Vertical filling machines are essential tools in various industries, particularly in packaging and manufacturing. These machines ensure precise and efficient filling of different products into containers, significantly enhancing productivity and consistency. This article delves into six types of vertical filling machines, highlighting their features, applications, and benefits. If you need more styles and functions, please contact us in time. The article only shows some machines. We have a strong factory, professional technicians, and accept customization. Any needs of customers can be solved.
1. Lipstick Filling Machine
Lipstick filling machines are specialized equipment designed to handle the delicate process of filling lipstick molds with the melted product. These machines are crucial in the cosmetics industry, where precision and hygiene are paramount.
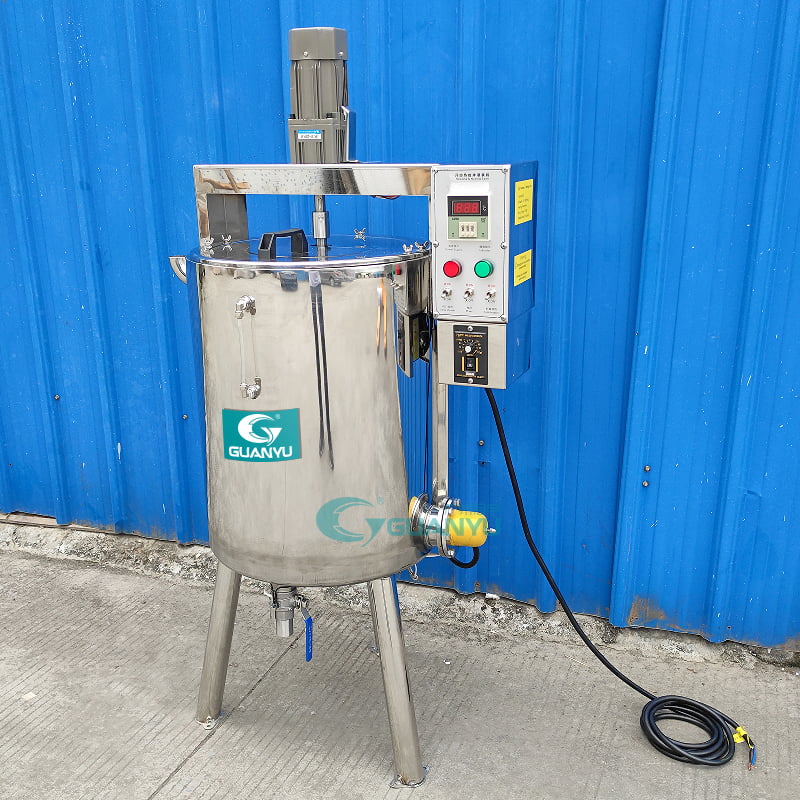
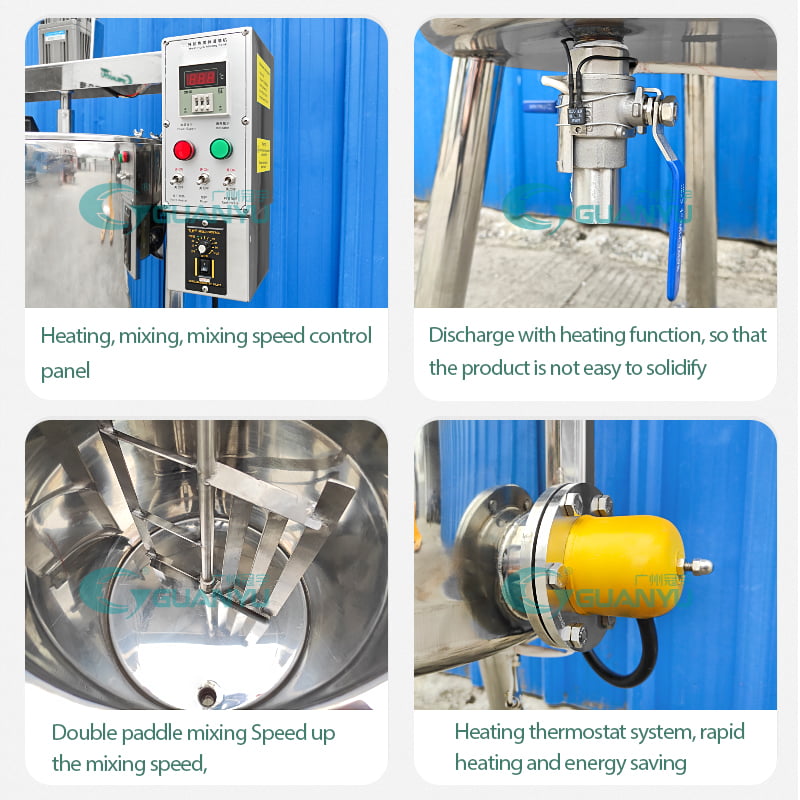
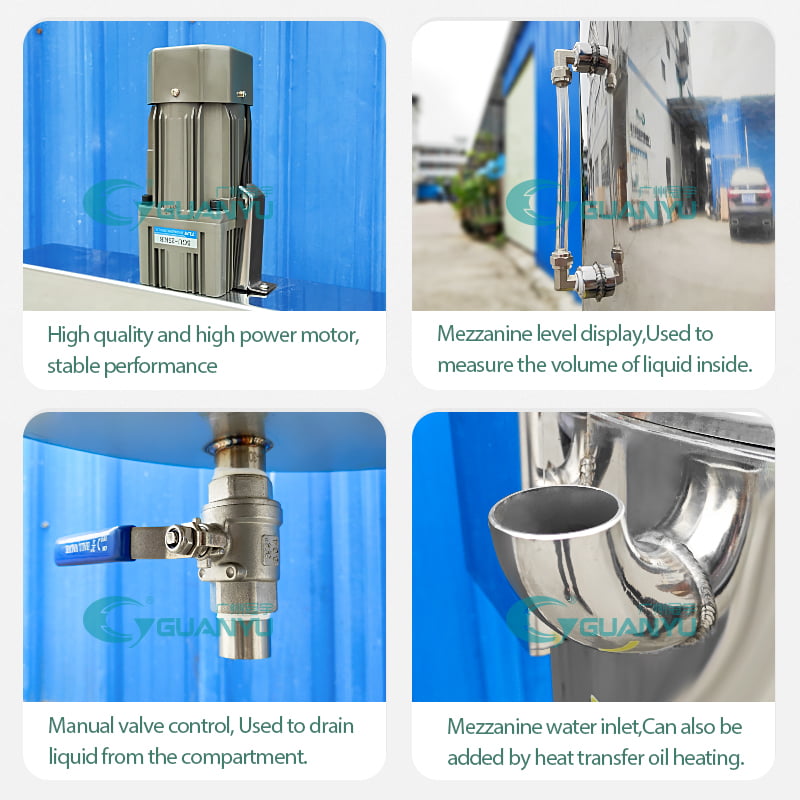
Features:
- Precision: Lipstick filling machines are equipped with precise dosing systems to ensure each mold is filled with the exact amount of product, maintaining uniformity across batches.
- Heating System: They have integrated heating systems to keep the product at the ideal temperature for filling, preventing clogging and ensuring smooth operation.
- Customization: These machines often allow customization in terms of mold shapes and sizes, accommodating various lipstick designs.
Applications:
Lipstick filling machines are used by cosmetics manufacturers to produce a wide range of lipstick products, from traditional solid lipsticks to liquid and gel-based variations.
Benefits:
- Consistency: Ensures each lipstick has the same volume and appearance.
- Efficiency: Automates the filling process, reducing manual labor and increasing production speed.
- Quality: Maintains product quality by preventing contamination and ensuring proper temperature control.
2. Quantitative Powder Vertical Filling Machine
Quantitative powder vertical filling machines are designed to handle the filling of powdered products with high accuracy. These machines are essential in industries such as food, pharmaceuticals, and chemicals.
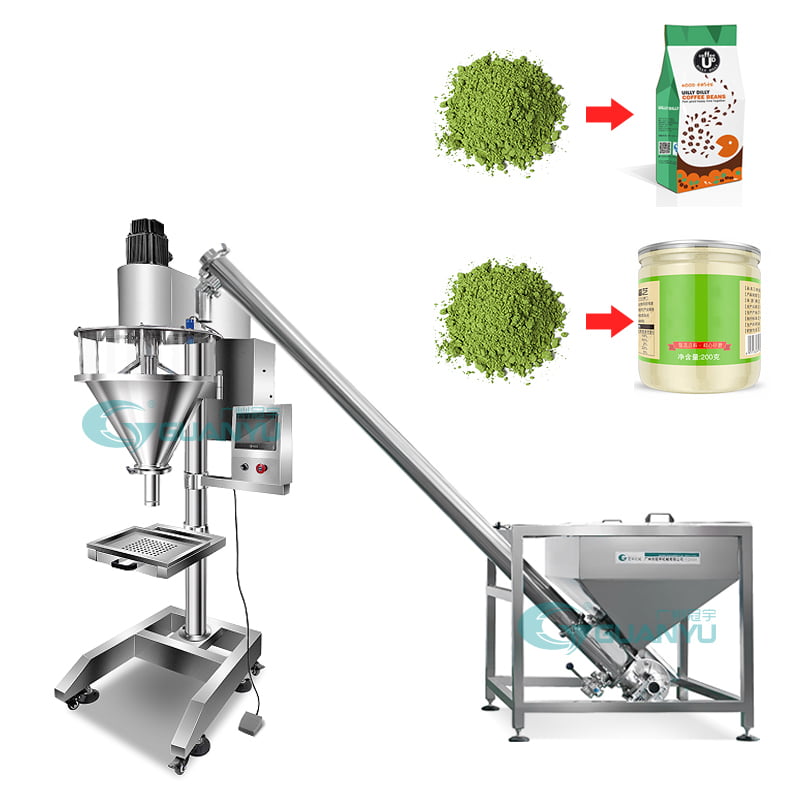
Features:
- High Precision: Utilizes advanced weighing and dosing systems to ensure accurate filling of powders.
- Versatility: Can handle various types of powders, including fine, coarse, and granulated materials.
- Dust Control: Equipped with dust extraction systems to maintain a clean working environment and prevent product loss.
Applications:
These machines are widely used for filling spices, flour, powdered supplements, and chemical powders into containers such as bottles, jars, and sachets.
Benefits:
- Accuracy: Ensures precise measurements, reducing waste and ensuring product consistency.
- Hygiene: Maintains a clean filling process, essential for food and pharmaceutical products.
- Productivity: Speeds up the filling process, allowing for higher production volumes.
3. Sealed Vertical Filling Machine
Sealed vertical filling machines are designed to fill and seal containers in one integrated process. These machines are commonly used in the food and beverage industry to package products that require airtight sealing.
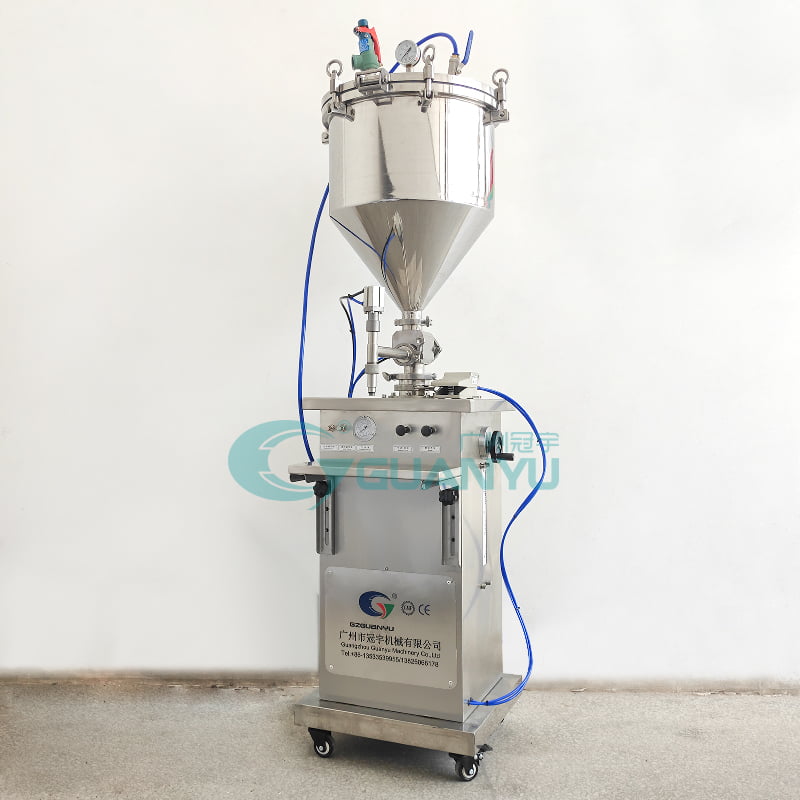
Features:
- Integrated Sealing: Combines filling and sealing operations, ensuring a streamlined process.
- Airtight Seals: Ensures containers are sealed tightly to prevent leakage and contamination.
- Automated Operation: Features automated controls for precise filling and sealing, reducing the need for manual intervention.
Applications:
These machines are ideal for packaging liquid products like juices, sauces, and soups, as well as semi-liquid products like yogurt and puddings.
Benefits:
- Preservation: Ensures products remain fresh by preventing exposure to air and contaminants.
- Efficiency: Automates the packaging process, increasing production speed and reducing labor costs.
- Versatility: Can handle a wide range of container sizes and types.
4. Pneumatic Ball Valve Filling Machine
Pneumatic ball valve filling machines are specialized for filling thick, viscous liquids and pastes. These machines use pneumatic systems to control the flow of the product, ensuring accurate filling.
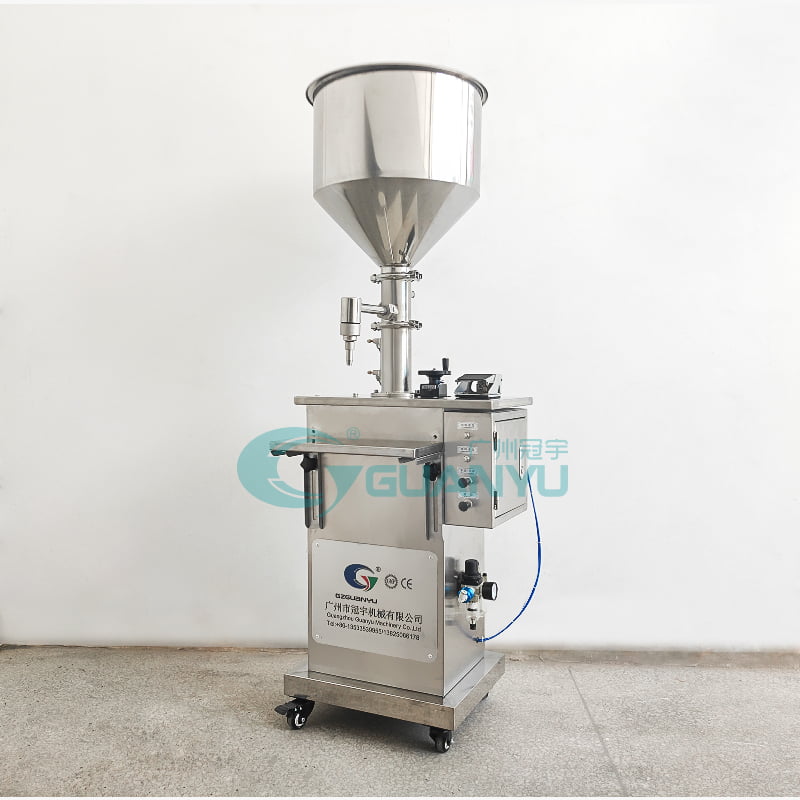

Features:
- Pneumatic Control: Utilizes pneumatic ball valves to manage the flow of viscous products, providing precise control.
- Durability: Constructed with robust materials to handle the wear and tear of filling thick substances.
- Adjustable Filling Speed: Allows operators to adjust the filling speed based on the product’s viscosity and production requirements.
Applications:
These machines are commonly used in industries such as food (for sauces, honey, and syrups), cosmetics (for creams and gels), and chemicals (for adhesives and sealants).
Benefits:
- Precision: Ensures accurate filling of viscous products, minimizing waste and spillage.
- Reliability: Durable construction ensures long-term operation with minimal maintenance.
- Flexibility: Can handle a variety of thick products, making it versatile for different industries.
5. Liquid and Paste Dual-Purpose Filling Machine
Liquid and paste dual-purpose filling machines are designed to handle both liquid and paste products, providing flexibility for manufacturers who need to fill different types of products using one machine.

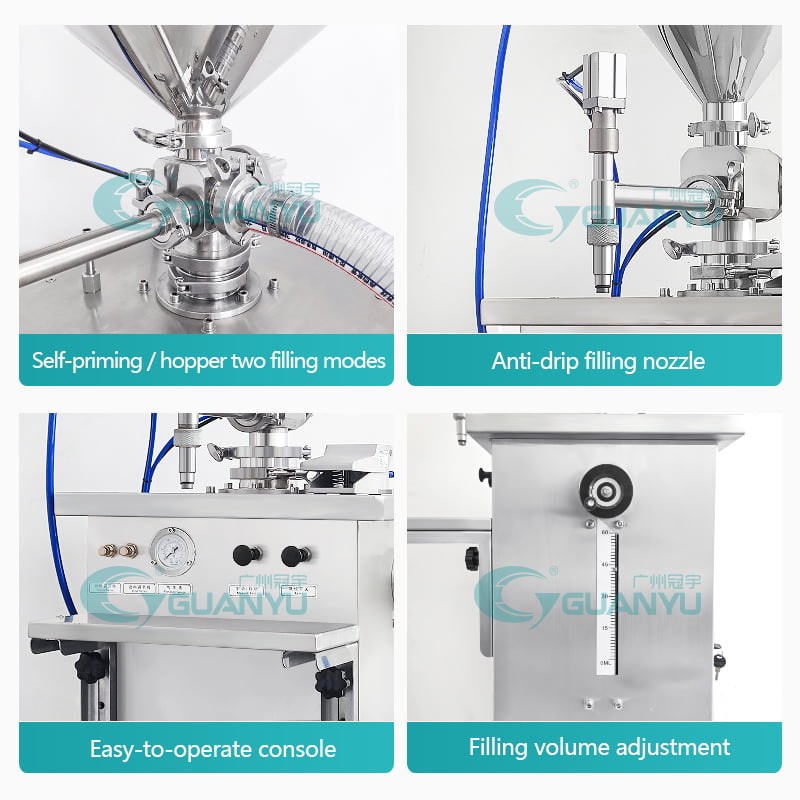
Features:
- Dual-Purpose Design: Capable of filling both liquid and paste products, reducing the need for multiple machines.
- Easy Changeover: Features quick-change components that allow operators to switch between filling liquids and pastes with minimal downtime.
- Accurate Filling: Equipped with precise dosing mechanisms to ensure consistent filling volumes for both liquids and pastes.
Applications:
These machines are ideal for manufacturers who produce a variety of products, such as sauces, lotions, shampoos, and creams.
Benefits:
- Cost-Effective: Reduces the need for multiple machines, saving on equipment costs and space.
- Versatility: Handles a wide range of products, enhancing production flexibility.
- Efficiency: Streamlines production by allowing quick transitions between different product types.
6. Self-Priming Two-End Filling Machine
Self-priming two-end filling machines are designed for high-speed filling operations, featuring self-priming capabilities that ensure a continuous supply of the product to the filling heads. These machines are suitable for both liquid and semi-liquid products.
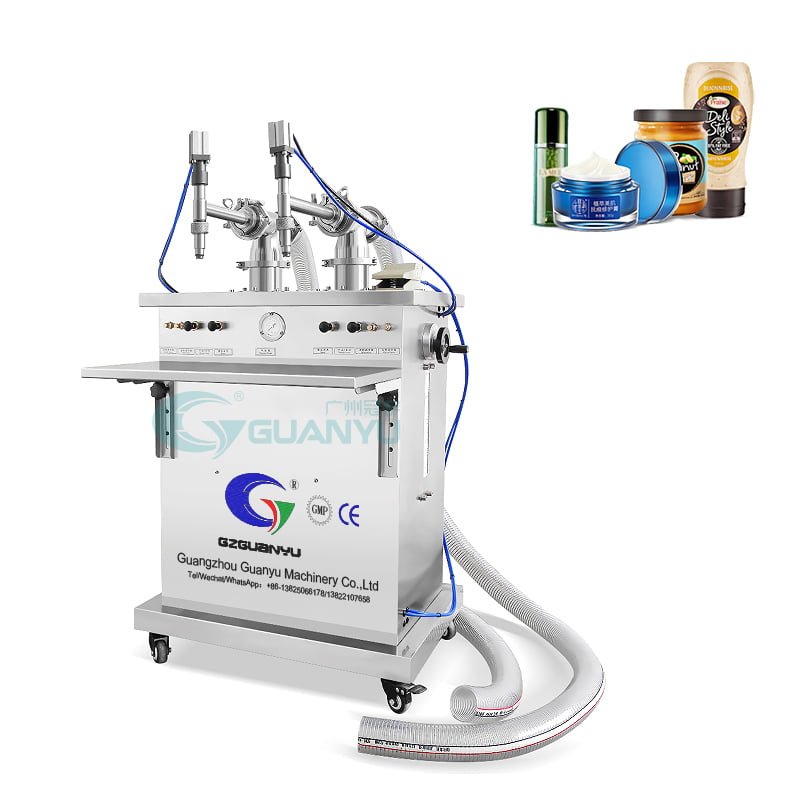
Features:
- Self-Priming System: Ensures a consistent flow of product to the filling heads, reducing the risk of interruptions.
- Two-End Filling: Allows for simultaneous filling of two containers, doubling the filling speed.
- Automated Controls: Equipped with advanced control systems for precise and efficient operation.
Applications:
These machines are commonly used in the food and beverage industry (for filling bottles with water, juice, or oil), the cosmetics industry (for filling bottles with shampoos and conditioners), and the chemical industry (for filling containers with cleaning agents and solvents).
Benefits:
- Speed: Significantly increases filling speed, enhancing overall productivity.
- Consistency: Ensures uniform filling across all containers, maintaining product quality.
- Efficiency: Reduces downtime and increases throughput with its self-priming and dual-end design.
Conclusion
Vertical filling machines play a crucial role in modern manufacturing and packaging processes, offering precision, efficiency, and versatility. Each type of machine is designed to meet specific industry needs, from cosmetics to food and chemicals, ensuring that products are filled accurately and efficiently. By understanding the features and benefits of these machines, manufacturers can make informed decisions to optimize their production lines and enhance overall productivity.
Howdy! Do you know if they make any plugins to assist with Search Engine Optimization? I’m
trying to get my blog to rank for some targeted keywords but I’m not seeing very good gains.
If you know of any please share. Thanks! You can read similar art here: Bij nl
Hey there! Do you know if they make any plugins to assist with Search Engine Optimization? I’m trying to get my site to rank for some targeted keywords
but I’m not seeing very good results. If you know of any please share.
Kudos! I saw similar text here: Code of destiny
I’m really impressed with your writing abilities as smartly as with the layout in your blog. Is this a paid theme or did you customize it yourself? Anyway stay up the excellent high quality writing, it is rare to peer a nice blog like this one nowadays. I like guanyugz.com ! My is: LinkedIN Scraping
I’m extremely inspired along with your writing talents as neatly as with the layout for your weblog. Is that this a paid topic or did you modify it your self? Either way stay up the excellent quality writing, it is uncommon to peer a great weblog like this one nowadays. I like guanyugz.com ! It is my: TikTok Algorithm