Sunscreen is a vital product that protects our skin from harmful UV rays, preventing sunburn, premature aging, and even skin cancer. But have you ever wondered how sunscreen is made? From formulating effective protection to ensuring a smooth texture, the manufacturing of sunscreen involves several key steps and components. In this article, we will walk you through the entire process, from selecting the ingredients to packaging the final product.
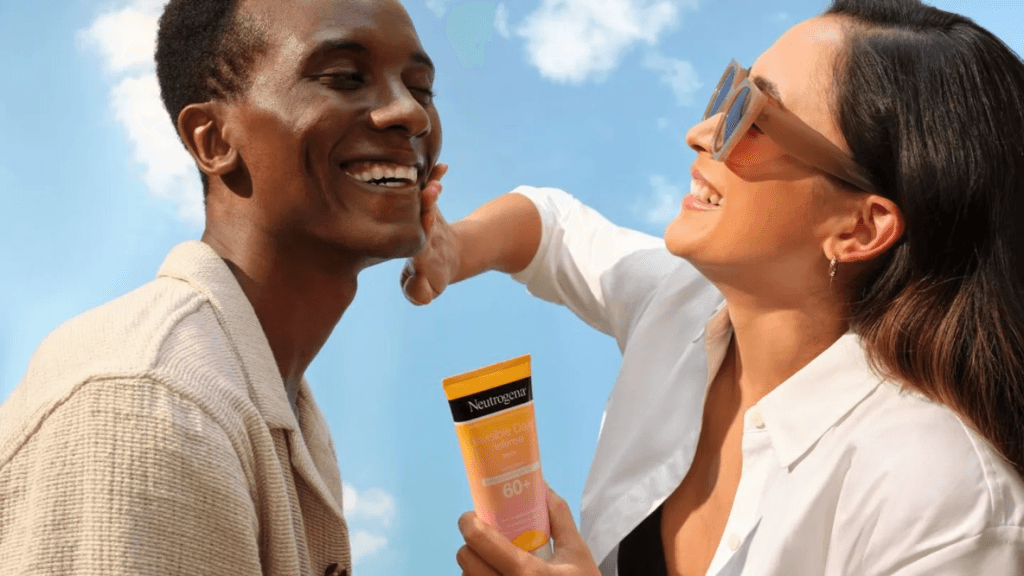
1. The Basics of Sunscreen Formulation
The foundation of any sunscreen is its ability to block or absorb ultraviolet (UV) radiation. The two primary types of sunscreen ingredients are chemical filters and physical (mineral) filters:
- Chemical Filters: These ingredients absorb UV radiation and transform it into heat, which is then released from the skin. Common chemical filters include avobenzone, octinoxate, and homosalate.
- Physical Filters: Also known as mineral sunscreens, these create a physical barrier that reflects UV rays. Zinc oxide and titanium dioxide are the most common mineral filters.
The choice of active ingredients depends on factors like skin sensitivity, desired SPF (Sun Protection Factor), and the desired texture of the final product.
2. The Manufacturing Process
Sunscreen manufacturing is a precise and scientific process that ensures the stability, efficacy, and safety of the product. Here’s an overview of the typical steps involved:
Step 1: Preparing the Base Formula
Sunscreen starts with a base that includes water, oils, and emulsifiers. The base helps bind the active ingredients and gives the product its desired texture. The water phase and oil phase are typically mixed separately before they are combined using an emulsifier that stabilizes the formula.
Step 2: Incorporating Active Ingredients
Once the base is ready, the active sunscreen ingredients (either chemical or physical) are added to the formula. The concentration of these ingredients determines the SPF level of the sunscreen. The formulation is carefully mixed to ensure the even distribution of these active ingredients.
Step 3: Homogenizing and Heating
The mixture is then homogenized (blended to a smooth consistency) and heated to ensure proper incorporation of the ingredients. This step ensures that the formula remains stable and that the active ingredients are evenly distributed throughout the sunscreen.
Step 4: Cooling and Stabilization
After heating, the sunscreen mixture is cooled. This helps maintain the integrity of the active ingredients, preventing any breakdown from excessive heat. During this cooling phase, stabilizers may be added to ensure the product does not separate over time.
Step 5: Testing and Quality Control
Before the sunscreen can be packaged, it undergoes rigorous testing. This includes checking for stability, efficacy (ensuring the sunscreen works as intended), and safety (ensuring it won’t irritate the skin). These tests are vital for ensuring the sunscreen’s performance matches its claims (e.g., SPF rating, broad-spectrum protection).
Step 6: Packaging
Once the sunscreen passes all quality control tests, it is ready to be packaged. The packaging is carefully designed to protect the formula from contaminants and preserve its shelf life. Sunscreens are often packaged in tubes, bottles, or pump dispensers to make them easy to apply.
Manufacturing Equipment in Detail
The quality of sunscreen depends significantly on the manufacturing equipment used:
High-Shear Mixers
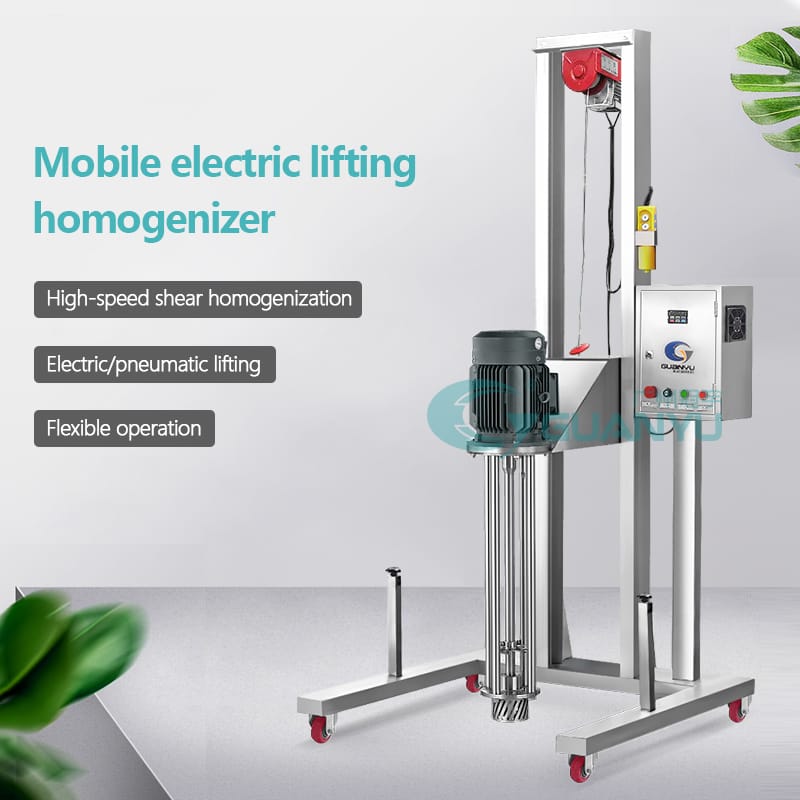
High-shear mixers are pivotal in the sunscreen manufacturing process. They are designed to effectively blend, emulsify, and disperse the various ingredients used in sunscreen formulations.
These mixers work by applying intense shear forces, crucial for breaking down particle agglomerates, ensuring even distribution of UV filters, and achieving a smooth texture.
Their ability to mix ingredients thoroughly ensures that the active ingredients are evenly distributed throughout the product, which is essential for consistent sun protection.
Vacuum Emulsifiers
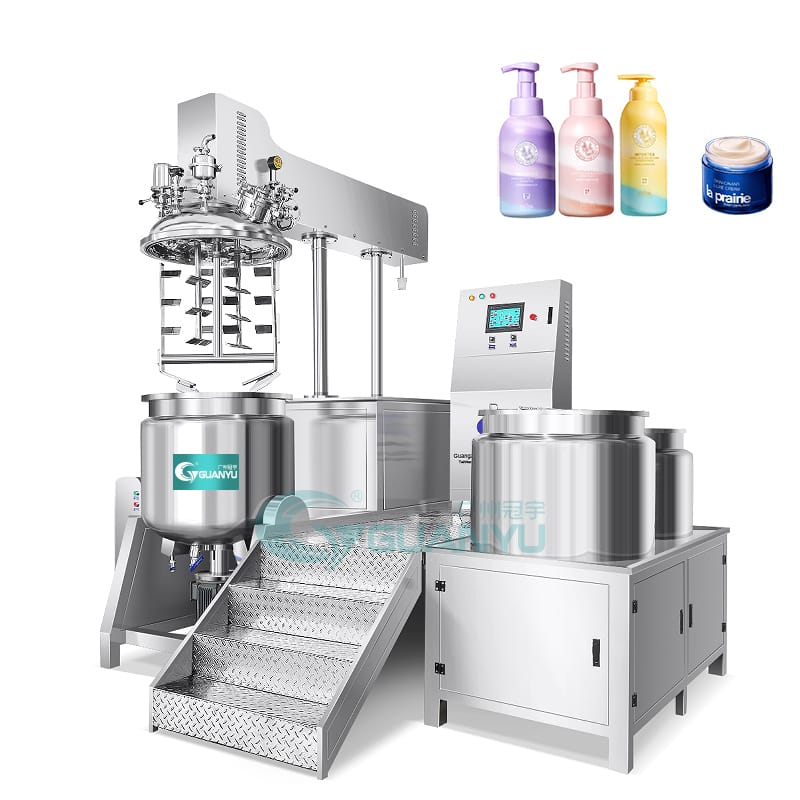
Vacuum emulsifiers play a crucial role in creating stable and uniform emulsions, which are the foundation of most sunscreen lotions and creams.
These machines work under vacuum conditions to prevent air incorporation, which is vital for achieving a stable emulsion and ensuring product longevity.
The vacuum environment also helps in reducing oxidative degradation of sensitive ingredients, such as certain organic UV filters and antioxidants, thus maintaining the efficacy and safety of the sunscreen product.
Filling Machines

Filling machines in sunscreen production are designed for precision and efficiency. They ensure that each container of sunscreen, whether it’s a bottle, tube, or spray, is filled with the exact amount of product.
This accuracy is critical not only for consumer satisfaction but also for regulatory compliance, as the labeled quantity must match the actual content. Modern filling machines are equipped with advanced technologies that can handle different viscosities and types of sunscreen formulations, ensuring consistent product quality.
Sealing and Labeling Equipment
Sealing and labeling equipment are the final steps in the sunscreen manufacturing process, and they are as important as the initial stages.
Sealing machines ensure that the packaging is securely closed to maintain the product’s integrity and prevent contamination. Proper sealing is crucial for preserving the product’s efficacy and shelf life.
Following sealing, labeling equipment is used to apply labels that provide essential information, including SPF rating, ingredients, usage instructions, and regulatory compliance details. This information is vital for consumers to make informed choices and use the product safely and effectively.
Quality Control and Testing Equipment
Quality control and testing equipment are integral to the sunscreen manufacturing process. These machines and instruments are used to test the final product for various parameters, such as SPF rating, broad-spectrum coverage, viscosity, and stability.
Quality control ensures that the sunscreen meets the required safety and efficacy standards set by regulatory bodies.
This equipment helps manufacturers maintain consistent product quality and consumer trust, which are critical in the competitive skincare market.
3. Innovations in Sunscreen Manufacturing
With ongoing advancements in skincare and cosmetic formulations, sunscreen manufacturing has seen numerous innovations. Some of the most exciting trends include:
- Water-Resistant Formulas: Modern sunscreens are often formulated to stay effective even after swimming or sweating. These products are created with enhanced water resistance, ensuring better protection during outdoor activities.
- Non-Greasy, Lightweight Textures: Many sunscreens are now available in lighter, non-greasy formulations, making them more comfortable for everyday wear. These formulas are often designed for easy absorption without leaving a white cast, especially important for those using mineral sunscreens.
- Environmental and Reef-Safe Ingredients: With growing concern about the impact of sunscreens on marine life, many manufacturers are shifting to “reef-safe” formulations that avoid harmful chemicals like oxybenzone and octinoxate.
- Broad-Spectrum Protection: Manufacturers are increasingly focusing on providing both UVB and UVA protection, which is crucial for preventing skin damage and premature aging.
4. Why Choosing the Right Sunscreen Matters
Choosing the right sunscreen is critical for effective sun protection. Here are some key factors to consider when selecting a sunscreen:
- SPF Rating: The SPF indicates the level of protection against UVB rays. A higher SPF offers more protection.
- Skin Type: People with sensitive skin should opt for mineral sunscreens, which are less likely to irritate, while those with oily skin may prefer gel-based sunscreens.
- Water Resistance: For outdoor activities, it’s important to choose a sunscreen labeled as water-resistant, which ensures protection even if you sweat or swim.
- Broad-Spectrum Protection: Make sure your sunscreen offers broad-spectrum protection to shield against both UVA and UVB rays.
Conclusion
Sunscreen is a critical part of our skincare routine, and its production involves careful formulation, testing, and quality control to ensure maximum protection. As the skincare industry continues to innovate, sunscreens are becoming more advanced, offering better texture, higher performance, and safer options for both our skin and the environment. By understanding the ingredients and manufacturing process, consumers can make more informed choices for their sun protection needs.
Enhance your industrial operations with BWER weighbridges, designed for exceptional accuracy and durability to support Iraq’s growing infrastructure and logistics sectors.
Thank you for your sharing. I am worried that I lack creative ideas. It is your article that makes me full of hope. Thank you. But, I have a question, can you help me?
I don’t think the title of your article matches the content lol. Just kidding, mainly because I had some doubts after reading the article.
Your point of view caught my eye and was very interesting. Thanks. I have a question for you.
Can you be more specific about the content of your article? After reading it, I still have some doubts. Hope you can help me.
Thanks for sharing. I read many of your blog posts, cool, your blog is very good.
Thanks for sharing. I read many of your blog posts, cool, your blog is very good.
Your point of view caught my eye and was very interesting. Thanks. I have a question for you.
Thanks for sharing. I read many of your blog posts, cool, your blog is very good.
Your point of view caught my eye and was very interesting. Thanks. I have a question for you.
Your point of view caught my eye and was very interesting. Thanks. I have a question for you.
Can you be more specific about the content of your article? After reading it, I still have some doubts. Hope you can help me.
I don’t think the title of your article matches the content lol. Just kidding, mainly because I had some doubts after reading the article.
Your point of view caught my eye and was very interesting. Thanks. I have a question for you.
Thanks for sharing. I read many of your blog posts, cool, your blog is very good.
Thanks for sharing. I read many of your blog posts, cool, your blog is very good.
Can you be more specific about the content of your article? After reading it, I still have some doubts. Hope you can help me.
Thanks for sharing. I read many of your blog posts, cool, your blog is very good.
Thanks for sharing. I read many of your blog posts, cool, your blog is very good.
Can you be more specific about the content of your article? After reading it, I still have some doubts. Hope you can help me. https://accounts.binance.com/register?ref=P9L9FQKY
Can you be more specific about the content of your article? After reading it, I still have some doubts. Hope you can help me.
Thanks for sharing. I read many of your blog posts, cool, your blog is very good.
Thanks for sharing. I read many of your blog posts, cool, your blog is very good.
Thank you for your sharing. I am worried that I lack creative ideas. It is your article that makes me full of hope. Thank you. But, I have a question, can you help me?
Thank you, your article surprised me, there is such an excellent point of view. Thank you for sharing, I learned a lot.
Thank you for your sharing. I am worried that I lack creative ideas. It is your article that makes me full of hope. Thank you. But, I have a question, can you help me?
Thank you for your sharing. I am worried that I lack creative ideas. It is your article that makes me full of hope. Thank you. But, I have a question, can you help me?
Can you be more specific about the content of your article? After reading it, I still have some doubts. Hope you can help me.
Thanks for sharing. I read many of your blog posts, cool, your blog is very good.
Your article helped me a lot, is there any more related content? Thanks!
Your article helped me a lot, is there any more related content? Thanks!
I don’t think the title of your article matches the content lol. Just kidding, mainly because I had some doubts after reading the article.
Your point of view caught my eye and was very interesting. Thanks. I have a question for you.
Your point of view caught my eye and was very interesting. Thanks. I have a question for you.
Thank you for your sharing. I am worried that I lack creative ideas. It is your article that makes me full of hope. Thank you. But, I have a question, can you help me?
Your article helped me a lot, is there any more related content? Thanks!
I don’t think the title of your article matches the content lol. Just kidding, mainly because I had some doubts after reading the article.
Your point of view caught my eye and was very interesting. Thanks. I have a question for you. https://www.binance.info/en-IN/register-person?ref=UM6SMJM3
Can you be more specific about the content of your article? After reading it, I still have some doubts. Hope you can help me.
Thank you for your sharing. I am worried that I lack creative ideas. It is your article that makes me full of hope. Thank you. But, I have a question, can you help me? https://www.binance.com/sl/register?ref=OMM3XK51