Introduction
In the realm of daily chemical products, including shampoos, detergents, lotions, and other personal care items, the demand for efficiency, accuracy, and quality in production is paramount. As the market expands and consumer expectations rise, manufacturers are continuously seeking ways to optimize their production processes. One significant innovation in this context is the semi-automatic filling machine. These machines bridge the gap between manual and fully automated systems, offering a balanced solution that enhances productivity while maintaining flexibility. This article explores the features, benefits, and applications of semi-automatic filling machines in the daily chemical products industry.
Overview of Semi-Automatic Filling Machines
Semi-automatic filling machines are designed to partially automate the process of filling containers with various liquid or viscous products. Unlike manual filling, which is labor-intensive and prone to inconsistencies, semi-automatic machines offer greater precision and speed without the complexity and cost associated with fully automated systems.

Key Features
- Flexibility: Semi-automatic filling machines can handle a wide range of container sizes and types, making them suitable for diverse product lines.
- Precision: These machines are equipped with advanced sensors and control systems that ensure accurate fill volumes, reducing product waste and ensuring consistency.
- Ease of Use: User-friendly interfaces and straightforward setup processes make these machines accessible even for operators with minimal technical expertise.
- Cost-Effective: Compared to fully automated systems, semi-automatic machines offer a lower initial investment, making them ideal for small to medium-sized enterprises.
Types of Semi-Automatic Filling Machines
- Piston Fillers: Ideal for thick, viscous products such as creams, Gele, and pastes. These machines use a piston mechanism to draw the product from a hopper and dispense it into containers with high precision.
- Gravity Fillers: Suitable for free-flowing liquids like shampoos and detergents. Gravity fillers rely on the natural flow of the liquid, making them simple and effective for certain applications.
- Pump Fillers: Versatile machines that can handle a range of viscosities. Pump fillers use different types of pumps (e.g., peristaltic, gear) to transfer the product from the supply tank to the containers.
- Overflow Fillers: Commonly used for products that foam or require a uniform fill level. Overflow fillers ensure that each container is filled to the same level, regardless of minor variations in container volume.
Benefits of Semi-Automatic Filling Machines
The integration of semi-automatic filling machines into the production of daily chemical products offers numerous advantages, significantly impacting efficiency, Qualität, and operational costs.
Enhanced Efficiency
Semi-automatic filling machines streamline the filling process, allowing for higher throughput compared to manual methods. Operators can fill multiple containers in a shorter amount of time, increasing overall production capacity. This efficiency is crucial for meeting market demands and scaling operations.
Improved Accuracy and Consistency
The precision of semi-automatic filling machines ensures that each container receives the exact amount of product, minimizing variations and reducing waste. This consistency is vital for maintaining product quality and complying with regulatory standards. Accurate filling also enhances customer satisfaction, as consumers receive products with uniform quality.
Cost Savings
While fully automated systems require significant capital investment, semi-automatic machines provide a more affordable alternative without compromising on key benefits. The lower initial cost, combined with increased productivity and reduced waste, results in substantial cost savings for manufacturers. Additionally, these machines require less maintenance and have lower operational costs compared to their fully automated counterparts.
Flexibility in Production
Semi-automatic filling machines offer greater flexibility, allowing manufacturers to switch between different products and container sizes with ease. This adaptability is particularly beneficial for companies that produce a variety of daily chemical products. Quick changeover times ensure minimal downtime and enable manufacturers to respond swiftly to market trends and consumer preferences.
Ease of Integration and Operation
The user-friendly design of semi-automatic filling machines makes them easy to integrate into existing production lines. Their straightforward operation and minimal training requirements enable manufacturers to quickly deploy these machines and start reaping the benefits. The ability to easily adjust settings and parameters further enhances their usability and convenience.
Applications in Daily Chemical Products
Semi-automatic filling machines are versatile tools that find applications across a wide range of daily chemical products. Here are some specific examples of how these machines are utilized in the industry:
Personal Care Products
- Shampoos and Conditioners: Semi-automatic fillers are ideal for handling the viscosity of shampoos and conditioners, ensuring precise and consistent filling. These machines can accommodate various bottle sizes and shapes, catering to different product lines.
- Lotions and Creams: For thicker personal care products like lotions and creams, piston fillers offer the necessary precision and control. The ability to handle varying viscosities ensures smooth and efficient filling, maintaining product integrity.
- Body Wash and Liquid Soaps: Gravity fillers and pump fillers are commonly used for body wash and liquid soaps, providing accurate filling and minimizing foam formation. This ensures that each bottle is filled to the desired level without spillage or waste.
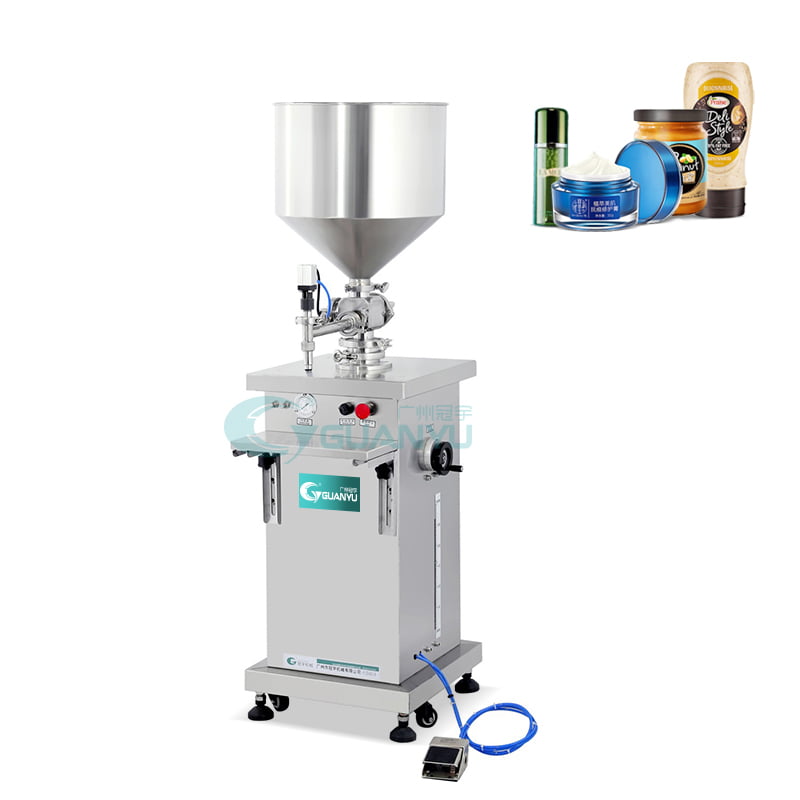
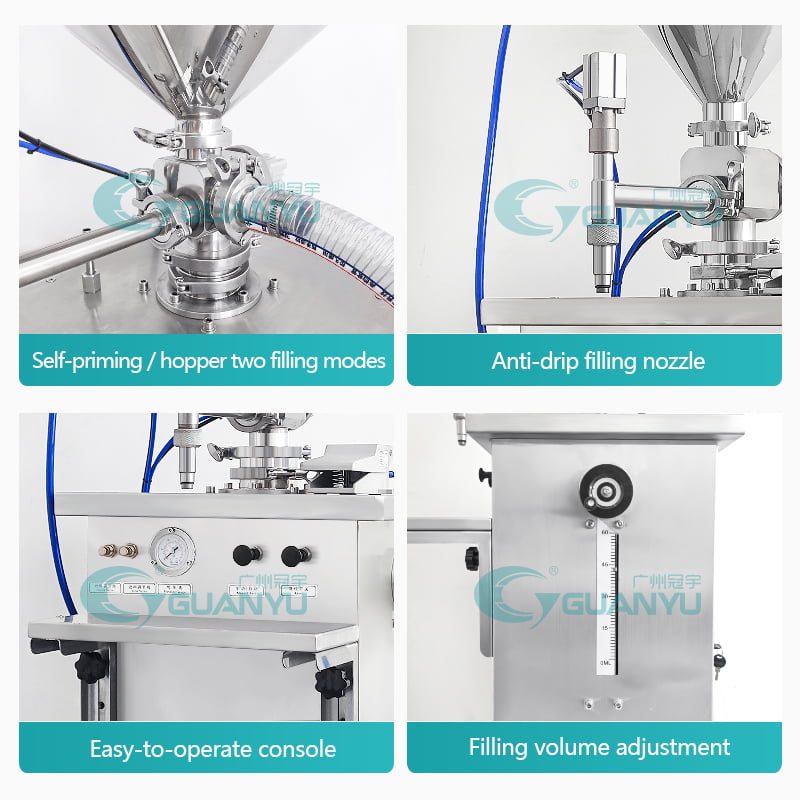
Household Cleaning Products
- Detergents: Semi-automatic filling machines are well-suited for filling liquid detergents into bottles and containers. The precise control over fill volumes ensures consistency, while the flexibility of the machines allows for easy switching between different detergent formulations.
- Disinfectants and Sanitizers: With the increased demand for disinfectants and sanitizers, semi-automatic fillers provide a reliable solution for efficient production. These machines can handle both liquid and gel-based formulations, ensuring accurate and hygienic filling.
Industrial and Specialty Chemicals
- Solvents and Cleaning Agents: Semi-automatic filling machines are used for filling solvents and industrial cleaning agents, ensuring safe and precise handling of these chemicals. The robust construction of these machines ensures durability and reliability in demanding production environments.
- Lubricants and Oils: For viscous products like lubricants and oils, piston fillers provide the necessary power and precision. These machines can handle high-viscosity fluids, ensuring consistent filling and reducing the risk of leaks or spills.
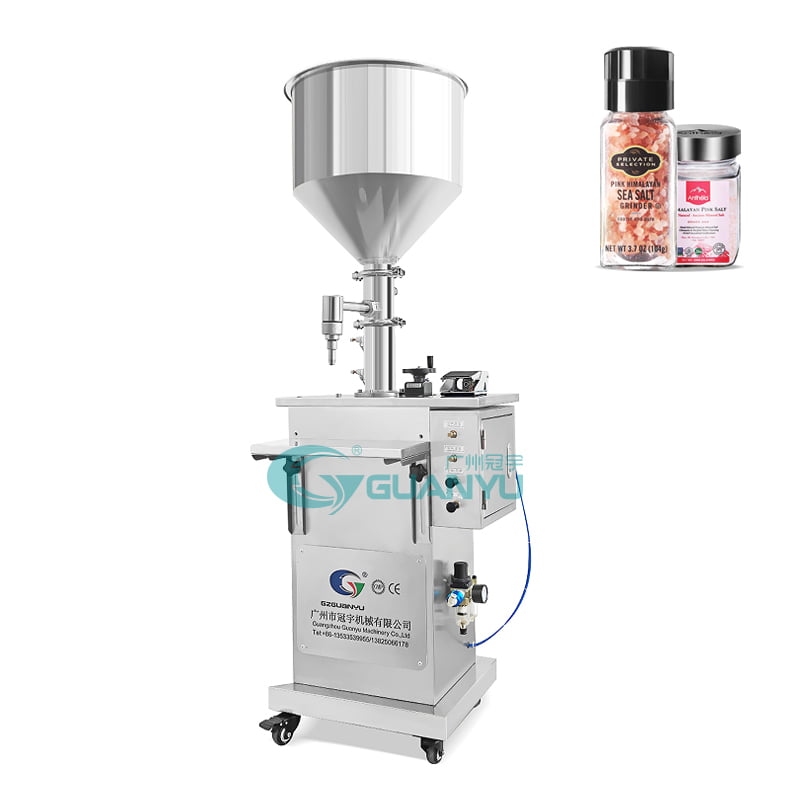
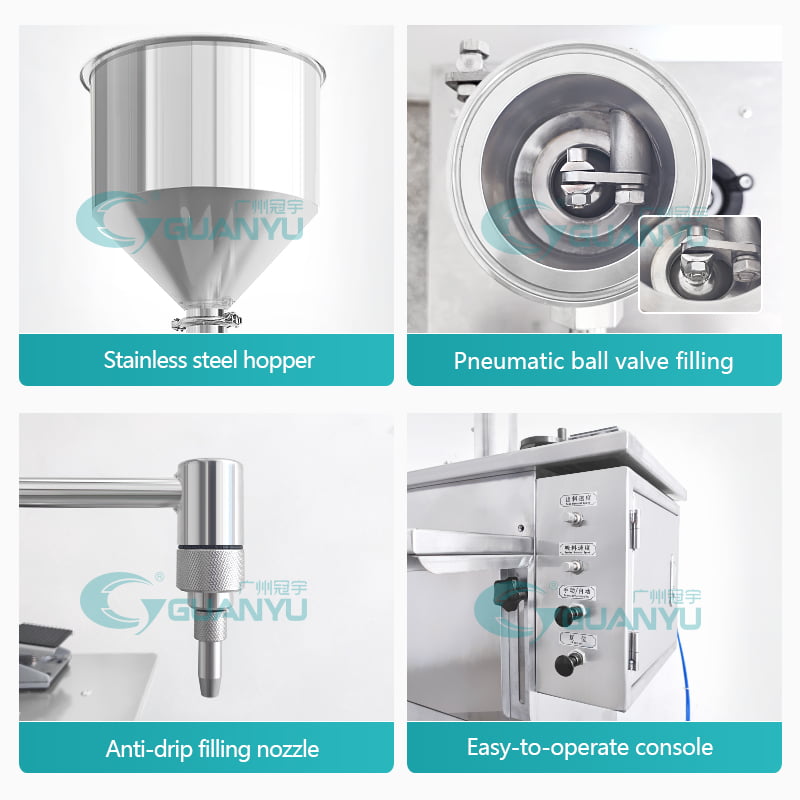
Case Study: Implementing Semi-Automatic Filling Machines
To illustrate the practical benefits of semi-automatic filling machines, consider the case of a mid-sized manufacturer of personal care products. The company faced challenges in meeting increasing demand while maintaining product quality and controlling costs. By implementing semi-automatic filling machines, they achieved significant improvements in their production process.
Initial Challenges
The company relied on manual filling methods, which were labor-intensive and prone to inconsistencies. Variations in fill volumes led to product wastage and quality issues, resulting in customer complaints and returns. Additionally, the slow filling process limited production capacity, hindering the company’s ability to scale and meet market demand.
The Solution
The company invested in semi-automatic piston fillers and pump fillers, tailored to their specific product range. These machines offered the precision and speed needed to improve efficiency and consistency. The semi-automatic nature of the machines allowed operators to retain some control over the process while significantly enhancing productivity.
Results
- Increased Production Capacity: The semi-automatic filling machines significantly increased the company’s production capacity. The faster filling process allowed the company to produce more units per shift, meeting the growing demand for their products.
- Enhanced Product Quality: The precision of the filling machines ensured that each container received the exact amount of product, eliminating variations and reducing waste. This consistency improved product quality and customer satisfaction, leading to fewer complaints and returns.
- Cost Savings: The efficiency gains achieved through the use of semi-automatic filling machines resulted in substantial cost savings. Reduced labor requirements, minimized waste, and increased productivity contributed to a more cost-effective production process.
- Operational Flexibility: The semi-automatic machines allowed the company to quickly switch between different products and container sizes, responding swiftly to market trends and customer preferences. This flexibility enhanced the company’s ability to innovate and expand its product line.
Conclusion
The introduction of semi-automatic filling machines represents a significant advancement in the production of daily chemical products. These machines offer a balanced solution that combines the efficiency and precision of automation with the flexibility and affordability required by small to medium-sized manufacturers. By improving production efficiency, accuracy, and consistency, semi-automatic filling machines help manufacturers meet the growing demand for high-quality products while controlling costs and maintaining operational flexibility.
As the market for daily chemical products continues to evolve, the adoption of semi-automatic filling machines will play a crucial role in enabling manufacturers to stay competitive and responsive to consumer needs. Investing in these machines not only enhances production capabilities but also ensures that manufacturers can deliver products that meet the highest standards of quality and performance.