Overview of Production Equipment Solution
In industries such as cosmetics, daily chemicals, produtos farmacêuticos, and food, the selection and integration of production equipment play a pivotal role in ensuring efficiency, qualidade, and compliance. This guide aims to introduce the critical types of equipment necessary for these sectors, showcasing the benefits of engaging a one-stop solution provider. These providers offer a comprehensive suite of machinery and production lines tailored to meet diverse production demands, making them indispensable to modern manufacturing processes.
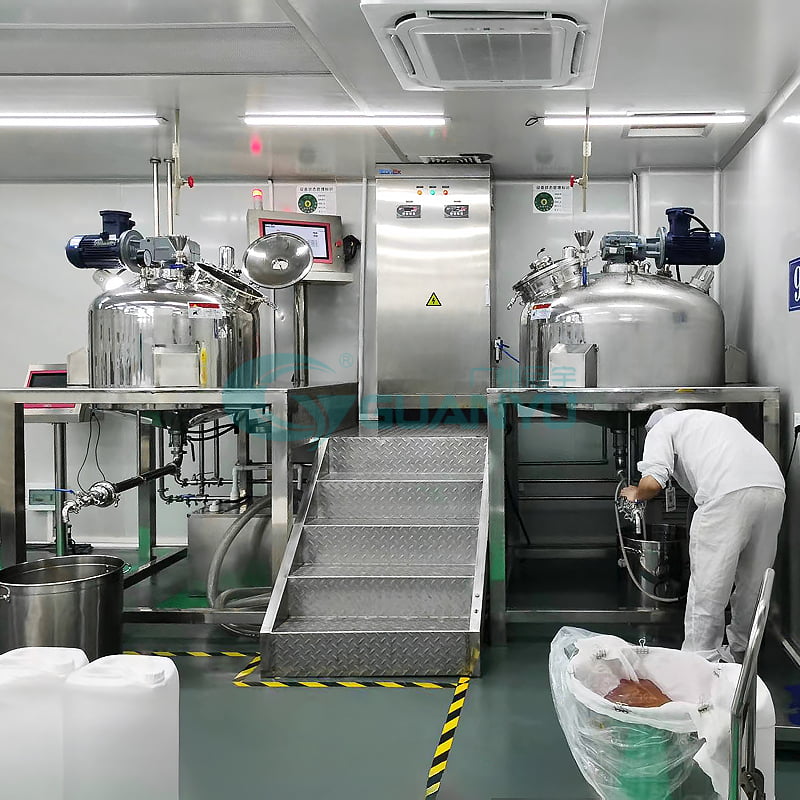
The demand for quality and uniformity in production has driven the need for advanced machines capable of precise and efficient operation. Within the cosmetics industry, mixers, homogenizers, and filling machines ensure that products are consistent, safe, and meet stringent regulatory standards. Similarly, in the daily chemicals sector, emulsifying mixers, reactors, and dispersion machines are vital for creating products with the right viscosity, texture, and shelf-life.
In pharmaceuticals, where accuracy and sterility are paramount, encapsulation machines, tablet presses, and coating machines must meet rigorous sanitary and operational guidelines. Além disso, food industries rely heavily on an array of equipment such as mixers, sterilizers, packaging machines, and conveyors to maintain hygiene, maximise productivity, and adhere to food safety standards. Hence, integrating each of these pieces of equipment from different suppliers can be cumbersome and often leads to inefficiencies and increased costs.
Opting for a one-stop solution provider can mitigate these challenges by offering a holistic and cohesive machinery setup tailored to specific industry needs. The advantages, such as streamlined procurement processes, reduced compatibility issues, and cost-effective maintenance, are significant. Adicionalmente, such providers ensure that all equipment complies with relevant industry standards, thus enhancing overall production integrity and efficiency.
Resumindo, sourcing production equipment from a single provider not only simplifies operational logistics but also enhances productivity and cost efficiency, making it a strategic choice for industries aiming for seamless and high-quality production processes.
Types of Vacuum Emulsifying Machines
Vacuum emulsifying machines are essential tools across several industries, including cosmetics, daily chemicals, produtos farmacêuticos, and food production. These machines are engineered to create homogenous mixtures by breaking down and blending different ingredients in a controlled vacuum environment. This process is pivotal for ensuring the consistency and stability of the end products.
The two primary types of vacuum emulsifying machines are fixed vacuum emulsifying machines and hydraulic lifting vacuum emulsifying machines. Both types play a significant role in the production process, each offering unique advantages depending on the specific requirements of the application.
Fixed vacuum emulsifying machines are designed for settings where the production requirements remain primarily constant. These machines are stationary and ideal for high-volume production runs, offering robust performance and reliability. The fixed design minimizes potential disruptions during operation, ensuring uniform mixing and emulsification. The consistent application of vacuum pressure in these machines significantly reduces the presence of air bubbles, leading to a finer, more stable product.
On the other hand, hydraulic lifting vacuum emulsifying machines provide remarkable flexibility and ease of use. These machines feature a hydraulic system that allows the mixing chamber to be raised or lowered, facilitating easier material handling and cleaning procedures. This flexibility is particularly beneficial for small to medium batch productions where frequent changeovers are common. The advanced automation incorporated into these machines also enhances productivity and reduces manual labor.
Technological advancements have further refined the efficiency of vacuum emulsifying machines. Modern units are equipped with intelligent control systems, allowing precise control over mixing speeds, temperature, and vacuum levels. These enhancements not only improve the quality of emulsification but also ensure optimal energy consumption and reduced operational costs. In cosmetics, por exemplo, achieving a smooth and stable formulation is crucial, while in pharmaceuticals, consistent particle size and distribution are paramount. Similarly, in the food industry, these machines ensure that emulsions, such as sauces and dressings, have the desired texture and stability.
Understanding the different types of vacuum emulsifying machines and their specific applications across various industries highlights their critical role in modern production environments, promoting efficiency, product quality, and operational effectiveness.
Diverse Range of Filling Machines
Filling machines are critical in the production processes across multiple industries, including cosmetics, daily chemicals, produtos farmacêuticos, and food. These machines streamline the packaging process, ensuring efficiency and precision. Various types of filling machines are available, each suited for specific applications and production scales.
Pneumatic filling machines operate using compressed air, allowing for high-speed filling. They are particularly advantageous in environments where electricity usage needs to be minimized or is regulated strictly. Their ability to fill at consistent speeds makes them ideal for large-scale production, ensuring uniformity and quality in the final product.
Mechanical filling machines, on the other hand, rely on mechanical components and movements to perform the filling operations. These machines are robust and reliable for long-term use. They are highly regarded in large-scale production environments due to their durability and the minimal maintenance they require. Mechanical filling machines are favored for their precision, making them suitable for industries requiring meticulous dosing, such as pharmaceuticals and food processing.
Pedal filling machines are manual but feature a foot-operated mechanism, offering a balance between control and ease of use. These machines are essential in small-scale productions or environments where speed is not the primary concern. They allow for greater manual control, making them suitable for specialty products where nuanced filling is necessary, often seen in small-batch cosmetics and artisanal food production.
Manual filling machines are the simplest form of filling technology, operated entirely by hand. These machines are perfect for very small-scale operations or low-budget setups, providing the most control over the filling process. They are used widely in environments where automation is not viable and where precision is more critical than speed, such as in laboratories or small-scale pharmaceutical compounding.
The choice of filling machine significantly impacts production efficiency and product quality. Whether pneumatic, mecânico, pedal, or manual, each type serves a specific need, maintaining consistency and quality across various production scales. These machines are essential in tailoring the production process to meet industry-specific standards and consumer expectations.
Supporting Equipment and Production Lines
Supporting equipment and comprehensive production lines form the backbone of numerous industries, including cosmetics, daily chemicals, produtos farmacêuticos, and food. Essential auxiliary equipment such as reaction agitator kettles, máquinas de cosméticos, chemical machinery, and water treatment equipment are indispensable for realizing seamless and efficient production processes.
Reaction agitator kettles play a critical role in mixing and chemical reactions, ensuring homogeneity and precise control over reaction conditions. These kettles come in various forms, including double-layer, triple-layer, and jacketed, allowing tailored utilization based on specific production needs. Their adaptability makes them prominent in industries requiring precise temperature control and uniform mixing.
In cosmetics manufacturing, specialized machinery is key. This includes high-shear mixers for emulsification processes, filling and capping machines, and labeling equipment. These machines are designed to handle the delicate formulations of skincare and makeup products, ensuring consistency in texture and stability in product formulations.
The daily chemicals sector benefits from advanced chemical machinery that handles everything from mixing to packaging. Por exemplo, detergent and cleaning product manufacturers rely on dedicated blenders, dosing systems, and filling lines that smoothly integrate with other production equipment, ensuring streamlined operations.
Water treatment equipment is another critical component in production lines, especially relevant for industries where high water purity standards are mandatory. Systems like reverse osmosis, deionization, and ultrafiltration ensure that the water used in production processes meets stringent quality requirements, thereby safeguarding product integrity.
The integration of these support systems into comprehensive production lines not only enhances production speed but also ensures higher quality assurance. Automated processes reduce human error and downtime, leading to consistent output and operational efficiency. With fully integrated production lines, industries can achieve optimized workflows, leading to cost savings and improved product quality, providing a substantial advantage in competitive markets.