Introduction to Industrial Soap Production
The production of long bar soap in an industrial setting requires a combination of precision, efficiency, and the right equipment. One of the most crucial pieces of equipment in this process is the mixing pot. This vessel is where the raw ingredients—such as fats, oils, lye, and additives—are combined and processed to form the soap base. Selecting the appropriate mixing pot can significantly influence the quality, consistency, and productivity of soap manufacturing. This article explores the essential considerations when choosing a mixing pot for industrial soap production and highlights the types of mixing pots that are most suitable for this purpose.
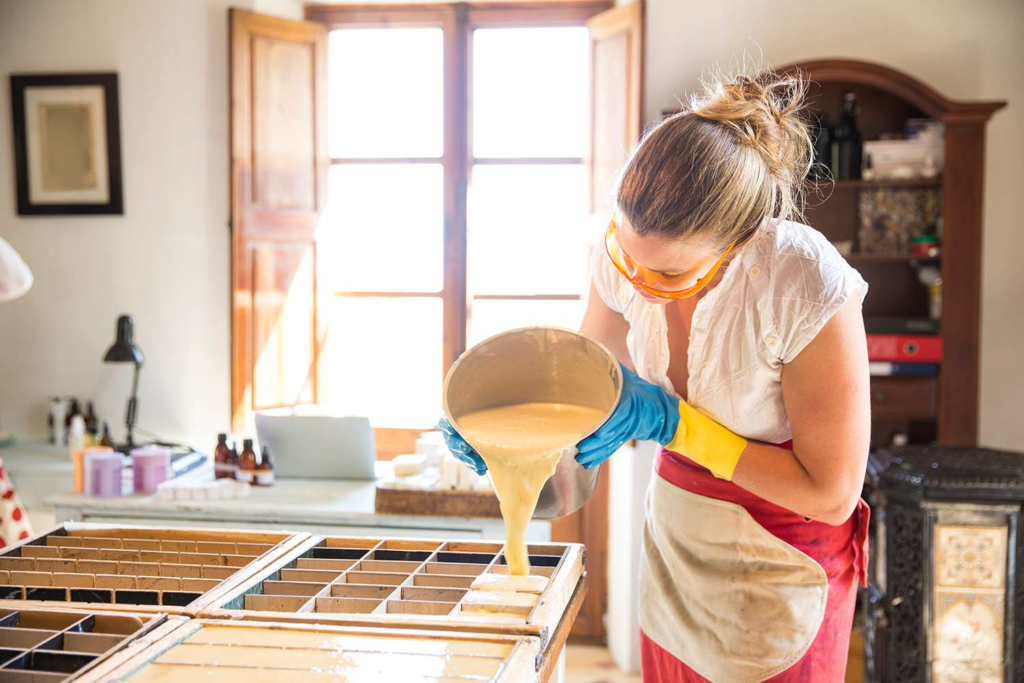
Essential Considerations for Selecting a Mixing Pot
When selecting a mixing pot for the industrial production of long bar soap, several factors need to be considered to ensure optimal performance and product quality. These factors include material compatibility, capacity, mixing capabilities, and heating options.
Material Compatibility
The materials used in constructing the mixing pot must be compatible with the soap ingredients. Stainless steel is often the preferred choice due to its corrosion resistance, durability, and ease of cleaning. Stainless steel can withstand the caustic nature of lye and the high temperatures required during soap production. Additionally, it does not react with oils and additives, ensuring that the final soap product remains pure and uncontaminated.
Capacity and Scalability
The capacity of the mixing pot should align with the production scale of the facility. Industrial soap production typically involves large batches, so the mixing pot must be able to handle significant volumes of ingredients. It’s important to choose a pot that not only meets current production needs but also allows for scalability. A pot that is too small can bottleneck the production process, while a pot that is too large may lead to inefficiencies and increased energy consumption.
Mixing Capabilities
Effective mixing is crucial to achieving a homogeneous soap mixture. The mixing pot should be equipped with a powerful and efficient mixing mechanism that can handle the viscosity of the soap mixture. Common mixing mechanisms include paddle mixers, turbine mixers, and anchor agitators. Paddle mixers are suitable for low to medium-viscosity mixtures, while turbine mixers and anchor agitators are better suited for high-viscosity mixtures. The choice of mixer should ensure that all ingredients are thoroughly blended without introducing excessive air, which can affect the texture and quality of the soap.
Heating Options
Heating is an integral part of the soap-making process, as it facilitates the saponification reaction between fats and lye. Mixing pots may come with built-in heating elements or jackets that allow for precise temperature control. Electric heating elements are common in smaller setups, while steam jackets are often used in larger industrial settings due to their efficiency in maintaining consistent temperatures. The ability to control the temperature accurately is vital to ensure that the soap mixture reaches the appropriate consistency and that the saponification process completes successfully.
When selecting a mixing pot for the industrial production of long bar soap, several factors need to be considered to ensure optimal performance and product quality. These factors include material compatibility, capacity, mixing capabilities, and heating options.
Material Compatibility
The materials used in constructing the mixing pot must be compatible with the soap ingredients. Stainless steel is often the preferred choice due to its corrosion resistance, durability, and ease of cleaning. Stainless steel can withstand the caustic nature of lye and the high temperatures required during soap production. Additionally, it does not react with oils and additives, ensuring that the final soap product remains pure and uncontaminated.
Capacity and Scalability
The capacity of the mixing pot should align with the production scale of the facility. Industrial soap production typically involves large batches, so the mixing pot must be able to handle significant volumes of ingredients. It’s important to choose a pot that not only meets current production needs but also allows for scalability. A pot that is too small can bottleneck the production process, while a pot that is too large may lead to inefficiencies and increased energy consumption.
Mixing Capabilities
Effective mixing is crucial to achieving a homogeneous soap mixture. The mixing pot should be equipped with a powerful and efficient mixing mechanism that can handle the viscosity of the soap mixture. Common mixing mechanisms include paddle mixers, turbine mixers, and anchor agitators. Paddle mixers are suitable for low to medium-viscosity mixtures, while turbine mixers and anchor agitators are better suited for high-viscosity mixtures. The choice of mixer should ensure that all ingredients are thoroughly blended without introducing excessive air, which can affect the texture and quality of the soap.
Heating Options
Heating is an integral part of the soap-making process, as it facilitates the saponification reaction between fats and lye. Mixing pots may come with built-in heating elements or jackets that allow for precise temperature control. Electric heating elements are common in smaller setups, while steam jackets are often used in larger industrial settings due to their efficiency in maintaining consistent temperatures. The ability to control the temperature accurately is vital to ensure that the soap mixture reaches the appropriate consistency and that the saponification process completes successfully.
When selecting a mixing pot for the industrial production of long bar soap, several factors need to be considered to ensure optimal performance and product quality. These factors include material compatibility, capacity, mixing capabilities, and heating options.
Material Compatibility
The materials used in constructing the mixing pot must be compatible with the soap ingredients. Stainless steel is often the preferred choice due to its corrosion resistance, durability, and ease of cleaning. Stainless steel can withstand the caustic nature of lye and the high temperatures required during soap production. Additionally, it does not react with oils and additives, ensuring that the final soap product remains pure and uncontaminated.
Capacity and Scalability
The capacity of the mixing pot should align with the production scale of the facility. Industrial soap production typically involves large batches, so the mixing pot must be able to handle significant volumes of ingredients. It’s important to choose a pot that not only meets current production needs but also allows for scalability. A pot that is too small can bottleneck the production process, while a pot that is too large may lead to inefficiencies and increased energy consumption.
Mixing Capabilities
Effective mixing is crucial to achieving a homogeneous soap mixture. The mixing pot should be equipped with a powerful and efficient mixing mechanism that can handle the viscosity of the soap mixture. Common mixing mechanisms include paddle mixers, turbine mixers, and anchor agitators. Paddle mixers are suitable for low to medium-viscosity mixtures, while turbine mixers and anchor agitators are better suited for high-viscosity mixtures. The choice of mixer should ensure that all ingredients are thoroughly blended without introducing excessive air, which can affect the texture and quality of the soap.
Heating Options
Heating is an integral part of the soap-making process, as it facilitates the saponification reaction between fats and lye. Mixing pots may come with built-in heating elements or jackets that allow for precise temperature control. Electric heating elements are common in smaller setups, while steam jackets are often used in larger industrial settings due to their efficiency in maintaining consistent temperatures. The ability to control the temperature accurately is vital to ensure that the soap mixture reaches the appropriate consistency and that the saponification process completes successfully.
Types of Mixing Pots Suitable for Soap Production
There are several types of mixing pots that can be used in the industrial production of long bar soap. Each type has its advantages and is suited to specific production requirements.
Stainless Steel Mixing Tanks
Stainless steel mixing tanks are the most commonly used vessels in industrial soap production. They offer durability, easy maintenance, and resistance to chemical reactions. These tanks often come with advanced features such as variable speed mixers, temperature control systems, and automated mixing cycles. Stainless steel tanks can be customized to meet specific production needs, making them versatile for different scales of operation.
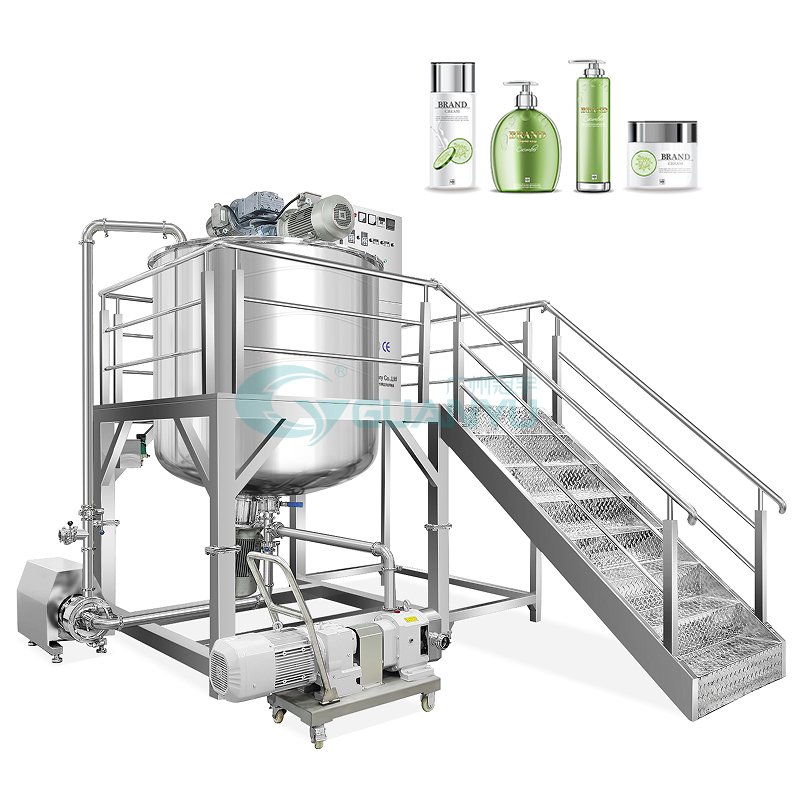
Jacketed mixing vessels are ideal for processes that require precise temperature control. These vessels have a double-walled construction with a space between the walls where heating or cooling fluids circulate. This design allows for uniform heating or cooling of the soap mixture, preventing hotspots and ensuring consistent quality. Jacketed vessels are particularly useful in large-scale soap production where maintaining a stable temperature is critical.
Vacuum Mixing Pots
Vacuum mixing pots are used in the production of high-quality soaps where air entrapment needs to be minimized. These pots create a vacuum environment during mixing, which helps remove air bubbles and achieve a denser, more uniform soap. Vacuum mixing is especially beneficial for transparent or specialty soaps that require a smooth and clear appearance. These pots often feature advanced controls and automation to manage the vacuum levels and mixing speeds.
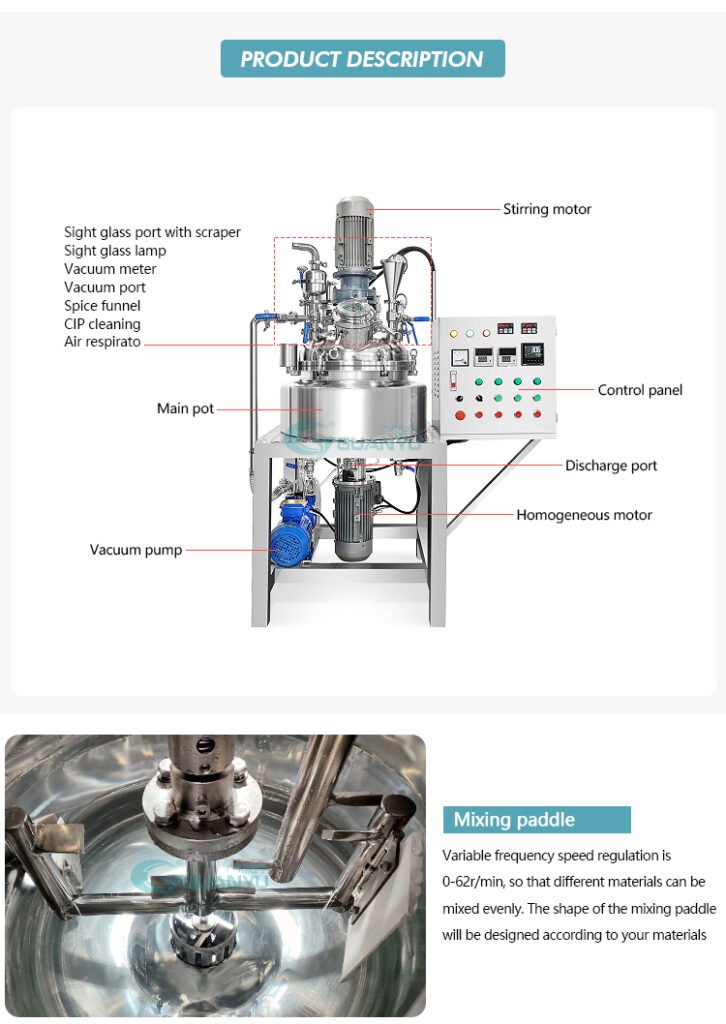
Agitated Pressure Vessels
Agitated pressure vessels combine mixing and pressure control, which can be advantageous in certain soap production processes. These vessels are designed to withstand high pressures, allowing for faster and more efficient saponification. The agitation system ensures thorough mixing, while the pressure environment can enhance the chemical reactions. This type of vessel is suitable for large-scale operations where time efficiency and product consistency are paramount.
Guanyu Company has all the machines and accepts customization.
our company ALIBABA website:
Guanyu company has sufficient strength and rich experience to solve
awesome
Howdy! This is my first visit to your blog! We are a team of volunteers and starting a new initiative in a community in the same niche. Your blog provided us valuable information to work on. You have done a marvellous job!
Thank you for any other informative web site. Where else could I am getting that kind of information written in such a perfect means? I’ve a project that I am just now running on, and I’ve been at the look out for such info.
These days of austerity and relative stress about taking on debt, lots of people balk against the idea of using a credit card in order to make purchase of merchandise as well as pay for any occasion, preferring, instead just to rely on this tried along with trusted means of making payment – hard cash. However, if you’ve got the cash there to make the purchase in full, then, paradoxically, that is the best time to use the cards for several causes.
I have seen many useful elements on your website about computers. However, I’ve got the impression that laptop computers are still not quite powerful more than enough to be a option if you typically do things that require lots of power, just like video touch-ups. But for website surfing, statement processing, and majority of other typical computer work they are fine, provided you don’t mind your little friend screen size. Thank you sharing your thinking.
After examine a few of the blog posts on your web site now, and I truly like your means of blogging. I bookmarked it to my bookmark website listing and can be checking back soon. Pls check out my web site as effectively and let me know what you think.
I’m not that much of a internet reader to be honest but your sites really nice, keep it up! I’ll go ahead and bookmark your website to come back down the road. Many thanks
Thanks for discussing your ideas. The one thing is that college students have a selection between federal student loan along with a private education loan where its easier to choose student loan consolidation than through the federal student loan.
Everyone loves what you guys are up too. Such clever work and coverage! Keep up the good works guys I’ve incorporated you guys to blogroll.
Hi, i feel that i noticed you visited my website so i came to ?go back the favor?.I’m attempting to find issues to improve my site!I suppose its adequate to make use of a few of your ideas!!
Thank you for sharing superb informations. Your web-site is very cool. I’m impressed by the details that you?ve on this website. It reveals how nicely you perceive this subject. Bookmarked this website page, will come back for extra articles. You, my friend, ROCK! I found simply the information I already searched everywhere and just couldn’t come across. What a great web site.
Heya this is kind of of off topic but I was wanting to know if blogs use WYSIWYG editors or if you have to manually code with HTML. I’m starting a blog soon but have no coding knowledge so I wanted to get guidance from someone with experience. Any help would be greatly appreciated!
I was curious if you ever thought of changing the page layout of your blog? Its very well written; I love what youve got to say. But maybe you could a little more in the way of content so people could connect with it better. Youve got an awful lot of text for only having one or two pictures. Maybe you could space it out better?
whoah this weblog is excellent i love studying your posts. Stay up the great work! You understand, many people are looking round for this info, you can aid them greatly.
I have observed that car insurance providers know the automobiles which are liable to accidents along with other risks. They also know what types of cars are susceptible to higher risk as well as higher risk they’ve got the higher your premium charge. Understanding the very simple basics connected with car insurance will let you choose the right sort of insurance policy that will take care of the needs you have in case you become involved in an accident. Many thanks sharing your ideas for your blog.
I’ve observed that in the world of today, video games are definitely the latest phenomenon with children of all ages. Periodically it may be not possible to drag your son or daughter away from the activities. If you want the best of both worlds, there are several educational gaming activities for kids. Great post.
I have observed that in the world the present day, video games will be the latest popularity with children of all ages. There are occassions when it may be out of the question to drag your son or daughter away from the video games. If you want the very best of both worlds, there are several educational activities for kids. Great post.
Greetings! I’ve been following your web site for some time now and finally got the courage to go ahead and give you a shout out from New Caney Texas! Just wanted to tell you keep up the fantastic work!
Very nice post. I simply stumbled upon your weblog and wished to say that I have truly enjoyed surfing around your weblog posts. In any case I?ll be subscribing in your feed and I hope you write once more very soon!
Pretty section of content. I just stumbled upon your website and in accession capital to assert that I get actually enjoyed account your blog posts. Any way I will be subscribing to your augment and even I achievement you access consistently rapidly.
Today, with the fast chosen lifestyle that everyone is having, credit cards have a huge demand throughout the economy. Persons out of every area of life are using credit card and people who not using the credit card have arranged to apply for one. Thanks for expressing your ideas in credit cards.
you’re really a good webmaster. The website loading speed is amazing. It seems that you’re doing any unique trick. Furthermore, The contents are masterpiece. you have done a wonderful job on this topic!
Thanks for this wonderful article. One other thing is that almost all digital cameras come equipped with the zoom lens so that more or less of any scene to get included by way of ‘zooming’ in and out. These changes in {focus|focusing|concentration|target|the a**** length are reflected while in the viewfinder and on big display screen right at the back of the particular camera.
Thanks for another informative web site. Where else could I get that kind of info written in such an ideal way? I have a project that I’m just now working on, and I’ve been on the look out for such information.
One more thing. In my opinion that there are many travel insurance web pages of trustworthy companies that let you enter holiday details and find you the rates. You can also purchase the international holiday insurance policy on the internet by using your credit card. Everything you should do should be to enter your own travel details and you can begin to see the plans side-by-side. Merely find the plan that suits your finances and needs then use your credit card to buy them. Travel insurance on the web is a good way to do investigation for a respectable company to get international travel cover. Thanks for expressing your ideas.
WONDERFUL Post.thanks for share..extra wait .. ?
Hi there, i read your blog occasionally and i own a similar one and i was just wondering if you get a lot of spam feedback? If so how do you stop it, any plugin or anything you can advise? I get so much lately it’s driving me mad so any assistance is very much appreciated.
Hmm it appears like your site ate my first comment (it was extremely long) so I guess I’ll just sum it up what I submitted and say, I’m thoroughly enjoying your blog. I too am an aspiring blog blogger but I’m still new to the whole thing. Do you have any helpful hints for beginner blog writers? I’d genuinely appreciate it.
I have realized that online education is getting popular because obtaining your college degree online has turned into a popular method for many people. Many people have not necessarily had a possible opportunity to attend a regular college or university yet seek the elevated earning potential and career advancement that a Bachelor Degree gives. Still other people might have a diploma in one field but wish to pursue a thing they already have an interest in.
Usually I don’t learn article on blogs, however I would like to say that this write-up very compelled me to check out and do it! Your writing style has been amazed me. Thanks, very great article.
Thanks for the interesting things you have uncovered in your post. One thing I would really like to reply to is that FSBO human relationships are built as time passes. By bringing out yourself to owners the first weekend their FSBO will be announced, prior to a masses start calling on Friday, you make a good relationship. By mailing them instruments, educational resources, free reports, and forms, you become a good ally. If you take a personal interest in them along with their problem, you build a solid network that, many times, pays off in the event the owners decide to go with a realtor they know plus trust — preferably you.
http://www.arttree.com.au is Australia Popular Online Art Store. We sell Canvas Prints & Handmade Canvas Oil Paintings. We Offer Up-to 70 Percent OFF Discount and FREE Delivery Australia, Sydney, Melbourne, Brisbane, Adelaide, Hobart and all regional areas.
check out https://s3.amazonaws.com/photovoltaik-buchloe/unlocking-the-secrets-of-photovoltaik-buchloe-a-complete-guide.html
Thanks for your publication. I also think laptop computers have become more and more popular nowadays, and now are sometimes the only sort of computer found in a household. This is because at the same time they are becoming more and more inexpensive, their processing power keeps growing to the point where there’re as robust as desktop computers through just a few years back.
hello!,I like your writing so much! share we communicate more about your article on AOL? I require an expert on this area to solve my problem. Maybe that’s you! Looking forward to see you.
Wow! This could be one particular of the most beneficial blogs We have ever arrive across on this subject. Actually Great. I’m also a specialist in this topic therefore I can understand your effort.
Woah! I’m really digging the template/theme of this website. It’s simple, yet effective. A lot of times it’s very hard to get that “perfect balance” between superb usability and visual appearance. I must say you’ve done a great job with this. In addition, the blog loads extremely fast for me on Firefox. Outstanding Blog!
Superb website you have here but I was wanting to know if you knew of any user discussion forums that cover the same topics discussed in this article? I’d really like to be a part of group where I can get feedback from other experienced individuals that share the same interest. If you have any recommendations, please let me know. Bless you!
F*ckin? tremendous things here. I?m very glad to see your article. Thanks a lot and i’m looking forward to contact you. Will you kindly drop me a mail?
Hi! Do you use Twitter? I’d like to follow you if that would be ok. I’m undoubtedly enjoying your blog and look forward to new posts.
http://www.mybudgetart.com.au is Australia’s Trusted Online Wall Art Canvas Prints Store. We are selling art online since 2008. We offer 1000+ artwork designs, up-to 50 OFF store-wide, Budget Pricing Wall Prints starts from $70, FREE Delivery Australia & New Zealand and World-wide shipping. Order Online your canvas prints today at mybudgetart.com.au
Thanks for the helpful content. It is also my opinion that mesothelioma has an particularly long latency period, which means that indication of the disease might not exactly emerge right up until 30 to 50 years after the initial exposure to asbestos fiber. Pleural mesothelioma, which is the most common kind and has an effect on the area round the lungs, could cause shortness of breath, chest muscles pains, along with a persistent cough, which may lead to coughing up bloodstream.
Along with everything that appears to be developing within this specific area, all your points of view are actually relatively refreshing. Nonetheless, I beg your pardon, because I can not give credence to your entire idea, all be it exhilarating none the less. It looks to me that your comments are not completely justified and in fact you are generally yourself not really totally confident of the point. In any case I did appreciate reading it.
Today, considering the fast life-style that everyone leads, credit cards get this amazing demand in the economy. Persons from every field are using the credit card and people who aren’t using the card have made arrangements to apply for one. Thanks for revealing your ideas about credit cards.
Today, with all the fast way of life that everyone leads, credit cards get this amazing demand throughout the market. Persons out of every arena are using the credit card and people who are not using the card have made up their minds to apply for one. Thanks for spreading your ideas on credit cards.
There’s noticeably a bundle to learn about this. I assume you made certain nice factors in features also.
I do like the way you have presented this particular challenge and it really does offer me personally some fodder for consideration. Nevertheless, because of what I have witnessed, I just simply wish as the actual remarks pack on that folks remain on point and don’t start on a soap box regarding the news du jour. All the same, thank you for this outstanding point and even though I can not agree with this in totality, I regard the viewpoint.
Your house is valueble for me. Thanks!?
http://www.factorytapestry.com is a Trusted Online Wall Hanging Tapestry Store. We are selling online art and decor since 2008, our digital business journey started in Australia. We sell 100 made-to-order quality printed soft fabric tapestry which are just too perfect for decor and gifting. We offer Up-to 50 percent OFF Storewide Sale across all the Wall Hanging Tapestries. We provide Fast Shipping USA, CAN, UK, EUR, AUS, NZ, ASIA and Worldwide Delivery across 100+ countries.
check out https://s3.ap-south-1.amazonaws.com/restumpingbendigo/ultimate-guide-to-restumping-in-bendigo-everything-you-need-to-know.html
Hiya! I just would like to give a huge thumbs up for the nice information you’ve gotten right here on this post. I can be coming again to your weblog for more soon.
Hi! This is kind of off topic but I need some guidance from an established blog. Is it difficult to set up your own blog? I’m not very techincal but I can figure things out pretty quick. I’m thinking about setting up my own but I’m not sure where to begin. Do you have any ideas or suggestions? Thanks
This design is wicked! You most certainly know how to keep a reader entertained. Between your wit and your videos, I was almost moved to start my own blog (well, almost…HaHa!) Wonderful job. I really loved what you had to say, and more than that, how you presented it. Too cool!
Thanks for your helpful post. In recent times, I have come to understand that the particular symptoms of mesothelioma cancer are caused by a build up of fluid involving the lining on the lung and the breasts cavity. The illness may start inside the chest region and spread to other parts of the body. Other symptoms of pleural mesothelioma include fat loss, severe deep breathing trouble, temperature, difficulty taking in food, and irritation of the face and neck areas. It needs to be noted that some people existing with the disease will not experience just about any serious indicators at all.
Fantastic beat ! I would like to apprentice even as you amend your site, how can i subscribe for a blog site? The account helped me a applicable deal. I had been tiny bit familiar of this your broadcast offered bright transparent concept
This web page is known as a walk-via for all the data you wanted about this and didn?t know who to ask. Glimpse here, and also you?ll positively uncover it.
Hi there would you mind stating which blog platform you’re working with? I’m looking to start my own blog in the near future but I’m having a hard time making a decision between BlogEngine/Wordpress/B2evolution and Drupal. The reason I ask is because your design seems different then most blogs and I’m looking for something unique. P.S Apologies for getting off-topic but I had to ask!
magnificent points altogether, you simply gained a brand new reader. What would you suggest in regards to your post that you made a few days ago? Any positive?
Hello! Do you know if they make any plugins to safeguard against hackers? I’m kinda paranoid about losing everything I’ve worked hard on. Any recommendations?
check out https://storage.googleapis.com/restumpingbendigo/restumping-revolution-modernizing-bendigo-properties.html
Nice post. I was checking continuously this blog and I’m impressed! Very useful info specially the last part 🙂 I care for such info a lot. I was seeking this certain information for a very long time. Thank you and best of luck.
You need to read https://storage.googleapis.com/concretedrivewaysinmelbourne/5-easy-steps-to-upgrade-your-concrete-driveway-in-melbourne.html
Howdy very cool web site!! Man .. Beautiful .. Wonderful .. I’ll bookmark your website and take the feeds also?I am happy to find so many useful information here within the submit, we need develop extra techniques on this regard, thanks for sharing. . . . . .
okmark your blog and check again here frequently. I am quite certain I will learn lots of new stuff right here! Good luck for the next!
I think that is one of the such a lot significant information for me. And i am satisfied studying your article. However should statement on few general things, The website taste is wonderful, the articles is in reality great : D. Good activity, cheers
naturally like your web site but you need to check the spelling on several of your posts. A number of them are rife with spelling problems and I find it very bothersome to tell the truth nevertheless I?ll surely come back again.
I will immediately grab your rss feed as I can’t find your email subscription link or e-newsletter service. Do you have any? Please let me know so that I could subscribe. Thanks.
I’m really impressed together with your writing skills and also with the structure on your weblog. Is this a paid subject matter or did you modify it your self? Either way keep up the nice quality writing, it is uncommon to see a great weblog like this one today..
Simply want to say your article is as amazing. The clearness for your publish is simply great and i can think you’re knowledgeable on this subject. Fine along with your permission let me to clutch your RSS feed to keep updated with imminent post. Thank you one million and please continue the rewarding work.
I appreciate, cause I found exactly what I was looking for. You have ended my four day long hunt! God Bless you man. Have a nice day. Bye
Thanks for expressing your ideas with this blog. Also, a misconception regarding the banking institutions intentions when talking about property foreclosure is that the standard bank will not have my installments. There is a fair bit of time that this bank is going to take payments every now and then. If you are also deep in the hole, they’re going to commonly call that you pay the payment completely. However, that doesn’t mean that they will have any sort of repayments at all. When you and the bank can manage to work some thing out, a foreclosure practice may halt. However, if you continue to pass up payments beneath new approach, the foreclosures process can pick up from where it left off.
Just read the article and I have to say—really well done. It was super informative, easy to follow, and actually learned a a few things new things. Definitely worth the read!
There are actually a whole lot of particulars like that to take into consideration. That could be a nice level to convey up. I offer the thoughts above as basic inspiration but clearly there are questions like the one you deliver up the place crucial thing might be working in sincere good faith. I don?t know if finest practices have emerged around issues like that, but I am positive that your job is clearly recognized as a fair game. Each boys and girls feel the influence of just a second?s pleasure, for the rest of their lives.
My brother suggested I would possibly like this blog. He was once entirely right. This put up actually made my day. You cann’t imagine simply how so much time I had spent for this information! Thanks!
Fantastic post but I was wondering if you could write a litte more on this topic? I’d be very grateful if you could elaborate a little bit further. Many thanks!
I have been exploring for a little bit for any high quality articles or weblog posts in this kind of area . Exploring in Yahoo I finally stumbled upon this site. Studying this info So i?m happy to exhibit that I have a very just right uncanny feeling I discovered exactly what I needed. I most for sure will make sure to do not fail to remember this site and give it a glance regularly.
One thing I want to comment on is that weightloss system fast can be achieved by the right diet and exercise. Your size not merely affects appearance, but also the general quality of life. Self-esteem, depressive disorder, health risks, along with physical capabilities are impacted in extra weight. It is possible to make everything right whilst still having a gain. In such a circumstance, a condition may be the primary cause. While a lot of food but not enough workout are usually responsible, common medical conditions and popular prescriptions can easily greatly add to size. Many thanks for your post here.
Hey very cool web site!! Man .. Excellent .. Amazing .. I’ll bookmark your site and take the feeds also?I’m happy to find a lot of useful info here in the post, we need work out more strategies in this regard, thanks for sharing. . . . . .
I can’t express how much I value the effort the author has put into creating this exceptional piece of content. The clarity of the writing, the depth of analysis, and the plethora of information offered are simply impressive. Her enthusiasm for the subject is evident, and it has definitely made an impact with me. Thank you, author, for sharing your wisdom and enlightening our lives with this extraordinary article!
From my notice, shopping for electronic products online can for sure be expensive, nevertheless there are some how-to’s that you can use to help you get the best products. There are always ways to uncover discount deals that could help make one to have the best electronic products products at the cheapest prices. Interesting blog post.
One thing I’d really like to say is that before acquiring more pc memory, have a look at the machine within which it can be installed. If your machine is actually running Windows XP, for instance, the actual memory limit is 3.25GB. Setting up greater than this would merely constitute any waste. Be sure that one’s mother board can handle the actual upgrade volume, as well. Good blog post.
I have learned result-oriented things from the blog post. One other thing I have discovered is that usually, FSBO sellers will probably reject anyone. Remember, they can prefer not to use your expert services. But if you actually maintain a comfortable, professional relationship, offering help and remaining in contact for four to five weeks, you will usually be capable of win a meeting. From there, a listing follows. Thanks a lot
I would like to thnkx for the efforts you have put in writing this site. I am hoping the same high-grade blog post from you in the upcoming also. Actually your creative writing abilities has inspired me to get my own blog now. Really the blogging is spreading its wings quickly. Your write up is a good example of it.
Have you ever considered publishing an e-book or guest authoring on other blogs? I have a blog based upon on the same topics you discuss and would love to have you share some stories/information. I know my audience would appreciate your work. If you’re even remotely interested, feel free to send me an e-mail.
There are actually loads of details like that to take into consideration. That could be a great level to deliver up. I supply the ideas above as basic inspiration however clearly there are questions just like the one you deliver up the place crucial factor can be working in trustworthy good faith. I don?t know if best practices have emerged round issues like that, but I’m positive that your job is clearly identified as a good game. Each boys and girls really feel the impact of only a moment?s pleasure, for the remainder of their lives.
I?m not sure where you’re getting your information, but great topic. I needs to spend some time learning more or understanding more. Thanks for fantastic information I was looking for this info for my mission.
magnificent post, very informative. I wonder why the other specialists of this sector don’t notice this. You should continue your writing. I’m sure, you have a huge readers’ base already!
I am very happy to read this. This is the kind of manual that needs to be given and not the accidental misinformation that’s at the other blogs. Appreciate your sharing this greatest doc.
Excellent beat ! I wish to apprentice while you amend your web site, how could i subscribe for a blog website? The account aided me a acceptable deal. I had been a little bit acquainted of this your broadcast provided bright clear idea
Many thanks for this article. I’d also like to talk about the fact that it can always be hard if you are in school and starting out to create a long credit rating. There are many individuals who are just trying to pull through and have a lengthy or beneficial credit history is often a difficult factor to have.
You could definitely see your skills in the paintings you write. The arena hopes for more passionate writers such as you who are not afraid to mention how they believe. Always follow your heart.
What?s Happening i’m new to this, I stumbled upon this I have found It positively useful and it has aided me out loads. I hope to contribute & help other users like its helped me. Great job.
Pretty section of content. I just stumbled upon your website and in accession capital to assert that I get actually enjoyed account your blog posts. Anyway I?ll be subscribing to your augment and even I achievement you access consistently quickly.
Thanks for the ideas you are discussing on this site. Another thing I’d like to say is getting hold of duplicates of your credit score in order to inspect accuracy of each detail is one first action you have to carry out in credit score improvement. You are looking to clear your credit file from harmful details problems that damage your credit score.
Hi there, I found your site via Google while looking for a related topic, your site came up, it looks great. I have bookmarked it in my google bookmarks.
Thanks for your post. What I want to comment on is that when searching for a good online electronics go shopping, look for a web site with total information on key elements such as the privacy statement, basic safety details, any payment methods, and various terms along with policies. Always take time to read the help along with FAQ segments to get a greater idea of how a shop performs, what they can perform for you, and how you can make the most of the features.
Great paintings! That is the type of information that are meant to be shared around the net. Shame on Google for not positioning this submit upper! Come on over and visit my site . Thank you =)
Thanks for every other informative blog. The place else may I am getting that type of information written in such a perfect method? I have a mission that I am simply now running on, and I’ve been on the glance out for such info.
Hello, i think that i saw you visited my weblog thus i came to ?return the favor?.I am trying to find things to enhance my website!I suppose its ok to use a few of your ideas!!
Wonderful paintings! This is the type of info that are meant to be shared across the web. Disgrace on the seek engines for no longer positioning this publish upper! Come on over and discuss with my site . Thank you =)
I believe one of your advertisements triggered my web browser to resize, you may well want to put that on your blacklist.
It?s really a cool and helpful piece of information. I am glad that you just shared this useful information with us. Please keep us informed like this. Thank you for sharing.
After I originally commented I clicked the -Notify me when new comments are added- checkbox and now every time a comment is added I get four emails with the same comment. Is there any means you’ll be able to take away me from that service? Thanks!
Just want to say your article is as surprising. The clarity in your post is simply cool and i can assume you are an expert on this subject. Fine with your permission allow me to grab your feed to keep updated with forthcoming post. Thanks a million and please continue the enjoyable work.
I have observed that in the world these days, video games are classified as the latest rage with children of all ages. Occasionally it may be out of the question to drag your kids away from the activities. If you want the very best of both worlds, there are many educational video games for kids. Great post.
Hello there! Do you know if they make any plugins to help with SEO? I’m trying to get my blog to rank for some targeted keywords but I’m not seeing very good results. If you know of any please share. Kudos!
Great blog here! Additionally your site a lot up fast! What host are you using? Can I get your associate hyperlink for your host? I want my web site loaded up as fast as yours lol
Thanks for your post. I also feel that laptop computers are getting to be more and more popular these days, and now in many cases are the only type of computer utilized in a household. Simply because at the same time actually becoming more and more very affordable, their processing power keeps growing to the point where there’re as highly effective as pc’s coming from just a few years back.
I like what you guys are up also. Such intelligent work and reporting! Carry on the superb works guys I have incorporated you guys to my blogroll. I think it’ll improve the value of my website 🙂
I am really inspired together with your writing skills as neatly as with the format on your blog. Is that this a paid subject matter or did you modify it yourself? Anyway stay up the excellent high quality writing, it?s uncommon to look a great weblog like this one today..
These days of austerity and also relative stress about running into debt, a lot of people balk against the idea of having a credit card to make acquisition of merchandise and also pay for a trip, preferring, instead only to rely on the particular tried in addition to trusted technique of making transaction – cash. However, if you have the cash available to make the purchase in full, then, paradoxically, that is the best time just to be able to use the credit card for several reasons.
What i don’t realize is actually how you are not actually much more well-liked than you may be right now. You’re very intelligent. You realize thus significantly relating to this subject, produced me personally consider it from a lot of varied angles. Its like women and men aren’t fascinated unless it is one thing to do with Lady gaga! Your own stuffs nice. Always maintain it up!
Thank you for another wonderful article. Where else could anyone get that type of info in such an ideal way of writing? I have a presentation next week, and I am on the look for such information.
Hey there! Do you know if they make any plugins to assist with Search Engine Optimization? I’m trying to get my blog to rank for some targeted keywords but I’m not seeing very good gains. If you know of any please share. Thank you!
Thanks for the ideas shared on your own blog. Something else I would like to talk about is that weight reduction is not exactly about going on a fad diet and trying to shed as much weight as you can in a couple of days. The most effective way in losing weight is by acquiring it slowly and following some basic guidelines which can provide help to make the most from your attempt to lose weight. You may recognize and already be following many of these tips, nonetheless reinforcing know-how never hurts.
Write more, thats all I have to say. Literally, it seems as though you relied on the video to make your point. You clearly know what youre talking about, why waste your intelligence on just posting videos to your weblog when you could be giving us something enlightening to read?
affordablecanvaspaintings.com.au is Australia Popular Online 100 percent Handmade Art Store. We deliver Budget Handmade Canvas Paintings, Abstract Art, Oil Paintings, Artwork Sale, Acrylic Wall Art Paintings, Custom Art, Oil Portraits, Pet Paintings, Building Paintings etc. 1000+ Designs To Choose From, Highly Experienced Artists team, Up-to 50 percent OFF SALE and FREE Delivery Australia, Sydney, Melbourne, Brisbane, Adelaide, Hobart and all regional areas. We ship worldwide international locations. Order Online Your Handmade Art Today.
deniz kucukkay
mehmet emre dinç
esteworld
medhair clinic
huseyin kandulu
dr basat
basat
ışık diş
şaban
terziler
salih emre
yelken
dr yelken
ahd clinic
adem köse
adem köse
Thank you for this article. I might also like to state that it can always be hard if you find yourself in school and simply starting out to initiate a long credit standing. There are many scholars who are just simply trying to make it through and have a good or favourable credit history can sometimes be a difficult matter to have.
basat
aslı tarcan global
terziler
adem köse