Dans l'industrie du parfum, the process of filling bottles with precise amounts of fragrance is a crucial step that directly impacts product quality and brand reputation. Perfume filling machines, integral to modern fragrance production, are designed to automate and optimize this process, ensuring accuracy, efficacité, and consistency. This article explores the role of perfume filling machines, highlighting their key features, types, benefits, and the latest trends in this essential aspect of fragrance manufacturing.
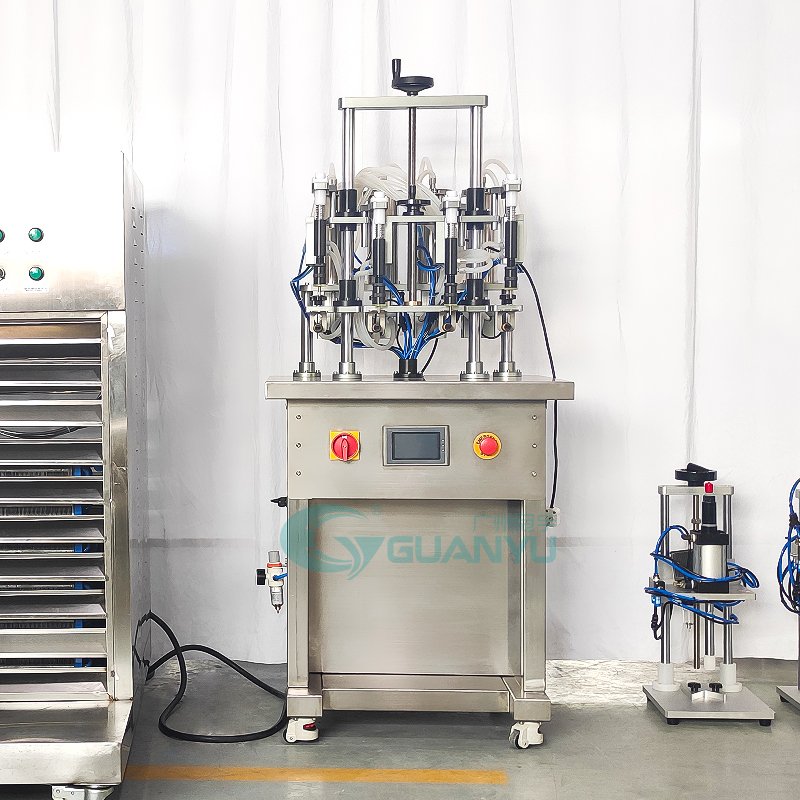
The Importance of Precision in Perfume Filling
Perfume is a luxury product where quality and presentation are paramount. Each bottle must contain an exact volume of fragrance to meet both regulatory standards and consumer expectations. Any deviation in the filling process can lead to inconsistencies in product offerings, potentially harming the brand’s reputation. Perfume filling machines address these challenges by providing a reliable and efficient means of accurately filling bottles with the desired amount of fragrance.
Core Features of Perfume Filling Machines
Perfume filling machines are designed with advanced features that cater to the specific needs of fragrance production. Key features include:
- High-Precision Filling Mechanism: At the heart of every perfume filling machine is a high-precision filling system. This mechanism ensures that each bottle is filled with the exact amount of perfume, with minimal deviation, thereby maintaining consistency across production batches.
- Versatile Conveyor Systems: These machines are equipped with conveyor systems that can be adjusted to accommodate various bottle sizes and shapes. This flexibility allows manufacturers to produce a diverse range of products without needing to invest in multiple machines.
- Automatic Bottle Positioning: To achieve accurate filling, bottles must be perfectly positioned under the filling heads. Advanced perfume filling machines use automated positioning systems to ensure each bottle is correctly aligned, reducing the risk of spillage and waste.
- User-Friendly Control Interfaces: Modern perfume filling machines are controlled via intuitive interfaces, often featuring touchscreen panels. These interfaces allow operators to easily adjust fill volumes, vitesse, and other parameters, making the machines highly adaptable to different production needs.
- Anti-Drip Technology: To maintain cleanliness and prevent wastage, many perfume filling machines incorporate anti-drip nozzles. This technology ensures that the filling process is not only efficient but also mess-free, which is particularly important when dealing with high-value liquids like perfume.
Types of Perfume Filling Machines
Perfume filling machines vary in complexity and capacity, making them suitable for different scales of production:
- Manual Filling Machines: These are basic machines ideal for small-scale or artisanal perfume producers. They require manual operation, making them suitable for lower production volumes where the emphasis is on craftsmanship rather than speed.
- Semi-Automatic Filling Machines: These machines offer a balance between manual and automated operations. They require some operator involvement but significantly increase production efficiency compared to fully manual systems. Semi-automatic machines are often used by mid-sized manufacturers looking to scale their operations without fully committing to automation.
- Fully Automatic Filling Machines: Designed for large-scale production, fully automatic machines handle the entire filling process with minimal human intervention. These machines are equipped with advanced features such as automatic bottle feeding, plafonnement, and labeling, making them ideal for high-volume production environments.
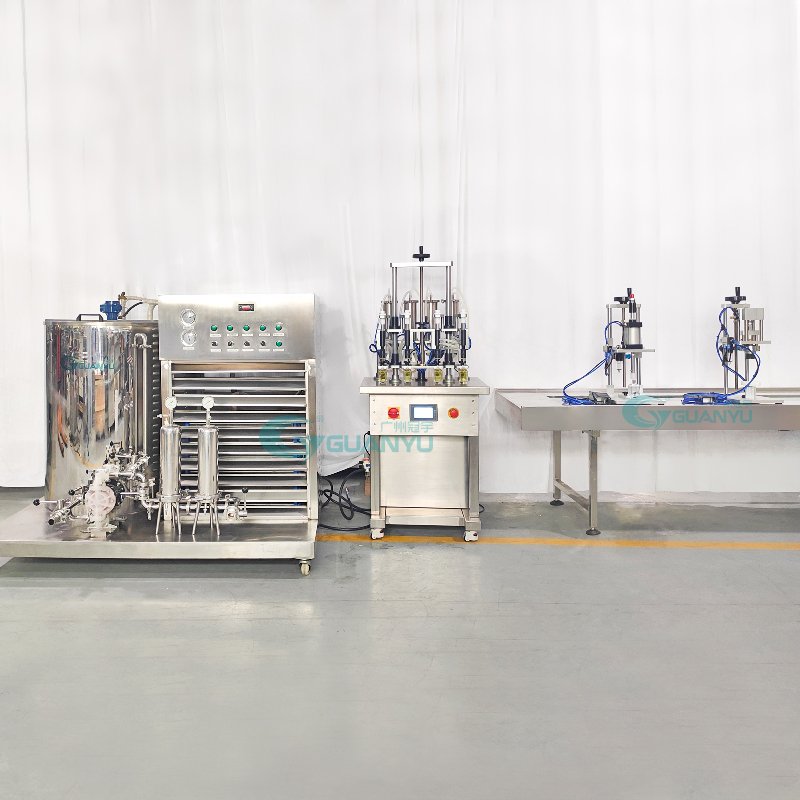
Benefits of Using Advanced Perfume Filling Machines
The adoption of advanced perfume filling machines in fragrance production offers several significant benefits:
- Enhanced Production Efficiency: Automatic filling machines can process large volumes of bottles per hour, dramatically increasing production speed. This efficiency is crucial for manufacturers looking to meet high consumer demand while maintaining quality.
- Consistency and Accuracy: Perfume filling machines are engineered to deliver precise fill volumes, ensuring consistency across all bottles. This accuracy is vital for maintaining the integrity of the product and meeting regulatory standards.
- Reduction in Wastage: By accurately controlling the amount of perfume dispensed, these machines minimize overfilling and spillage, leading to a significant reduction in product waste. This not only saves costs but also supports sustainable manufacturing practices.
- Labor Cost Savings: The automation of the filling process reduces the need for manual labor, leading to substantial savings in operational costs. This is particularly beneficial for large manufacturers where labor costs can represent a significant portion of overall expenses.
- Improved Hygiene and Safety: Perfume filling machines are designed to meet strict hygiene standards. Many machines use stainless steel and other non-reactive materials, ensuring that the perfume remains uncontaminated. Additionally, safety features such as explosion-proof designs are crucial when dealing with flammable substances commonly found in perfumes.
Innovations in Perfume Filling Technology
The fragrance industry is constantly evolving, with new technologies emerging that enhance the efficiency and functionality of perfume filling machines. One such trend is the integration of smart technologies, such as the Internet of Things (IoT), into these machines. IoT-enabled machines can be monitored in real-time, allowing for predictive maintenance and reducing downtime. This technology also enables remote control and optimization of the filling process, further enhancing production efficiency.
Another innovation is the development of multi-function machines that can handle various stages of production, from filling to capping and labeling. These integrated systems reduce the need for multiple machines and streamline the production process, making it more cost-effective and efficient.
Additionally, the trend towards customization in the fragrance market has led to the creation of more versatile filling machines. These machines are capable of handling a wide range of bottle shapes and sizes, enabling brands to offer personalized products without compromising on production speed or quality.
The Future of Perfume Filling Machines
As consumer demands continue to evolve, so too will the technology behind perfume filling machines. Future advancements are likely to focus on further enhancing automation, improving the flexibility of machines to handle diverse product lines, and integrating more sustainable practices into the manufacturing process.
For instance, the use of eco-friendly materials and energy-efficient technologies in machine design is expected to become more prevalent as brands increasingly prioritize sustainability. De plus, as digital technologies advance, we can expect to see even greater integration of AI and machine learning in perfume filling machines, enabling smarter, more adaptable production systems.
About us Guanyu Machinery Company
◭ 25 Années: Guangzhou Guanyu Machinery Co.Ltd a été engagé dans la recherche et la fabrication de machines pour médical, produits chimiques alimentaires et industriels pour 25 années.
◭ Notre propre usine: Notre usine a 7000 mètres carrés, plus que 100 ouvriers, et 6 lignes de production de machines, y compris la fabrication de machines, polissage, et tester.
◭ Machines personnalisées: Nos principaux produits comprennent des machines émulsifiantes sous vide fixes, homogénèseurs mobiles, toutes sortes de bouilloires agitatrices de réaction.
◭ Produits applicables: Ils conviennent à la fabrication de la crème, lotion, produits liquides, y compris la crème pour le visage, ondage, ketchup, Mayonnaise, Confiture, savon à main, shampooing, etc..
◭ Certifications: CE, BPF, UL et certificats technologiques brevetés.
Conclusion
Perfume filling machines are a cornerstone of modern fragrance production, offering unparalleled precision, efficacité, and consistency. As technology continues to advance, these machines will play an even more significant role in helping perfume manufacturers meet the demands of a dynamic and competitive market. For brands looking to stay ahead of the curve, investing in the latest perfume filling technology is not just an option—it’s a necessity for ensuring long-term success in the fragrance industry.