Introduction
The production of hand sanitizer has become increasingly critical in maintaining public health, especially during the COVID-19 pandemic. Ensuring the high quality and consistency of hand sanitizers is essential to their effectiveness. Central to this process is the use of advanced equipment, particularly mixing kettles. This essay explores the application of mixing kettles in the production of hand sanitizer, detailing their production advantages and overall benefits.
The Role of Mixing Tanks in Hand Sanitizer Production
What is a Mixing tank?
A mixing kettle, also known as a mixing tank or reactor, is a vessel designed to blend, mix, and sometimes heat ingredients to create a homogenous mixture. In the context of hand sanitizer production, mixing kettles are used to combine alcohol, agua, glycerin, and other essential ingredients to form a uniform product.
The Mixing Process
The process typically involves several steps:
- Ingredient Addition: Precise amounts of alcohol, agua, and other ingredients are added to the mixing kettle.
- Mezclando: The ingredients are mixed thoroughly to ensure even distribution and consistency.
- Heating/Cooling: Depending on the formulation, the mixture may be heated or cooled to facilitate blending or achieve desired properties.
- Emulsification: In some formulations, an emulsification step is required to combine ingredients that do not naturally mix well.
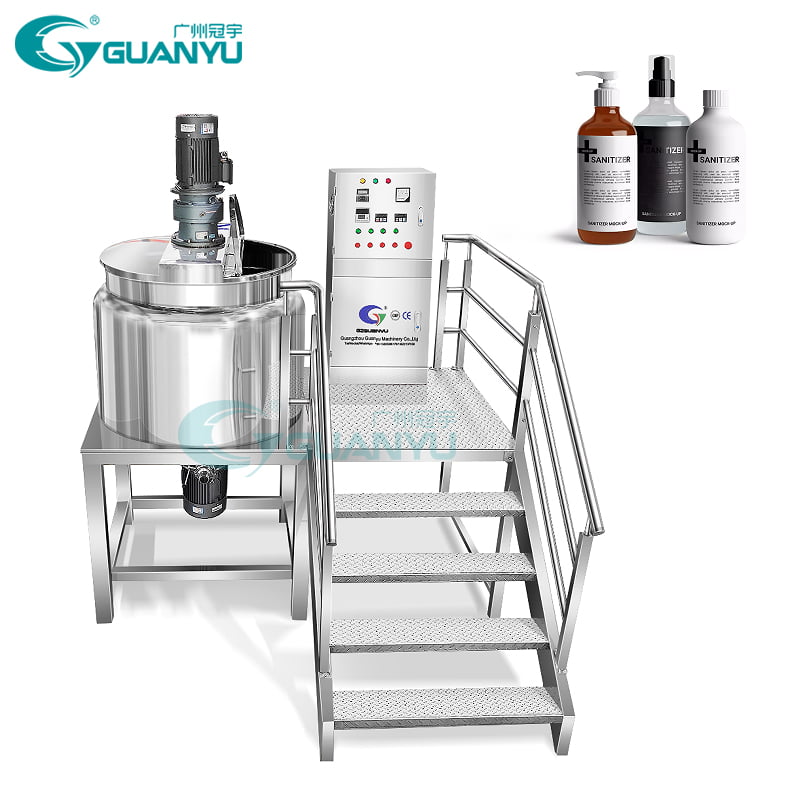
Production Advantages of Mixing Tanks in Hand Sanitizer Manufacturing
Consistent Quality and Homogeneity
One of the primary advantages of using mixing kettles in hand sanitizer production is the ability to achieve consistent quality and homogeneity. Proper mixing ensures that active ingredients, such as alcohol, are evenly distributed throughout the product. This consistency is crucial for the sanitizer’s effectiveness in killing germs and bacteria.
Efficient Production Process
Mixing kettles are designed for efficiency. They can handle large volumes of ingredients and complete the mixing process quickly. This efficiency translates to higher production rates, which is especially important during periods of high demand, such as during health crises.
Precise Control and Automation
Modern mixing kettles often come with advanced control systems that allow for precise monitoring and adjustment of mixing parameters, such as speed, temperature, and time. Automation reduces the risk of human error and ensures that each batch meets the same high standards.
Versatility and Flexibility
Mixing kettles are versatile and can be used for various formulations of hand sanitizers, whether gel-based, líquido, or foam. Their design allows for easy adjustments to accommodate different recipes, providing manufacturers with the flexibility to produce a wide range of products.
Hygienic Design
Maintaining hygiene is crucial in the production of hand sanitizers. Mixing kettles are typically made from stainless steel and other non-reactive materials that are easy to clean and sanitize. Their design often includes features that prevent contamination, such as sealed lids and sanitary fittings.
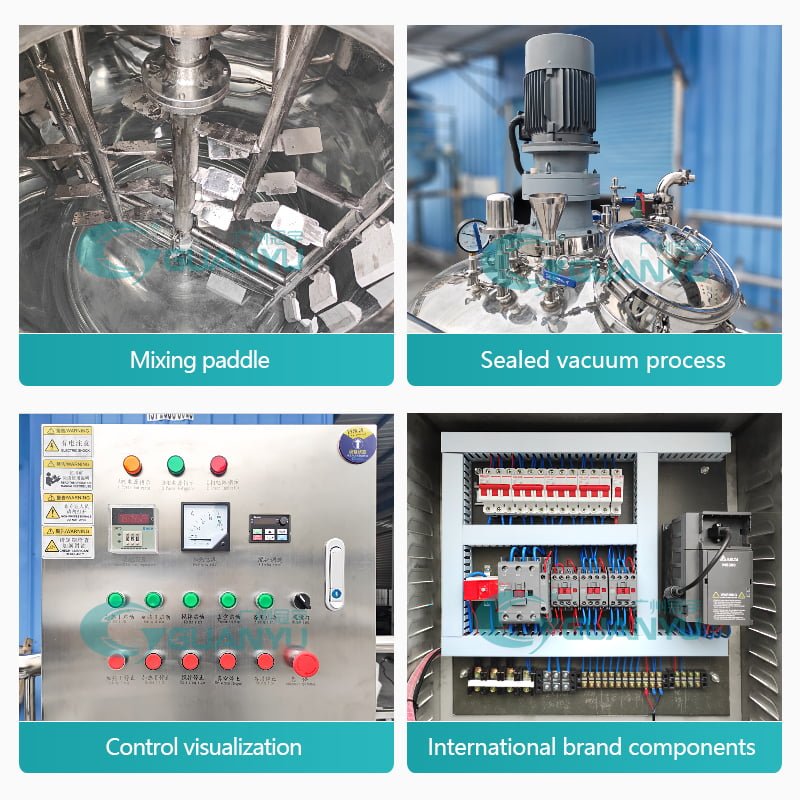
Technical Advantages of Mixing Tanks
Advanced Mixing Mechanisms
Mixing kettles are equipped with advanced mixing mechanisms, such as high-shear mixers, agitators, and impellers, which ensure thorough blending of ingredients. These mechanisms can handle various viscosities and ingredient combinations, ensuring a uniform product.
Temperature Control
Temperature control is essential in hand sanitizer production, especially when dealing with alcohol, which has a low boiling point. Mixing kettles with integrated heating and cooling systems allow precise temperature management, ensuring optimal mixing conditions and preventing the degradation of heat-sensitive ingredients.
Pressure Control
Some mixing kettles are designed to operate under specific pressure conditions, allowing for more efficient mixing and reaction control. This capability is particularly useful for certain formulations that require pressurized environments to achieve the desired properties.
Applications Beyond Hand Sanitizers
Versatility in Chemical and Pharmaceutical Industries
While this essay focuses on hand sanitizer production, mixing kettles are widely used in various industries, including pharmaceuticals, productos cosméticos, and food processing. Their ability to mix, heat, Frío, and emulsify makes them indispensable in producing creams, lotions, syrups, and other liquid or semi-liquid products.
Customization and Innovation
Mixing kettles can be customized to meet specific production needs. Por ejemplo, manufacturers can choose different mixing mechanisms, capacities, and control systems to suit their particular formulations. This customization supports innovation, allowing companies to develop new products and improve existing ones.
Case Study: Mixing pots in a Hand Sanitizer Production Facility
To illustrate the advantages of mixing kettles, consider a case study of a hand sanitizer production facility that transitioned from manual mixing methods to using modern mixing kettles.
Initial Challenges
The facility initially faced challenges with inconsistent product quality, high labor costs, and low production capacity. Manual mixing methods were time-consuming and prone to errors, leading to variability in the final product.
Implementation of Mixing Kettles
The decision to invest in mixing kettles was driven by the need to improve efficiency and product consistency. The new mixing kettles were integrated into the production line, replacing manual mixing methods.
Outcomes and Benefits
- Consistency and Quality: The mixing kettles provided uniform mixing, resulting in consistent product quality. Each batch of hand sanitizer met the same high standards for effectiveness and appearance.
- Increased Production Capacity: The efficiency of the mixing kettles allowed the facility to significantly increase its production capacity, meeting growing market demands without compromising quality.
- Reduced Labor Costs: Automation of the mixing process reduced the need for manual labor, lowering overall production costs and minimizing the risk of human error.
- Enhanced Hygiene: The hygienic design of the mixing kettles ensured that the production process met stringent sanitary standards, reducing the risk of contamination and improving product safety.
- Cost Savings: Despite the initial investment, the facility experienced cost savings through reduced labor costs, lower waste, and improved operational efficiency.
Conclusión
The application of mixing tanks in hand sanitizer production offers numerous advantages, from ensuring consistent quality and homogeneity to enhancing efficiency and reducing costs. These machines provide precise control over the mixing process, accommodating various formulations and supporting innovation. Beyond hand sanitizers, mixing kettles have versatile applications in the chemical, farmacéutico, e industrias alimentarias, making them a valuable investment for manufacturers. As demonstrated in the case study, transitioning to mixing kettles can lead to significant improvements in production outcomes, driving both customer satisfaction and business success.