Our Comprehensive Machine Inspection and Service Process
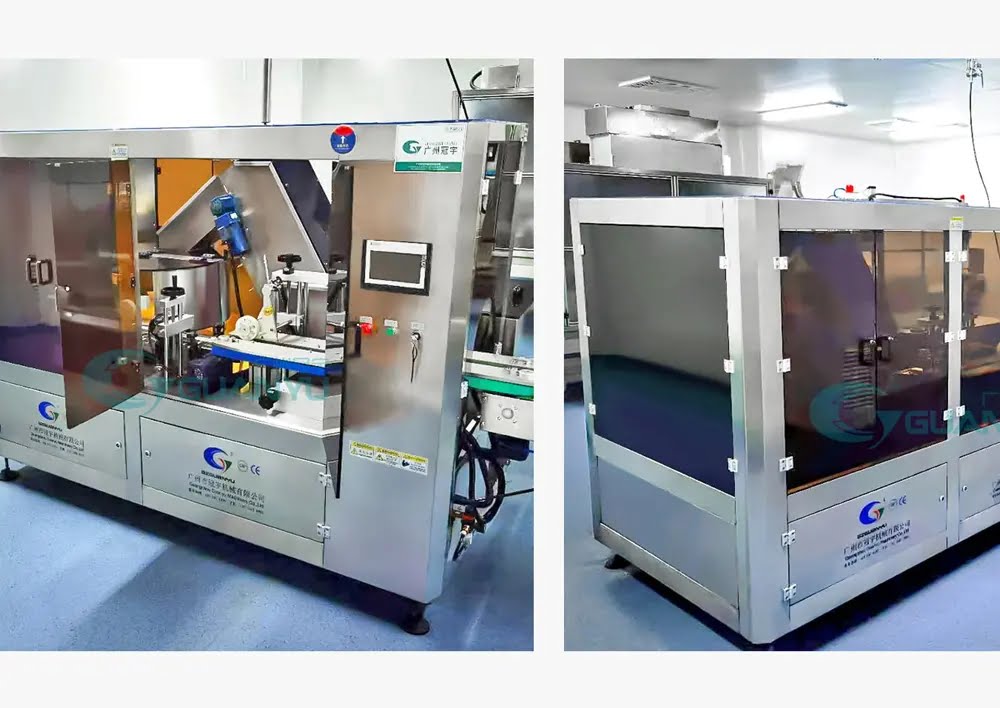
Ensuring the delivery of high-quality machinery is a core aspect of our service process. Prior to shipment, every machine undergoes a comprehensive inspection conducted by our experienced team. This meticulous pre-shipment inspection is designed to verify that the machine adheres to all specified quality and functionality standards. It aims to detect and address any potential issues, ensuring that the equipment is fully operational and complies with the desired specifications.
As part of our commitment to transparency and customer assurance, we meticulously document the inspection process through detailed video recordings. This video documentation is an integral component of our quality assurance protocol, providing a visual record of the machine’s condition and operational status. The video includes a step-by-step walkthrough, highlighting key functionalities, and demonstrating that each component performs as expected. By sharing this video with our customers prior to shipment, we enable them to independently verify the machine’s condition.
Such documentation serves multiple purposes. First, it offers customers a tangible assurance of the machine’s quality, fostering trust and confidence in our products. Second, it acts as a valuable reference point for post-delivery support, should any discrepancies arise. This proactive approach aligns with our commitment to transparency and reinforces our dedication to customer satisfaction. Lastly, it affords customers peace of mind, knowing they are receiving a product that has been thoroughly vetted and upheld to the highest standards.
Incorporating these rigorous pre-shipment inspections and comprehensive video documentation underscores our pledge to deliver only the best products. By ensuring machines meet all quality and functionality criteria before they leave our facility, we not only uphold our standards but also fortify the trust that our customers place in us.
Secure Packaging for Safe Delivery
Upon confirming that the machine meets all specified requirements, we focus on secure packaging to ensure its safety during transit. Our procedure begins with wrapping each machine in high-quality pearl cotton. This material is carefully chosen for its excellent shock-absorption properties, which significantly reduce the risk of damage from vibrations and impacts that may occur during transportation. This initial cushioning layer is critical in protecting delicate components and maintaining the machine’s integrity.
Following the application of pearl cotton, we proceed to place the wrapped machine into a robust wooden box. The wooden box is specifically designed to provide an additional layer of protection against heavy collisions and external pressure. Its sturdy construction ensures that the machine remains stationary and secure, minimizing the possibility of damage from movement during shipping. The box is sealed and reinforced with durable materials to prevent any potential breaches that could compromise the machine’s safety.
Throughout this packaging process, our team adheres to stringent protocols to guarantee that the machine arrives at the customer’s location without any impairment. Every step, from the cushioning to the boxing and sealing, is meticulously planned and executed to uphold our high standards of quality and reliability. This meticulous attention to packaging safeguards not only the physical condition of the machine but also upholds our commitment to delivering products that are ready for immediate use upon receipt.
Im Wesentlichen, our comprehensive packaging procedures reflect our dedication to ensuring that each machine is protected from the point it leaves our facility to the moment it is unpacked by our customers. This attention to detail in packaging is a crucial component of our overall service process, which emphasizes quality and continuous support.

Comprehensive Maintenance and Rapid Response Service
Our commitment to customer satisfaction does not end at delivery; it extends through the operational life of the equipment. We have established a robust maintenance service team comprising experienced on-site engineers and senior technicians. These professionals are equipped with the skills and tools needed to address any issues that may arise, ensuring that downtime is minimized and operations continue with minimal disruption.
The expertise of our team allows us to offer comprehensive maintenance services designed to keep machinery in optimal condition. Regular inspections and preventive maintenance work hand-in-hand to identify and resolve potential problems before they escalate into major issues. By focusing on preventative care, we help extend the lifecycle of the equipment while enhancing efficiency and performance.
In the event of any complications, our swift response capability sets us apart. Our team is prepared to rapidly travel to customer sites to perform necessary repairs and replacements. This rapid response minimizes downtime and ensures that your operations do not suffer prolonged interruptions. The ability to quickly mobilize a team of skilled engineers underscores our dedication to maintaining seamless operations for our customers.
Our senior technicians bring years of collective experience to every service call, applying their deep knowledge to diagnose problems accurately and implement effective solutions. Whether dealing with routine maintenance checks or unexpected breakdowns, our team’s prompt and proficient service is designed to meet the needs of diverse clients across various industries.
Overall, the combination of experienced professionals and a rapid response framework solidifies our position as a reliable partner in machine inspection and service. This ensures that our customers can expect comprehensive support that not only resolves issues quickly but also proactively maintains the quality and functionality of their equipment in the long term.
Global Support Network and Timely Quality Complaint Handling
At the core of our service provision lies a robust global support network, skillfully designed to address our clients’ needs—no matter where they are located. By strategically positioning engineering stations across key regions in Thailand, Europa, und Indien, we ensure that our team can swiftly deploy to any site requiring on-site service. This strategic placement forms a vital part of our commitment to offering prompt and reliable support to each and every one of our clients.
Our objective is to provide unmatched machine inspection and service processes, bolstering customer confidence in the reliability of their equipment. When it comes to addressing quality complaints, we understand the critical importance of timely action. Hence, our protocol dictates that any reported issues are acknowledged within one hour. We don’t just stop at acknowledgment; we promptly craft specific handling measures and recommendations tailored to the unique circumstances of each customer complaint.
This meticulous approach allows us to effectively mitigate the impact of any potential equipment downtime, ensuring that our clients’ operational efficiency is preserved. The utilization of a dedicated, multilingual support team further enhances our ability to offer bespoke guidance and technical resolutions swiftly. Through seamless coordination across our international stations, we are equipped to deliver expert service interventions at record speeds, underscoring our global reach and reliability.
The expansiveness of our support network is a testament to our dedication to providing continuous, quality service and reinforcing our global presence. This strategy not only allows us to offer timely and efficient resolutions but also maintains our clients’ trust in our systems and services. By integrating rapid response mechanisms and comprehensive support into our service framework, we stand by our promise to provide unwavering support, ensuring optimal performance and longevity of our machinery, regardless of geographic constraints.