The perfume making production industry is a complex and high-precision field that combines art and science to create fragrances that captivate the senses. Central to this process is a production line equipped with specialized machinery designed to handle the delicate ingredients involved. Однако, due to the volatile nature of many of these ingredients, particularly alcohol, safety is a paramount concern. This article explores the key equipment used in perfume production and highlights the importance of explosion-proof designs in ensuring both efficiency and safety in the manufacturing environment.
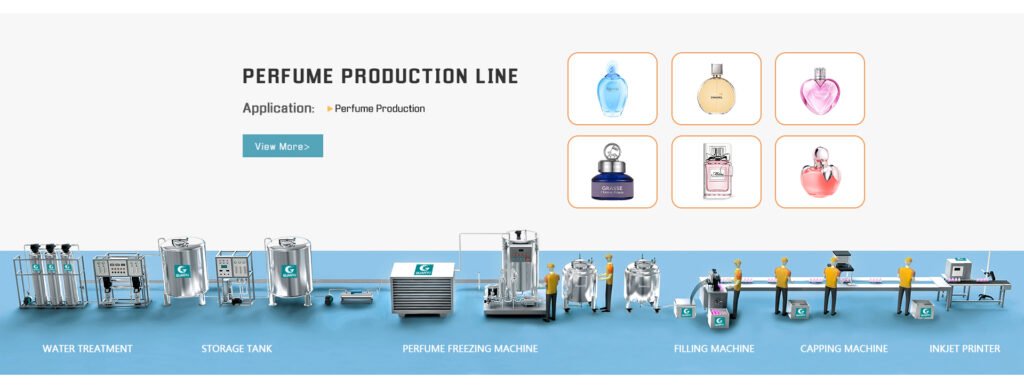
The Essential Components of a Perfume making Production Line
A modern perfume production line consists of several interconnected stages, each relying on sophisticated machinery to perform its role effectively. The main stages include manufacturing, наполнение, укупорка, and labeling. Each stage requires specific equipment designed to handle the unique challenges associated with working with flammable and sensitive materials.
Perfume Making Manufacturing Equipment: Precision and Safety Combined
The initial stage of perfume production involves the careful blending of various fragrance oils, solvents, and alcohol to create the base perfume. This process takes place in specialized manufacturing equipment that includes mixing tanks, agitators, and temperature control systems.
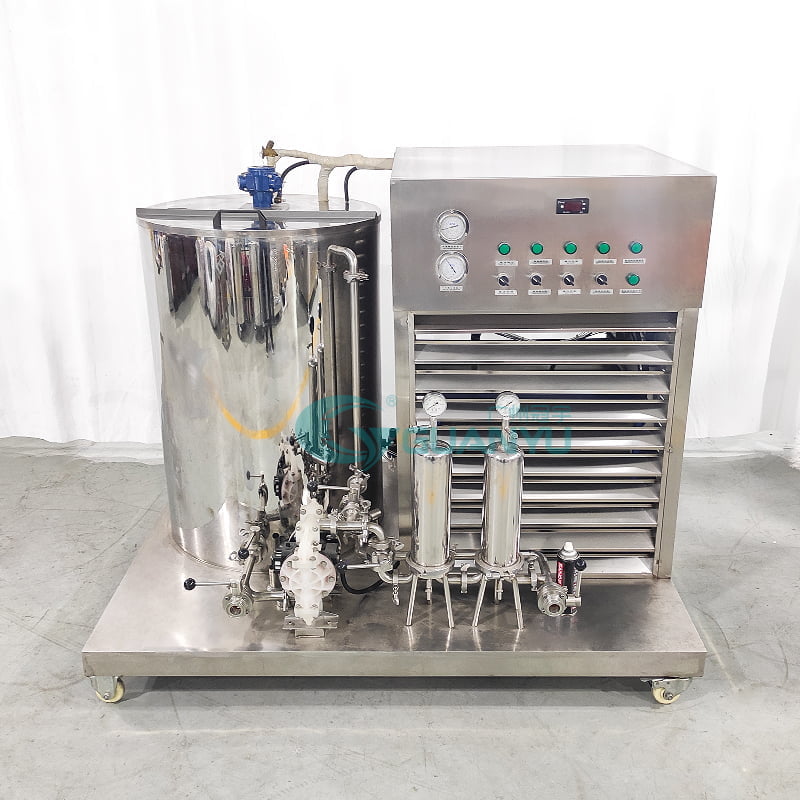
Explosion-Proof Features in Manufacturing Equipment
The use of alcohol and other volatile substances in perfume production creates an environment where the risk of explosion is always present. To mitigate this risk, manufacturing equipment is designed with several explosion-proof features:
- Hermetically Sealed Mixing Tanks: The mixing tanks used in perfume production are hermetically sealed to prevent the escape of flammable vapors. This containment is critical in reducing the risk of vapor accumulation, which could lead to an explosive atmosphere.
- Explosion-Proof Electronics: All electronic components within the manufacturing area are explosion-proof, meaning they are designed to operate at energy levels too low to ignite any flammable vapors. This includes control panels, датчики, and actuators, all of which play a crucial role in maintaining safety.
- Ventilation and Vapor Recovery Systems: The manufacturing area is equipped with advanced ventilation systems designed to remove flammable vapors from the air continuously. These systems often incorporate vapor recovery units that capture and recycle the vapors, not only improving safety but also reducing waste.
- Pressure and Temperature Monitoring: The equipment is fitted with sensors that continuously monitor pressure and temperature within the mixing tanks. If either parameter exceeds safe limits, automatic shut-off systems are triggered to prevent any potential hazards.
Filling Equipment: Balancing Precision with Protection
After the perfume is manufactured, it is transferred to filling machines, where it is carefully measured and dispensed into bottles. The filling process demands both accuracy and speed, as well as strict adherence to safety protocols due to the flammable nature of the perfume.
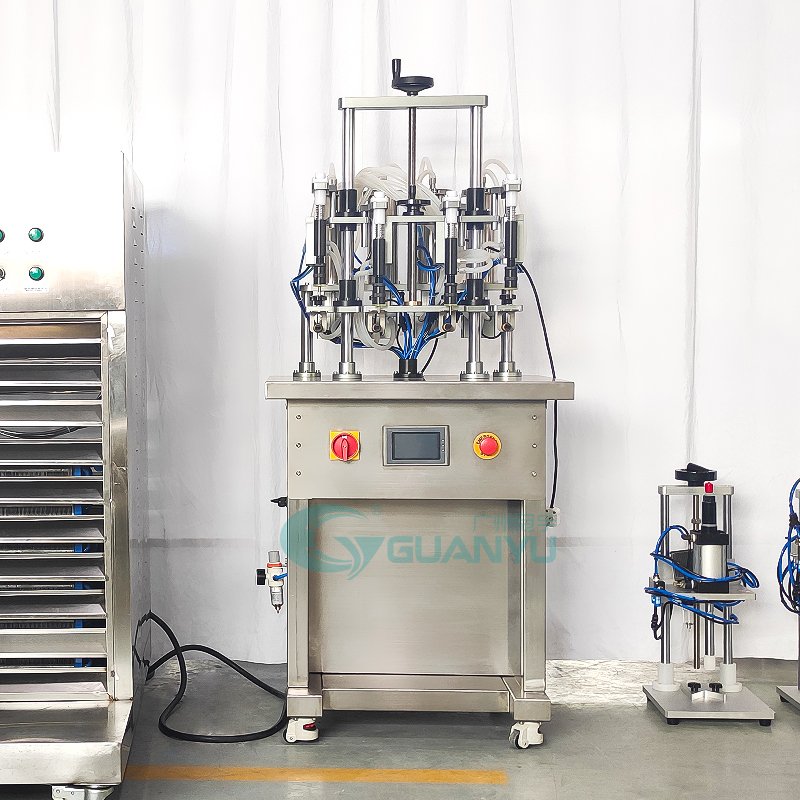
Explosion-Proof Features in Filling Equipment
The filling stage presents unique challenges, particularly in maintaining safety while ensuring each bottle is filled accurately. The explosion-proof design of filling equipment addresses these challenges in several ways:
- Enclosed Filling Chambers: The filling machines operate within enclosed chambers that are designed to contain any vapors released during the filling process. These chambers are often equipped with inert gas systems that displace oxygen, reducing the likelihood of combustion.
- Non-Sparking Materials and Components: The filling equipment is constructed from materials that are non-sparking and resistant to static electricity. This includes using stainless steel and other non-ferrous metals for parts that come into contact with the perfume, as well as ensuring that all moving parts are grounded to prevent static discharge.
- Leak Detection and Automatic Shutdown: Advanced sensors are integrated into the filling equipment to detect any leaks or spills that might occur during the process. If a leak is detected, the system automatically shuts down to prevent the release of flammable vapors into the production environment.
- Explosion-Proof Motors and Drives: The motors and drives used in the filling equipment are housed in explosion-proof enclosures, which are designed to contain any sparks or heat generated by the machinery. This ensures that even if an internal fault occurs, it will not result in an external explosion risk.
Capping and Labeling: Securing the Product Safely
Once the perfume is bottled, the next steps involve capping and labeling. These processes are crucial for ensuring the product’s integrity and for maintaining brand consistency. Although these stages are less hazardous than manufacturing and filling, they still require careful attention to safety.
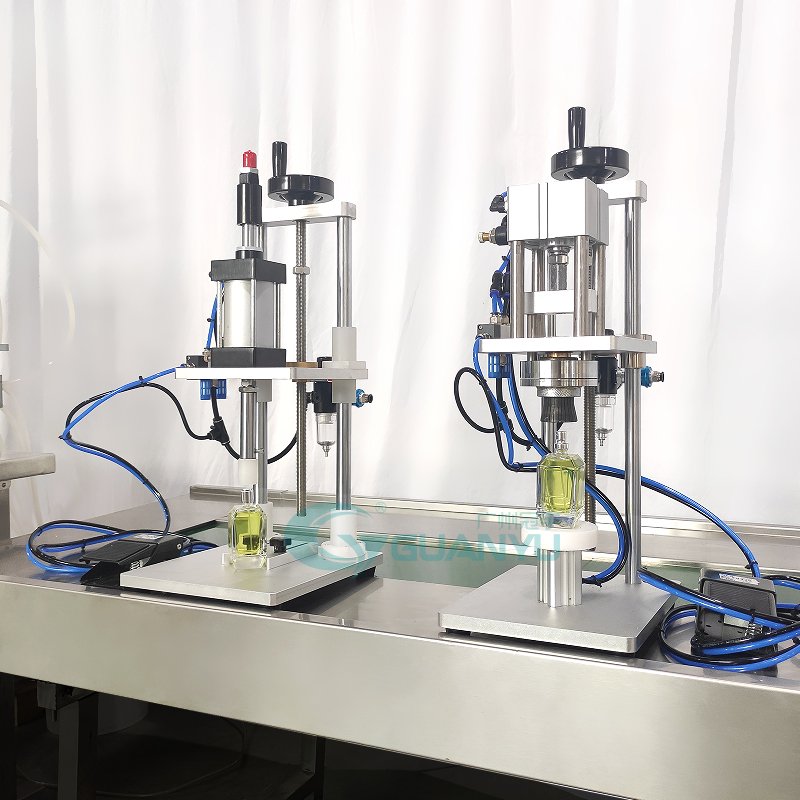
Safety Measures in Capping Equipment
Capping is the process of sealing the bottles to ensure that the perfume does not leak or evaporate. The equipment used for capping must be both precise and safe:
- Torque-Controlled Capping Heads: The capping equipment uses torque-controlled heads that apply the correct amount of force to seal the bottle without causing damage. This precise control minimizes the risk of creating sparks, which could occur if too much force is applied.
- Material Selection: Non-sparking materials are used in the parts of the capping machine that come into direct contact with the bottle and cap. This is particularly important if the capping process involves metal components, as improper materials could generate friction and heat.
Explosion-Proof Considerations in Labeling Equipment
Labeling might seem like a straightforward process, but it still involves potential risks, especially in environments where flammable vapors are present. The labeling equipment is designed with safety in mind:
- Antistatic Design: The labeling machines are designed to minimize the buildup of static electricity. This is achieved through the use of antistatic materials and grounding systems, which prevent static discharge that could ignite flammable vapors.
- Safe Adhesives: The adhesives used in labeling are selected for their low-temperature application, ensuring that no unnecessary heat is generated during the labeling process. This is crucial in maintaining a safe working environment.
Comprehensive Safety Protocols in Perfume Production
In addition to the explosion-proof design of the equipment, maintaining a safe perfume production line also requires stringent safety protocols. These protocols encompass regular maintenance, employee training, and robust emergency response planning.
- Routine Maintenance and Inspections: Regular maintenance of all equipment is essential to ensure that safety features remain effective. This includes inspecting explosion-proof enclosures, testing ventilation systems, and verifying that sensors and automatic shut-off mechanisms are functioning correctly.
- Employee Training and Awareness: Employees working in perfume production must be thoroughly trained in safety procedures, including the correct handling of flammable materials and the operation of explosion-proof equipment. Continuous training ensures that all staff are aware of potential risks and know how to respond in an emergency.
- Emergency Response Planning: A well-developed emergency response plan is critical in the event of an incident. This plan should include procedures for safe evacuation, the use of fire suppression systems, and coordination with emergency services. Regular drills and simulations help ensure that all employees are prepared to act swiftly and effectively in an emergency.
Заключение
The production of perfume is a sophisticated process that requires careful attention to both precision and safety. By incorporating explosion-proof designs into manufacturing, наполнение, укупорка, and labeling equipment, perfume producers can significantly reduce the risk of accidents, ensuring that the production line operates smoothly and safely. These safety measures, combined with strict maintenance protocols and comprehensive employee training, form the backbone of a safe and efficient perfume production environment.
As the industry continues to innovate, the emphasis on safety will remain paramount, driving further advancements in equipment design and production practices. For those interested in exploring more about safety and automation in industrial settings。