L'industrie cosmétique est un secteur en pleine croissance, continually evolving to meet consumer demands for innovative and high-quality products. One of the critical elements in the production of these products is the mixing blending tank. These tanks play a pivotal role in ensuring the consistency, stability, and quality of cosmetic products. This article explores the application of mixing blending tanks in the cosmetics industry, highlighting their importance, functionality, and impact on product development.
The Importance of Mixing Blending Pots
Mixing blending tanks are essential in the cosmetics industry due to the nature of the products being manufactured. Produits de beauté, including creams, lotions, shampoos, and makeup, require precise mixing of various ingredients to achieve the desired texture, stability, and efficacy. Inadequate mixing can lead to products that separate, have inconsistent textures, or fail to deliver the promised benefits. Donc, the use of mixing blending tanks ensures that each batch of product is homogeneous and meets the industry standards for quality and performance.
Types of Mixing Blending Pots
There are various types of mixing blending tanks used in the cosmetics industry, each designed to handle specific processes and product types. Some common types include:
- Stainless Steel Tanks: These are widely used due to their durability, resistance to corrosion, and ability to maintain product purity. Stainless steel tanks are ideal for mixing creams, lotions, et sérums.
- Vacuum Mixing Tanks: These tanks are used for products that require deaeration to prevent air bubbles, which can affect the product’s texture and stability. Vacuum mixing tanks are often used for thick creams and emulsions.
- Homogenizing Tanks: Equipped with high-shear mixers, these tanks are used to create fine, stable emulsions. They are essential for products like foundations and sunscreens where uniform particle size is crucial.
- Jacketed Tanks: These tanks have a double wall for temperature control, essential for processes requiring heating or cooling. They are used in the production of temperature-sensitive products like lipsticks and balms.
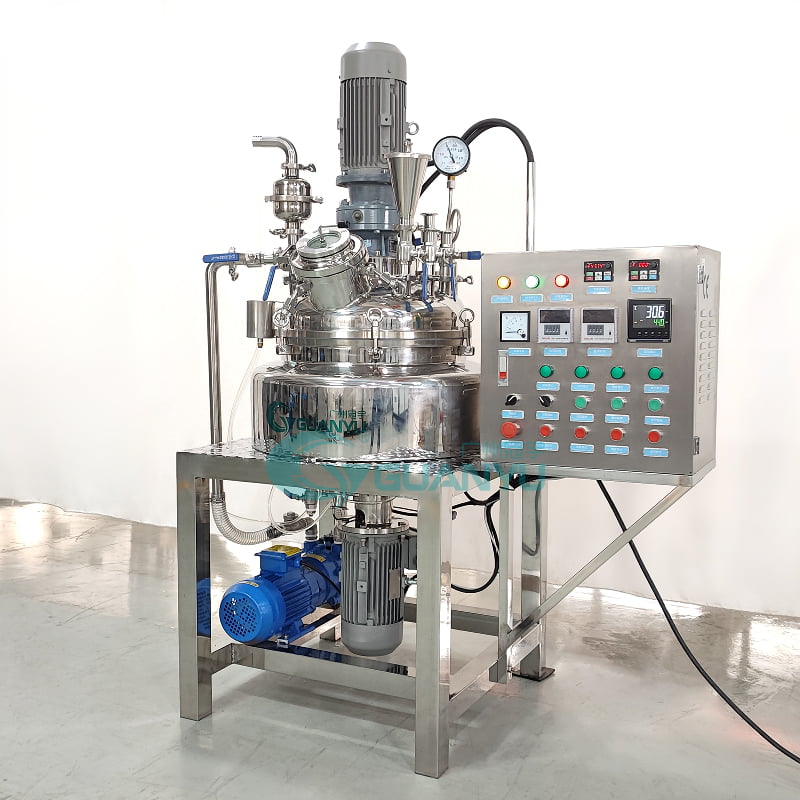
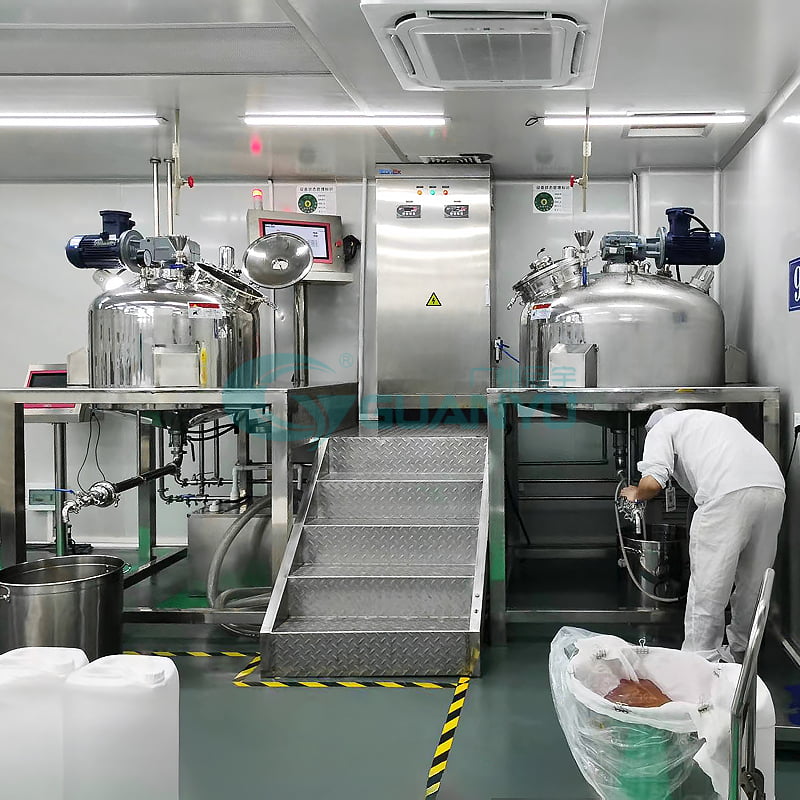
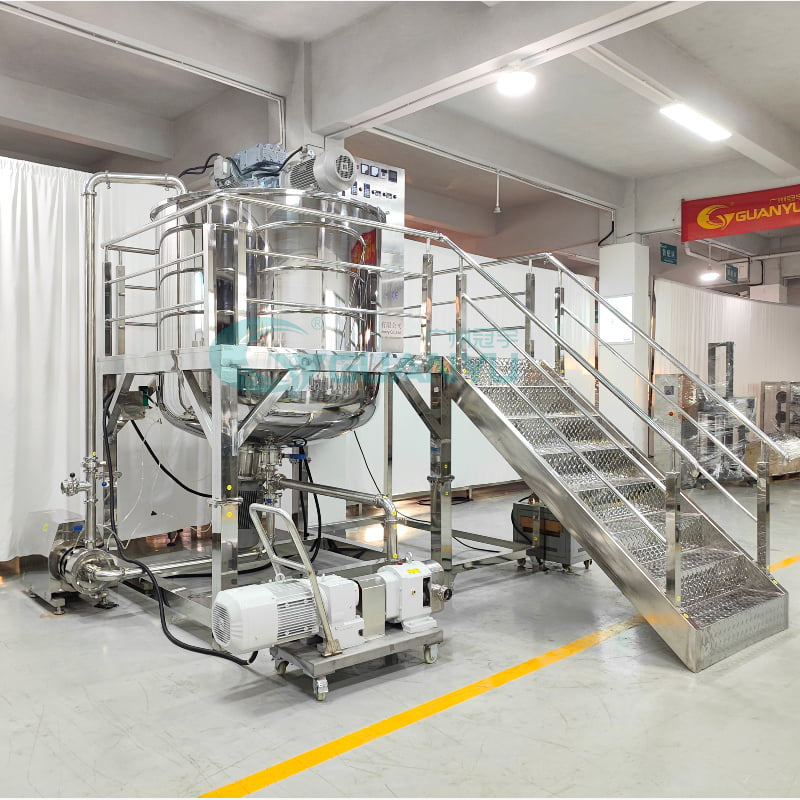
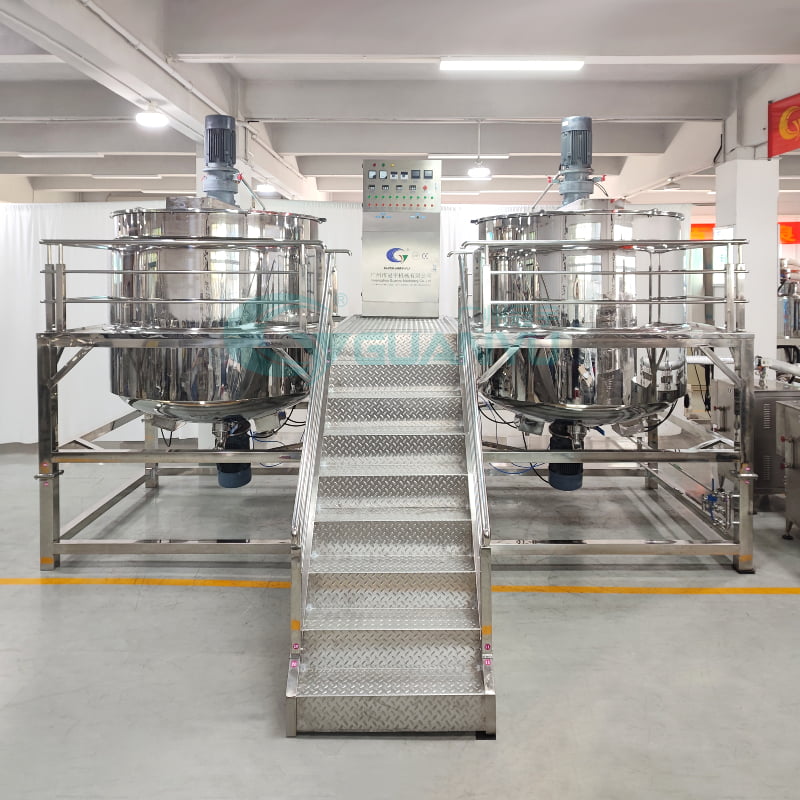
The Mixing Process in Cosmetic Production
The mixing process in cosmetic production involves several stages, each requiring precise control to achieve the desired outcome. The primary stages include:
- Ingredient Dispersion: The initial step involves dispersing powders, pigments, and other solid ingredients into liquids. This is typically done at low speeds to prevent dust formation and ensure uniform wetting of the powders.
- Emulsification: For products like lotions and creams, emulsification is crucial. This process involves mixing oil and water phases with the aid of emulsifiers to form a stable emulsion. High-shear mixers or homogenizers are often used in this stage to achieve the desired consistency and stability.
- Heating and Cooling: Some cosmetic products require heating to dissolve certain ingredients or to facilitate chemical reactions. Jacketed mixing tanks allow for precise temperature control during these processes. After mixing, rapid cooling may be necessary to stabilize the product.
- Deaeration: To remove trapped air and prevent foaming, vacuum mixing tanks are used. This step is essential for products that need to be smooth and free from air bubbles, such as gels and thick creams.
- Final Mixing: The last stage involves blending all ingredients thoroughly to ensure homogeneity. This step is crucial for maintaining product consistency across different batches.
Benefits of Using Mixing Blending Tanks
The use of mixing blending tanks in the cosmetics industry offers several benefits, contributing to the overall efficiency and quality of production. Some key benefits include:
- Consistent Quality: Mixing blending tanks ensure that each batch of product is mixed uniformly, resulting in consistent quality and performance. This is crucial for maintaining brand reputation and customer satisfaction.
- Efficacité améliorée: These tanks are designed for large-scale production, allowing manufacturers to produce large quantities of product in a shorter time. This enhances overall production efficiency and reduces costs.
- Improved Safety and Hygiene: Stainless steel mixing tanks are easy to clean and sanitize, reducing the risk of contamination. This is particularly important in the cosmetics industry, where product safety is paramount.
- Flexibility: Mixing blending tanks can be customized to handle different product types and production processes. This flexibility allows manufacturers to produce a wide range of cosmetic products using the same equipment.
- Scalability: As demand for cosmetic products grows, manufacturers can scale up production by investing in larger or additional mixing blending tanks. This scalability ensures that they can meet market demands without compromising on quality.
Innovations in Mixing Blending Tank Technology
Advancements in technology have led to significant innovations in mixing blending tank design and functionality. Some notable innovations include:
- Automated Systems: Modern mixing blending tanks are equipped with automated systems for precise control of mixing parameters, including speed, température, and mixing time. This automation reduces human error and ensures consistent product quality.
- In-line Mixing: In-line mixing technology allows for continuous mixing of ingredients as they flow through the system. This innovation enhances production efficiency and is particularly useful for large-scale manufacturing.
- Advanced Homogenizers: Newer homogenizers provide higher shear rates and better control over particle size distribution, resulting in finer and more stable emulsions. This is essential for high-performance cosmetic products.
- Energy Efficiency: Innovations in mixing tank design have also focused on reducing energy consumption. Energy-efficient motors and optimized mixing patterns help lower production costs and reduce the environmental impact of manufacturing processes.
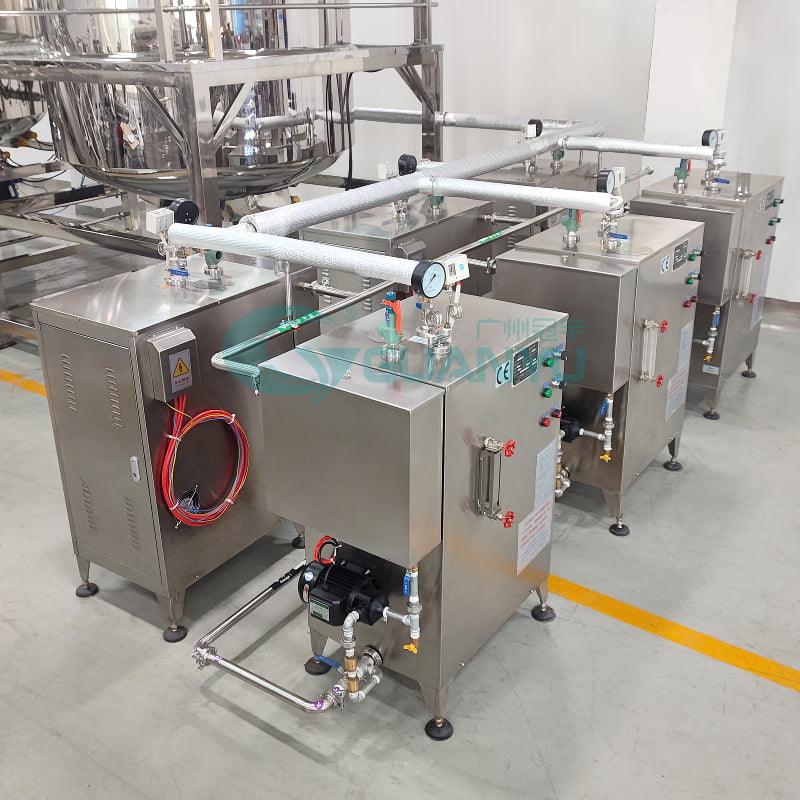
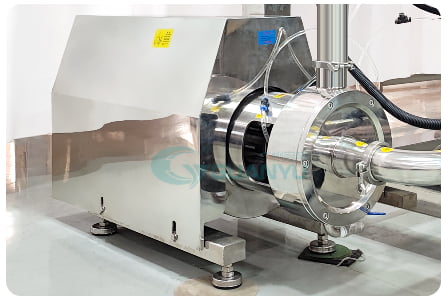
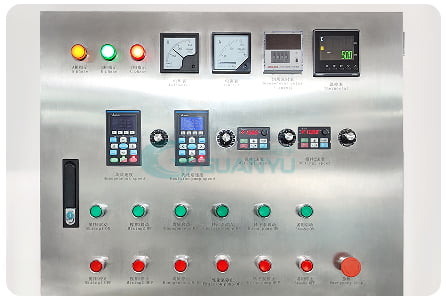
Conclusion
Mixing blending tanks are indispensable in the cosmetics industry, playing a crucial role in the production of high-quality products. Their ability to ensure consistent mixing, enhance production efficiency, and maintain product safety and hygiene makes them a vital component of cosmetic manufacturing. As technology continues to advance, the capabilities of mixing blending tanks will further improve, enabling manufacturers to meet the ever-evolving demands of the cosmetics market. By investing in state-of-the-art mixing blending tanks, cosmetic companies can maintain their competitive edge and continue to deliver innovative and high-quality products to consumers.