Introduction to the Types of Emulsifiers
In the realm of facial cream production, the choice of emulsifiers plays a pivotal role in determining the quality, stability, and texture of the final product. Emulsifiers are essential agents that facilitate the blending of immiscible liquids, such as oil and water, to create a homogenous and stable mixture. This section provides an overview of the main types of emulsifiers commonly employed in the cosmetic industry, specifically focusing on high shear mixers/homogenizers, emulsifying mixers, and vacuum emulsifiers. By understanding the working principles, advantages, and disadvantages of each type, readers can make informed decisions tailored to their specific production needs.
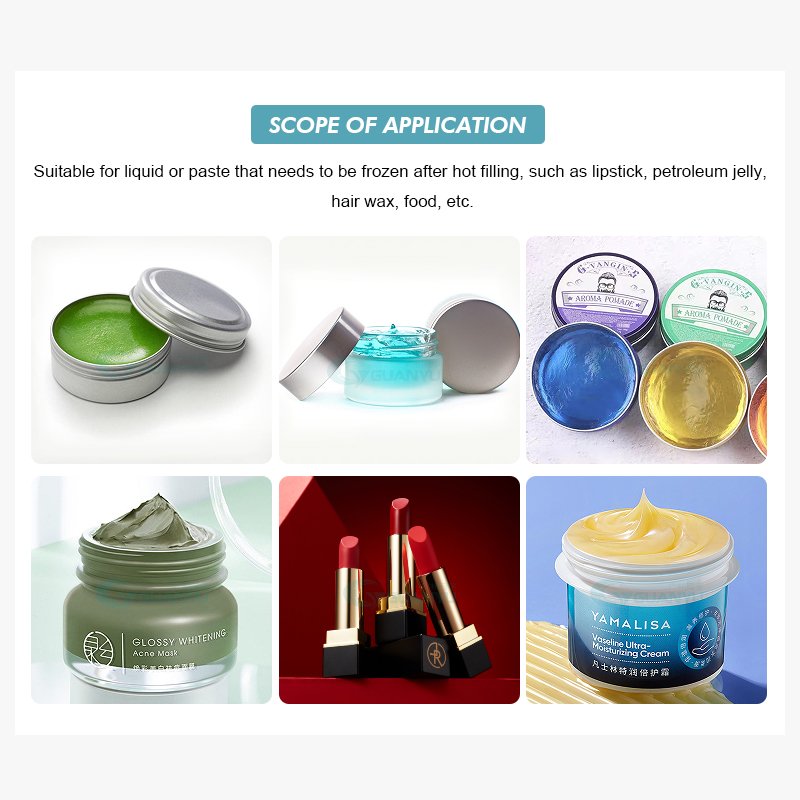
High Shear Mixers/Homogenizers
High Shear Mixers/Homogenizers: These emulsifiers operate by applying intense mechanical force to break down the droplets of oil and water into smaller sizes, resulting in a fine and uniform emulsion. High shear mixers are particularly effective in creating stable emulsions with smooth textures and are widely used for products requiring a consistent and luxurious feel. However, they can generate significant heat during operation, which may not be suitable for heat-sensitive ingredients. Additionally, the high energy consumption and maintenance costs are factors to consider when opting for this type of emulsifier.
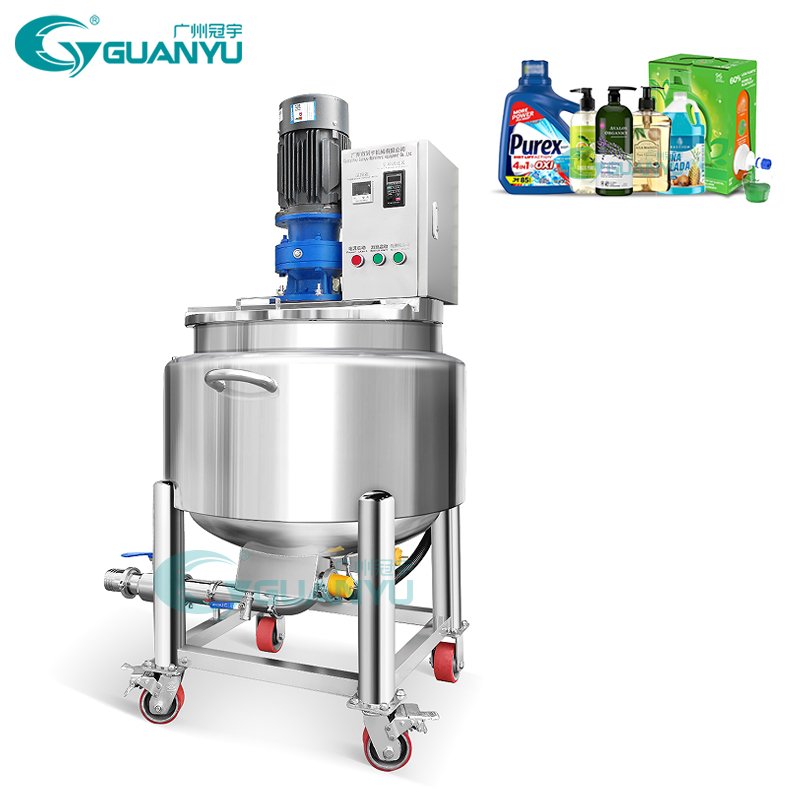
Emulsifying Mixers
Emulsifying Mixers: Emulsifying mixers utilize a combination of mechanical agitation and chemical emulsifiers to facilitate the blending process. These mixers are versatile and can handle a wide range of viscosities, making them suitable for various cosmetic formulations. The primary advantage of emulsifying mixers is their ability to produce stable emulsions with minimal energy input. However, the efficiency of these mixers can be influenced by the type and concentration of the chemical emulsifiers used, and they may not achieve the same level of fineness as high shear mixers.
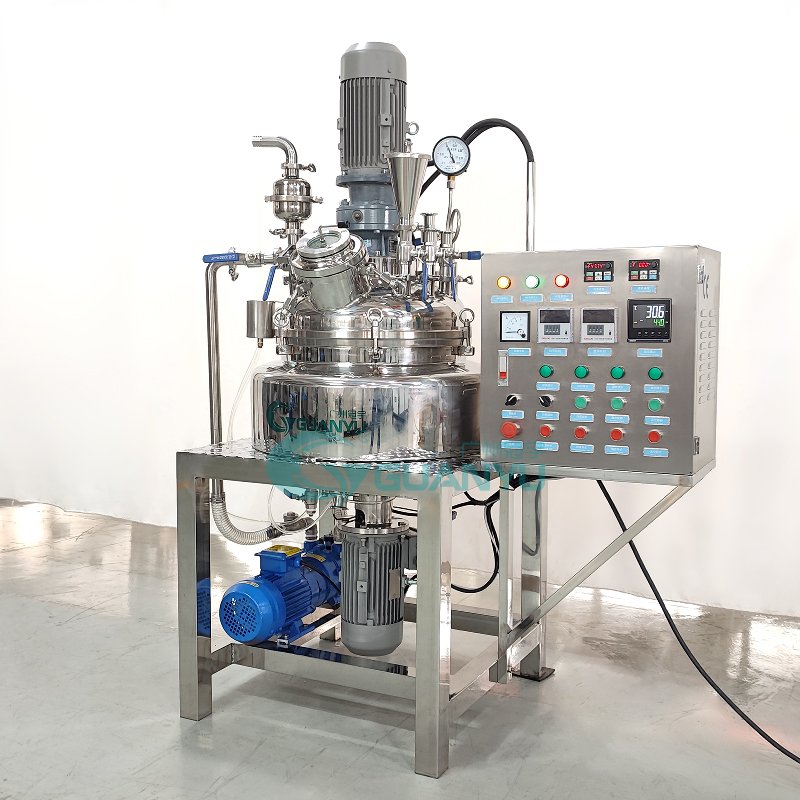
Vacuum Emulsifiers
Vacuum Emulsifiers: Vacuum emulsifiers operate under reduced pressure conditions, which helps in minimizing air incorporation and enhancing the stability of the emulsion. This type of emulsifier is ideal for producing high-quality facial creams with a smooth and air-free texture. Vacuum emulsifiers are particularly beneficial for formulations containing volatile or sensitive ingredients, as the low-pressure environment reduces the risk of oxidation and degradation. Nevertheless, the initial investment and operational complexity are higher compared to other emulsifiers, making them more suitable for large-scale production.
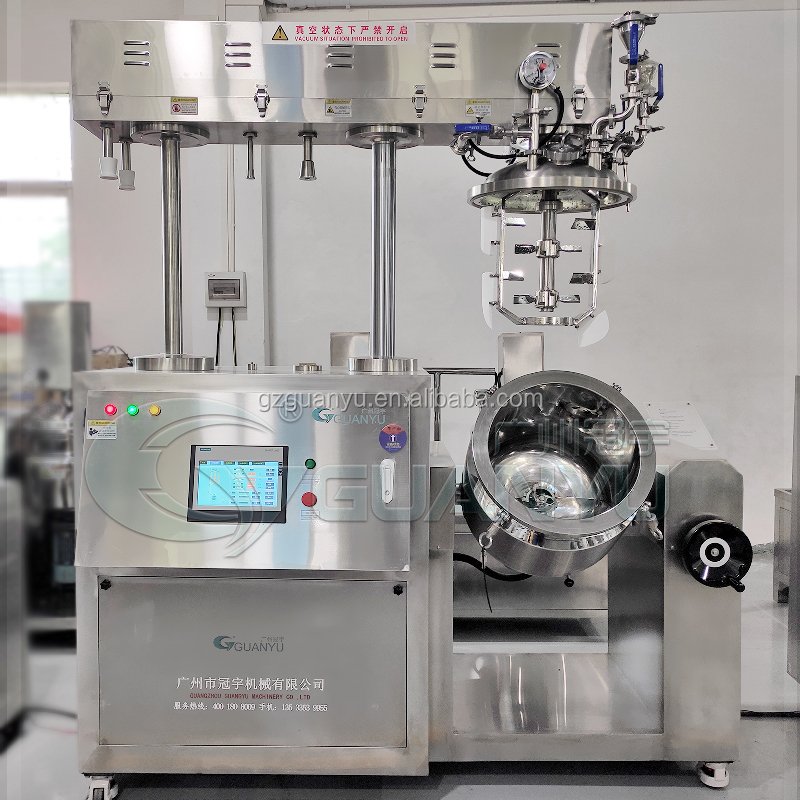
Features of Vacuum Homogenizing Emulsifier
In the production of facial creams, selecting the appropriate emulsifying equipment is critical to achieving a product that meets high-quality standards. A vacuum homogenizing emulsifier stands out due to its advanced features and benefits that significantly enhance the emulsification process.
One of the primary advantages of a vacuum homogenizing emulsifier is its ability to create a highly efficient emulsification effect. Operating in a vacuum environment, this equipment minimizes air incorporation, which is crucial for producing a smooth and consistent texture in facial creams. The absence of air bubbles during the emulsification process not only improves the product’s aesthetic appeal but also enhances its stability and shelf life. Consequently, the final product boasts a superior texture and consistency, essential qualities for high-end cosmetic products.
Another significant feature of vacuum homogenizing emulsifiers is their proficiency in maintaining consistent product quality across large batches. This consistency is achieved through precise control over various parameters such as temperature, pressure, and mixing speed, ensuring that each batch meets the same stringent quality standards. This capability is particularly beneficial for manufacturers looking to scale up production without compromising on the quality of their facial creams.
De plus, vacuum homogenizing emulsifiers offer flexibility to accommodate different production scales. Whether you are manufacturing small batches for niche markets or large-scale production for mainstream distribution, this equipment can be adjusted to meet diverse production needs. The versatility of vacuum homogenizing emulsifiers makes them an invaluable asset for both small and large cosmetic manufacturers.
Features of Vacuum Homogenizing Emulsifier
In the production of facial creams, selecting the appropriate emulsifying equipment is critical to achieving a product that meets high-quality standards. A vacuum homogenizing emulsifier stands out due to its advanced features and benefits that significantly enhance the emulsification process.
One of the primary advantages of a vacuum homogenizing emulsifier is its ability to create a highly efficient emulsification effect. Operating in a vacuum environment, this equipment minimizes air incorporation, which is crucial for producing a smooth and consistent texture in facial creams. The absence of air bubbles during the emulsification process not only improves the product’s aesthetic appeal but also enhances its stability and shelf life. Consequently, the final product boasts a superior texture and consistency, essential qualities for high-end cosmetic products.
Another significant feature of vacuum homogenizing emulsifiers is their proficiency in maintaining consistent product quality across large batches. This consistency is achieved through precise control over various parameters such as temperature, pressure, and mixing speed, ensuring that each batch meets the same stringent quality standards. This capability is particularly beneficial for manufacturers looking to scale up production without compromising on the quality of their facial creams.
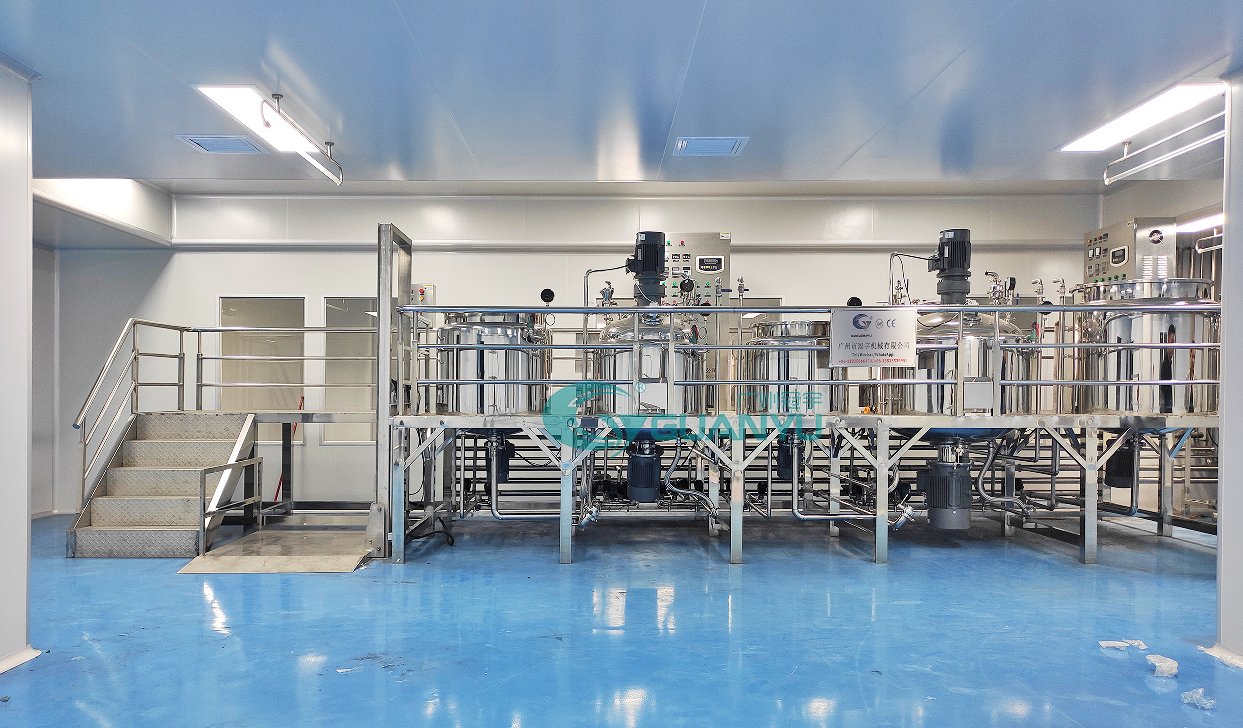
Real-world examples underscore the efficacy of vacuum homogenizing emulsifiers. For instance, a renowned skincare brand reported a 30% reduction in production time and a 20% improvement in product stability after switching to a vacuum homogenizing emulsifier. Similarly, a case study involving a mid-sized cosmetic company highlighted the equipment’s ability to produce uniform batches consistently, thereby enhancing overall customer satisfaction.
summary
the vacuum homogenizing emulsifier is a versatile and efficient tool that significantly enhances the production of high-quality facial creams. Its ability to produce a superior texture, maintain consistent quality across large batches, and adapt to various production scales makes it an essential piece of equipment in the cosmetic manufacturing industry.