In today’s fast-paced manufacturing environment, the demand for efficient and high-quality production processes has never been greater, particularly in the liquid cleaning products sector. A fully automated production line is essential for meeting consumer expectations and regulatory standards. This article will explore the various components of such a shampoo production line, detailing their functions, benefits, and the overall impact on the manufacturing of liquid cleaning products.
Shampoo Production Line
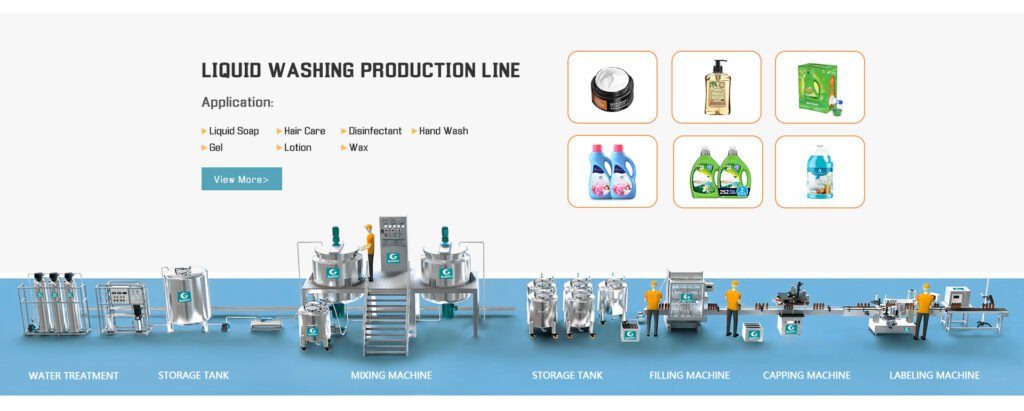
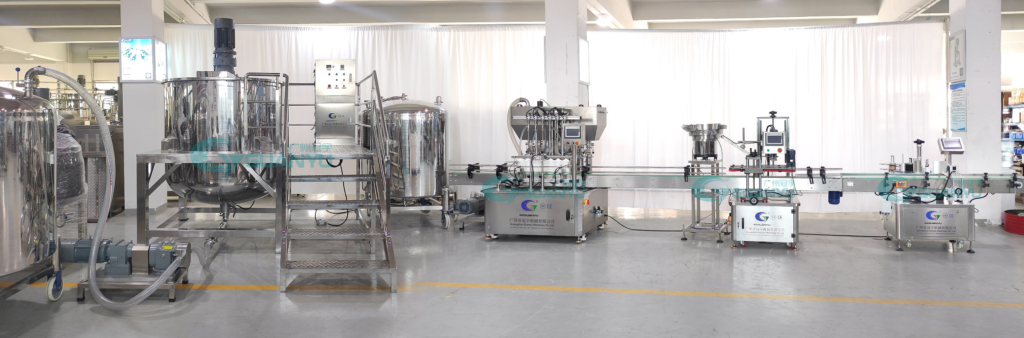
1. Raw Material Handling and Mixing Equipment
The production of liquid cleaning products begins with raw materials, which require careful handling and precise mixing.
- Ingredient Storage Tanks: These tanks are vital for storing liquid raw materials, including surfactants, solvents, and fragrances. Designed to maintain ingredient integrity, they often feature temperature controls and are constructed from materials resistant to corrosion. This ensures that the raw materials remain pure and safe for use in formulations.
- Mixing Tanks/Stirring Tanks: After the raw materials are measured, they are transferred to mixing tanks. These tanks are equipped with powerful agitators that ensure thorough mixing of ingredients. The ability to control temperature through heating and cooling jackets is crucial, as many chemical reactions require specific conditions to achieve optimal results.
- Weighing Systems: Precision is key in the formulation of cleaning products. Automated weighing systems allow for real-time measurement of ingredients, reducing human error and ensuring that each batch maintains the same quality and characteristics. This level of accuracy is critical for both performance and regulatory compliance.
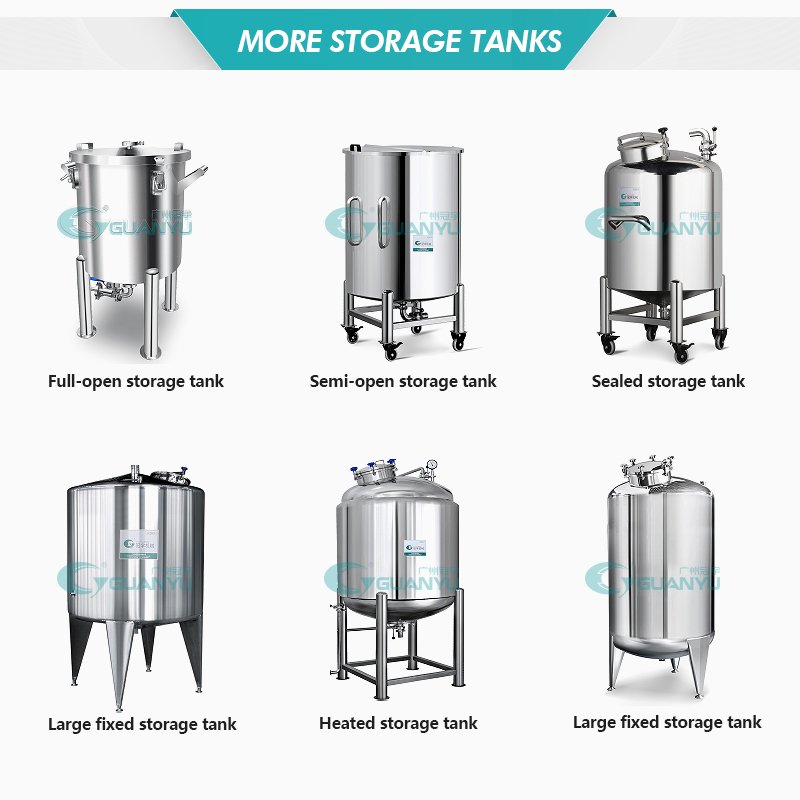
2. Conveying Systems
Efficient transport of materials throughout the production line is essential to maintain workflow and minimize downtime.
- Pipes and Pumps: These are essential for transferring blended liquids to filling machines. The choice of pumps depends on the viscosity and chemical properties of the products, ensuring safe and effective transfer without contamination.
- Conveyor Belts: Automated conveyor systems are used to move containers through different stages of production. These systems help reduce manual labor and enhance the speed of operations, facilitating a seamless transition from one phase to the next.
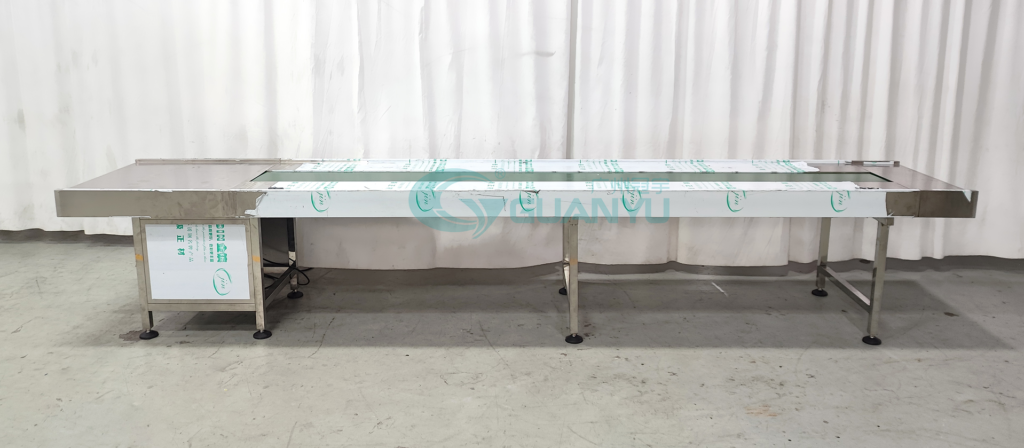
3. Filling Equipment
The filling stage is where the liquid cleaning products are packaged into their final containers.
- Filling Machines: Depending on the nature of the liquid, different types of filling machines may be used. For instance, piston pump fillers are ideal for viscous products, while peristaltic pumps are suitable for more delicate formulations. Selecting the right filling equipment is essential for achieving precise fill levels and minimizing waste.
- Multi-Head Filling Systems: To maximize efficiency, many production lines incorporate multi-head filling systems. These allow for simultaneous filling of multiple containers, significantly increasing the production rate and reducing cycle times.
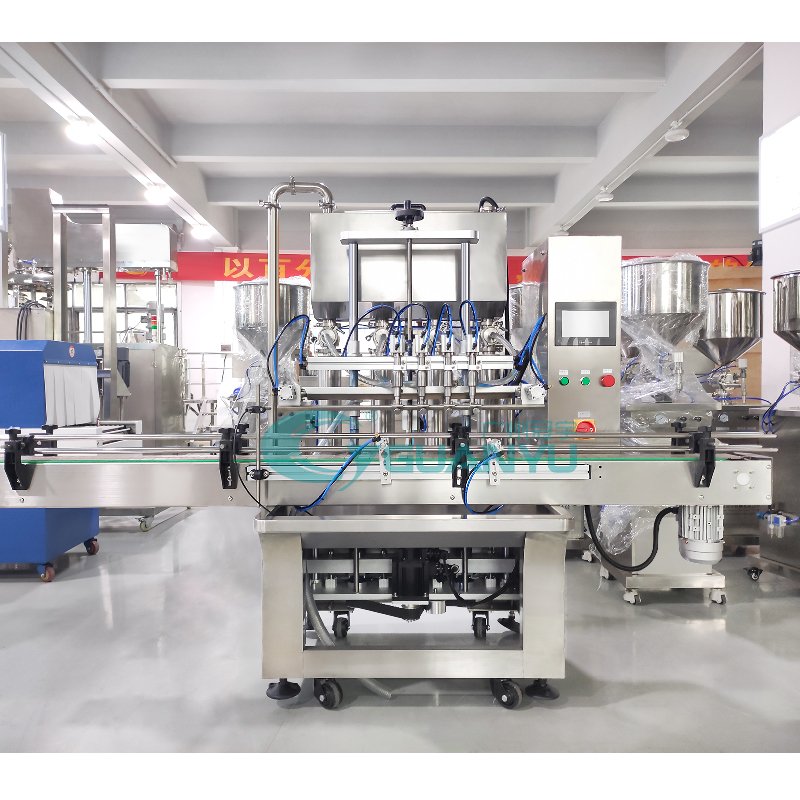
4. Sealing Equipment
After filling, it is crucial to seal the bottles properly to maintain product integrity.
- Sealing Machines: Various sealing technologies, such as capping machines and foil sealers, are utilized depending on the container type. These machines ensure that products remain uncontaminated and retain their quality throughout their shelf life.
- Automatic Cap Sorters: These devices streamline the capping process by automatically organizing and placing caps onto bottles. This automation reduces labor costs and enhances operational efficiency.
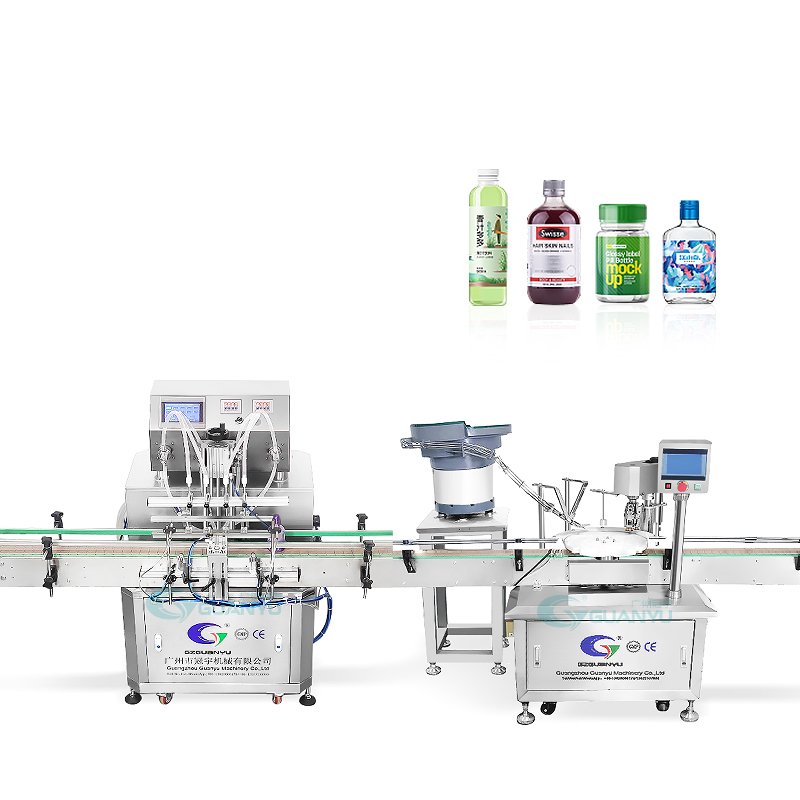
5. Labeling and Coding Equipment
Effective labeling and coding are critical for compliance and consumer information.
- Labeling Machines: Automatic labeling machines efficiently apply labels to containers, ensuring accurate placement and adherence. This is particularly important for branding and regulatory requirements, as labels must contain specific information.
- Coding Machines/Inkjet Printers: These machines print vital information, including batch numbers and expiration dates, directly onto the product. This coding is essential for traceability and compliance with health regulations.

6. Packaging Equipment
Once the products are sealed and labeled, they must be packaged for distribution.
- Shrink Wrapping Machines: These machines wrap finished bottles in plastic film, providing additional protection during transportation and enhancing shelf appeal. The shrink-wrapping process ensures that products remain secure and tamper-proof.
- Cartoning Machines: These automated machines package individual bottles into cartons, facilitating efficient shipping and storage. By automating this process, manufacturers can ensure that products are packaged consistently and securely.
- Case Sealers: Finally, case sealers are used to close cardboard boxes containing multiple cartons of the product. This step is essential for maintaining the integrity of the products during transport and storage.
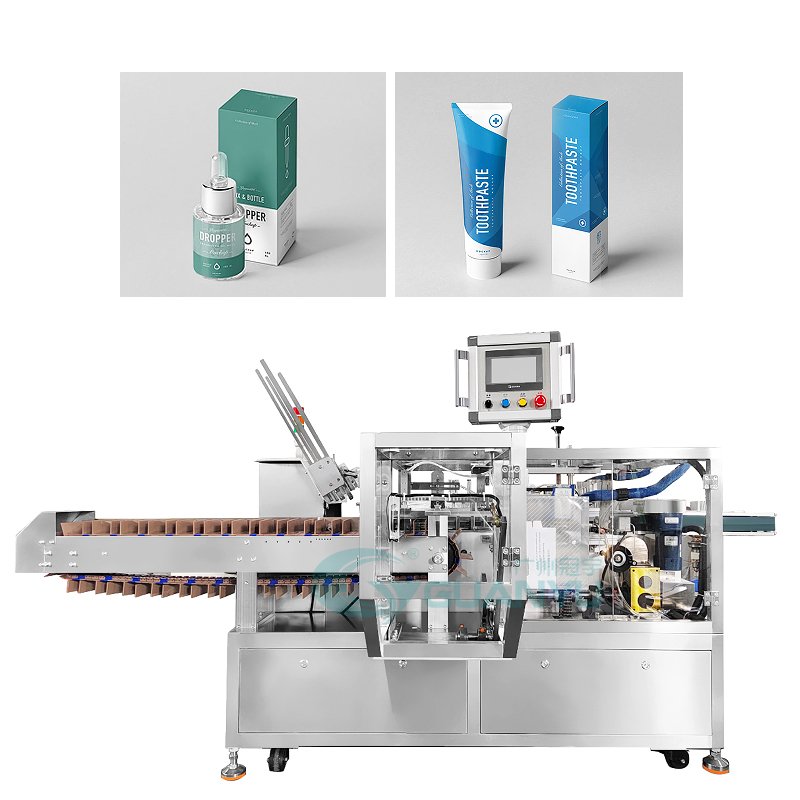
7. Inspection Equipment
Quality control is a fundamental aspect of the production process.
- Level Detectors: These systems monitor the liquid levels in each bottle to ensure compliance with specifications. Consistent fill levels are vital for maintaining product quality and consumer trust.
- Weight Check Machines: Automated weight check systems verify that each filled bottle meets established weight standards. This quality control step prevents financial losses due to underfilled containers and ensures regulatory compliance.
- Visual Inspection Systems: Advanced inspection systems use cameras to check the appearance of labels and the overall quality of the bottles. By identifying defects early in the process, manufacturers can maintain high-quality standards and avoid costly recalls.
8. Auxiliary Equipment
To support the production line, several auxiliary systems are necessary.
- Air Compressors: These provide pneumatic power for various production line equipment, enhancing efficiency and performance. Proper maintenance of these systems is essential for continuous operation.
- CIP (Clean-In-Place) Systems: Hygiene is crucial in manufacturing cleaning products. CIP systems allow for the internal cleaning of production line components without disassembly, ensuring that all equipment remains sanitary and compliant with health regulations.
Conclusion
A fully automated production line for liquid cleaning products is a complex yet efficient system that integrates various specialized equipment to ensure quality, speed, and safety throughout the manufacturing process. Each component, from raw material handling to final packaging, plays a vital role in delivering high-quality products that meet consumer expectations and regulatory standards.
The integration of automation not only enhances productivity but also improves consistency and reduces the potential for human error. As the liquid cleaning products market continues to grow, manufacturers who invest in advanced production technologies will be better positioned to meet increasing demand while maintaining high standards of quality and safety. By embracing innovation, these companies can thrive in a competitive landscape, delivering effective and reliable cleaning solutions to consumers worldwide.
I don’t think the title of your article matches the content lol. Just kidding, mainly because I had some doubts after reading the article.
I don’t think the title of your article matches the content lol. Just kidding, mainly because I had some doubts after reading the article.
Can you be more specific about the content of your article? After reading it, I still have some doubts. Hope you can help me.
Your point of view caught my eye and was very interesting. Thanks. I have a question for you.
Can you be more specific about the content of your article? After reading it, I still have some doubts. Hope you can help me. https://www.binance.info/join?ref=P9L9FQKY
I don’t think the title of your article matches the content lol. Just kidding, mainly because I had some doubts after reading the article.
Your article helped me a lot, is there any more related content? Thanks!
Thank you for your sharing. I am worried that I lack creative ideas. It is your article that makes me full of hope. Thank you. But, I have a question, can you help me?
Your point of view caught my eye and was very interesting. Thanks. I have a question for you.
Thank you for your sharing. I am worried that I lack creative ideas. It is your article that makes me full of hope. Thank you. But, I have a question, can you help me?
Thanks for sharing. I read many of your blog posts, cool, your blog is very good. https://accounts.binance.info/en/register-person?ref=JHQQKNKN
Thank you for your sharing. I am worried that I lack creative ideas. It is your article that makes me full of hope. Thank you. But, I have a question, can you help me?
Your article helped me a lot, is there any more related content? Thanks!
Your point of view caught my eye and was very interesting. Thanks. I have a question for you.
Can you be more specific about the content of your article? After reading it, I still have some doubts. Hope you can help me.
Can you be more specific about the content of your article? After reading it, I still have some doubts. Hope you can help me.
Thanks for sharing. I read many of your blog posts, cool, your blog is very good.
Your article helped me a lot, is there any more related content? Thanks!
Thank you, your article surprised me, there is such an excellent point of view. Thank you for sharing, I learned a lot.
Can you be more specific about the content of your article? After reading it, I still have some doubts. Hope you can help me.
Thank you for your sharing. I am worried that I lack creative ideas. It is your article that makes me full of hope. Thank you. But, I have a question, can you help me?
Thanks for sharing. I read many of your blog posts, cool, your blog is very good.
Thanks for sharing. I read many of your blog posts, cool, your blog is very good.
Thanks for sharing. I read many of your blog posts, cool, your blog is very good.
I don’t think the title of your article matches the content lol. Just kidding, mainly because I had some doubts after reading the article.
Your point of view caught my eye and was very interesting. Thanks. I have a question for you. https://www.binance.com/id/register?ref=GJY4VW8W
Your article helped me a lot, is there any more related content? Thanks!
Your article helped me a lot, is there any more related content? Thanks!