Introduction to plain bar soap Production
The production of plain bar soap is a meticulous process that involves several stages, each crucial to ensuring the quality and consistency of the final product. At the forefront of this process is the initial stage, where stirring pots play a pivotal role. Understanding the importance of the stirring process in soap production is essential for appreciating the intricate balance of ingredients and techniques required to produce high-quality soap.
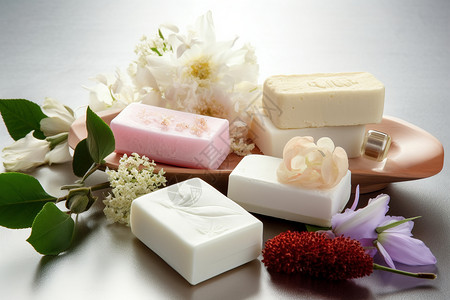
The stirring process is integral to the soap-making procedure, as it ensures that the various ingredients are thoroughly mixed and react appropriately. This stage typically involves the combination of fats or oils with an alkali, usually sodium hydroxide (lye), to initiate the saponification reaction. The stirring pot is where this reaction begins, and the quality of the mixing can significantly impact the texture, hardness, and overall performance of the soap.
Stirring pots used in soap production can vary in size and material, depending on the scale of the operation. For small-scale or artisanal soap makers, a simple stainless steel or heat-resistant plastic pot may suffice. These materials are chosen for their durability and resistance to the caustic nature of the ingredients. In larger industrial settings, more sophisticated equipment such as jacketed kettles with automated stirring mechanisms may be employed to ensure consistent and efficient mixing.
The ingredients used in ordinary soap typically include a blend of natural or synthetic fats and oils. Common choices are coconut oil, olive oil, palm oil, and animal fats like tallow. These fats react with the alkali to form soap and glycerin. The choice of oils can affect the soap’s properties, such as lather, moisturizing ability, and hardness. 此外, other additives like fragrances, colorants, and preservatives may be introduced during the stirring process to enhance the soap’s appeal and shelf life.
In conclusion, the initial stage of soap production involving stirring pots is fundamental to achieving a high-quality product. The thorough mixing of ingredients in the stirring pot ensures the success of the saponification process, ultimately determining the soap’s characteristics. As we delve deeper into the specifics of the equipment used, it becomes clear how each component contributes to the overall effectiveness and efficiency of soap production.
Types of Stirring Pots Used in Soap Production
The choice of stirring pot is crucial in the soap-making process, as it directly influences the quality of the final product and the efficiency of production. Traditional stainless steel pots are a popular option due to their robustness and high resistance to corrosion. These pots are particularly favored for their ability to withstand the caustic nature of soap-making ingredients without degrading over time. 此外, stainless steel pots are easy to clean, which is essential for maintaining hygiene standards in soap production.
Modern advancements have introduced electric stirring pots, which offer enhanced control and consistency. These pots come equipped with adjustable speed settings, allowing for precise emulsification of ingredients. Electric stirring pots are designed to maintain a consistent temperature, which is crucial for achieving uniformity in the soap mixture. This control over temperature and stirring speed can significantly improve the overall efficiency of the soap-making process, reducing the likelihood of errors and ensuring a high-quality product.
When selecting a stirring pot for soap production, several features should be considered to ensure suitability. Heat resistance is paramount, as the soap-making process often involves high temperatures that can damage less durable materials. The capacity of the pot is another important factor, as it should be sufficient to handle the volume of soap being produced without causing overflow or spillage. Ease of cleaning is also a critical feature, as remnants of previous batches can contaminate new mixtures and affect the quality of the soap.
The choice of stirring pot can also impact the emulsification of ingredients, a key step in soap-making that determines the texture and consistency of the final product. A pot that allows for thorough and even mixing will ensure that all ingredients are properly combined, leading to a smoother and more homogeneous soap. Ultimately, the right stirring pot can enhance the efficiency of the soap production process, leading to higher productivity and better-quality soap.
As time goes by, machines become more and more advanced and perfect. Here we recommend to you a great machine for making soap. our company hot sale product: open lid homogenizer mixing machine
open lid homogenizer mixing machine
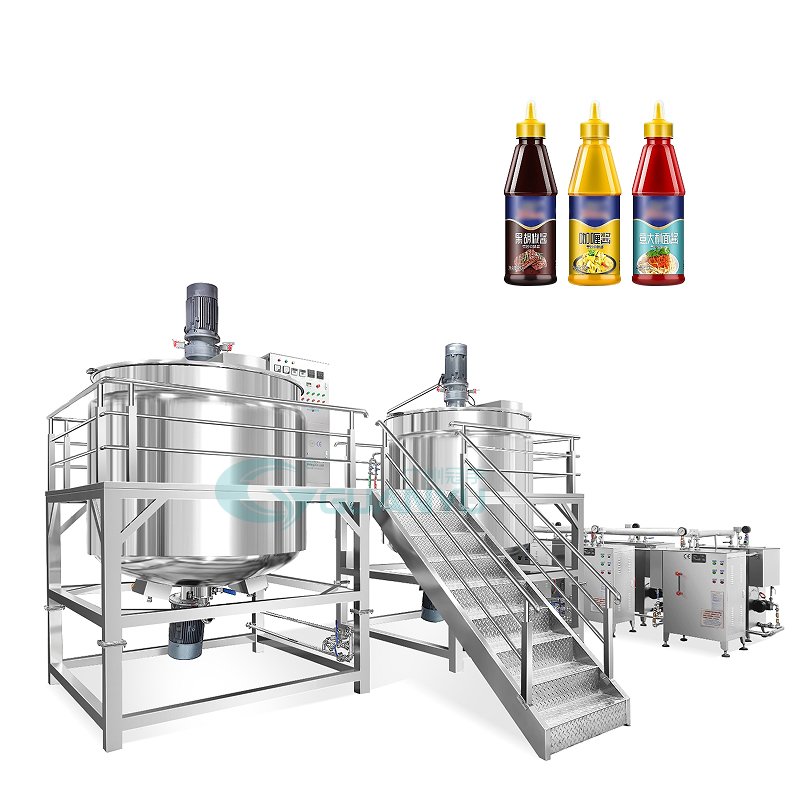
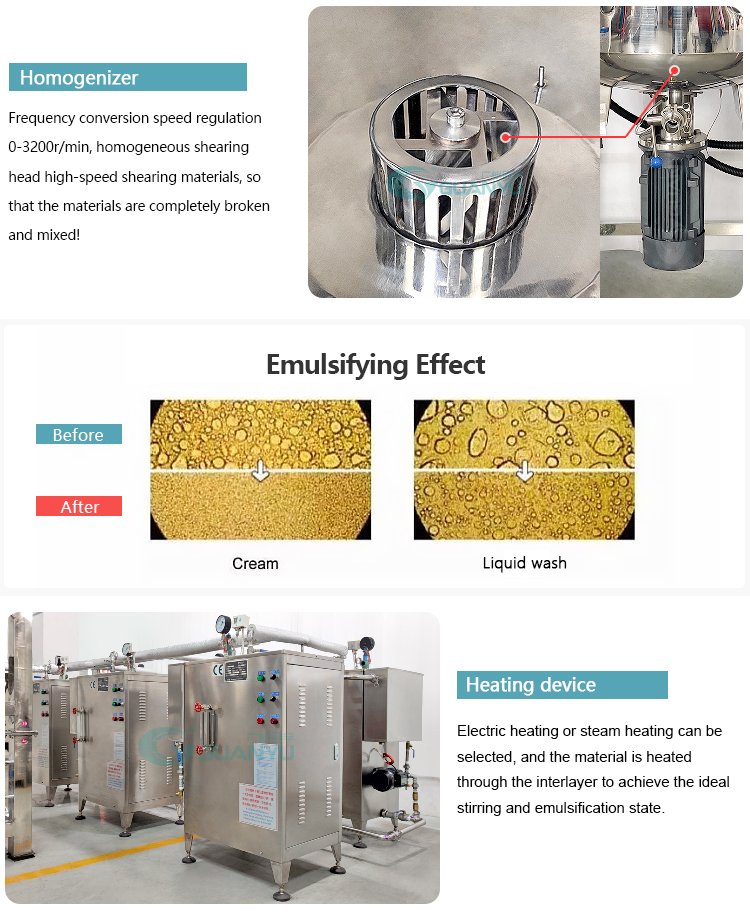
An open lid homogenizer mixing machine, often referred to as an open lid homogenizer or open lid mixing vessel, offers numerous advantages in the production of soap. This equipment is particularly valued in the soap manufacturing industry for its efficiency, versatility, and ability to produce high-quality products consistently. Here are the key benefits of using an open lid homogenizer mixing machine for soap production:
Enhanced Mixing and Homogenization
One of the primary advantages of an open lid homogenizer is its ability to achieve superior mixing and homogenization. The machine is designed to mix ingredients thoroughly, ensuring that all components are evenly distributed throughout the batch. This is crucial in soap production where uniformity in texture, 一致性, and ingredient dispersion directly impacts the quality of the final product. The homogenization process breaks down particles to a finer level, which is essential for producing smooth and high-quality soap.
Efficient Heating and Cooling
Open lid homogenizer mixing machines are equipped with heating and cooling systems that allow for precise temperature control. This is particularly important in soap production, where different phases of the process require specific temperatures. 例如, fats and oils need to be melted at controlled temperatures before being mixed with other ingredients. The machine’s ability to rapidly heat and cool the mixture ensures that the soap ingredients are processed at optimal temperatures, leading to better quality and stability of the final product.
Flexibility in Batch Sizes
These machines are designed to handle a wide range of batch sizes, making them suitable for both small-scale and large-scale soap production. The open lid design allows for easy adjustment of batch volumes, providing flexibility for manufacturers to produce different quantities based on demand. This versatility is advantageous for businesses looking to scale their operations or produce custom batches for specific market needs.
Ease of Operation and Maintenance
The open lid design of the homogenizer mixing machine simplifies the process of adding ingredients and monitoring the mixing process. Operators can easily access the interior of the machine, making it easier to add raw materials, inspect the mixture, and make any necessary adjustments. 此外, the open design facilitates easy cleaning and maintenance, reducing downtime and ensuring that the machine remains in optimal working condition. This ease of operation is particularly beneficial for maintaining consistent production schedules and minimizing production costs.
Improved Product Quality
Using an open lid homogenizer mixing machine in soap production leads to improved product quality. The thorough mixing and homogenization processes ensure that the final soap product has a consistent texture, color, and fragrance. The ability to control the mixing speed and duration allows manufacturers to fine-tune the process to achieve the desired product characteristics. This level of control is essential for producing high-quality soap that meets consumer expectations and stands out in the market.
Cost-Effective Production
The efficiency and effectiveness of open lid homogenizer mixing machines contribute to cost-effective soap production. The machines are designed to minimize waste and maximize the use of raw materials, reducing overall production costs. 此外, the ability to produce consistent batches reduces the likelihood of defects and the need for rework, further lowering production expenses. The energy-efficient design of these machines also helps in reducing operational costs, making them a financially viable option for soap manufacturers.
Versatility in Formulations
Open lid homogenizer mixing machines are capable of handling a wide variety of formulations, including solid bars, liquid soaps, and specialty products such as exfoliating soaps and moisturizing soaps. This versatility allows manufacturers to diversify their product offerings and cater to different market segments. The machine’s ability to handle different ingredients and additives without compromising the quality of the final product is a significant advantage for soap producers looking to innovate and expand their product lines.
结论
In summary, the open lid homogenizer mixing machine is a highly beneficial tool in soap production. Its ability to provide superior mixing and homogenization, efficient heating and cooling, flexibility in batch sizes, ease of operation and maintenance, improved product quality, cost-effective production, and versatility in formulations make it an indispensable asset for soap manufacturers. By investing in this equipment, producers can enhance their production processes, improve product quality, and achieve greater success in the competitive soap market.
More machines, welcome to our Alibaba official website:
https://gzguanyu.en.alibaba.com/?spm=a2700.shop_pl.88.5 |