Introduction to Homogenizing Mixers
Homogenizing mixers play a crucial role in the cosmetic and dental care industries, particularly in the production of products such as toothpaste and cosmetic creams. These machines are designed to create a uniform and consistent mixture by reducing the particle size of the components involved. The process of homogenization ensures that ingredients are evenly distributed throughout the mixture, preventing separation and ensuring that the final product maintains its intended quality, texture, and performance.
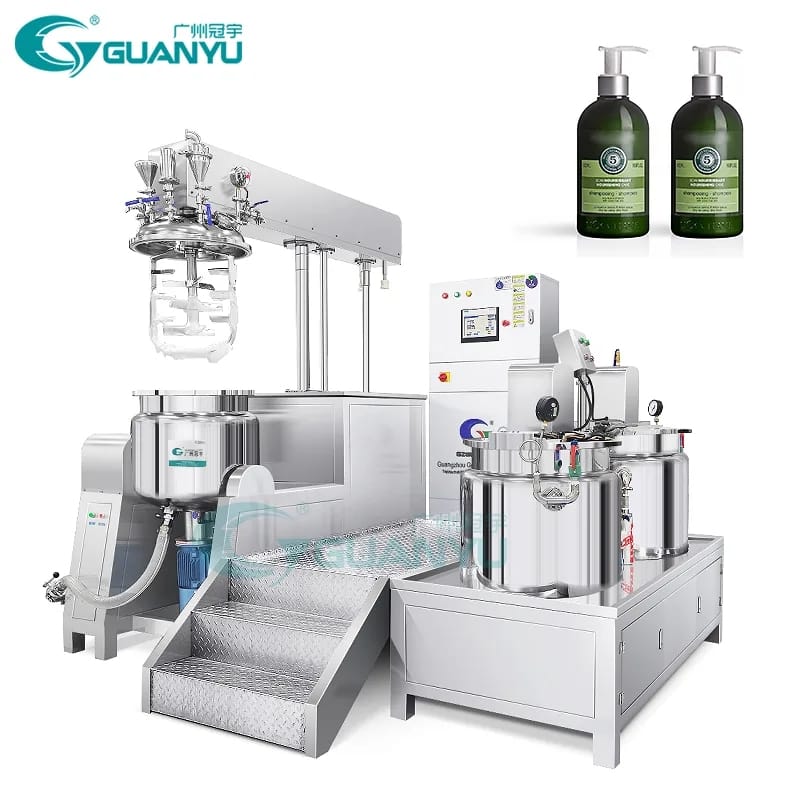
The fundamental principle behind homogenizing mixers is the application of mechanical forces that break down particles, resulting in a smoother and more stable emulsion. The machines utilize high shear forces to mix and emulsify the ingredients, effectively achieving a homogenous product. This is particularly essential in the formulation of toothpaste, where a consistent mixture contributes to the efficacy of the active ingredients, such as fluoride and abrasives, which work together to promote oral health.
In the context of cosmetic cream production, the role of homogenizing mixers is equally significant. Creams often contain various oils, water, and emulsifiers, which must be blended uniformly to achieve a desirable texture, stability, and appearance. A well-homogenized cosmetic cream not only enhances the sensory experience for the user but also ensures better absorption of active ingredients into the skin, effectively delivering the promised benefits of hydration, rejuvenation, and protection.
Portanto, investing in efficient homogenizing mixers is vital for manufacturers aiming to produce high-quality toothpaste and cosmetic products. These machines not only enhance the production process but also contribute to the overall success of the final product in the competitive market. By leveraging the capabilities of homogenizing mixers, companies can ensure that they consistently meet consumer demands for quality and efficacy in their toothpaste and cosmetic creams.
Understanding the Ingredients: What Goes into Toothpaste and Creams
Toothpaste and cosmetic creams are formulated with a variety of ingredients, each selected for its specific function and efficacy. Understanding these components is crucial for both manufacturers and consumers, as they play a significant role in the effectiveness and safety of the final product. Commonly, toothpaste contains abrasives, humectants, thickeners, flavoring agents, and active ingredients like fluoride. Abrasives, such as calcium carbonate or silica, are essential for removing plaque and stains from teeth while ensuring minimal wear on enamel.
Humectants, including glycerin and sorbitol, are added to retain moisture, preventing the toothpaste from drying out. Thickeners, such as xanthan gum, contribute to the product’s texture and viscosity, ensuring it can be easily dispensed and applied. Flavoring agents, often in the form of mint or fruit extracts, enhance the sensory experience, making oral care more pleasant. The inclusion of active ingredients, most notably fluoride, is crucial for dental health as they help strengthen enamel and prevent cavities.
On the other hand, cosmetic creams typically comprise emollients, emulsifiers, preservatives, and active ingredients tailored for skin health. Emollients, like oils or butters, provide moisture and improve skin texture. Emulsifiers facilitate the mixing of oil and water phases, creating a stable and homogeneous product. Preservatives are essential in preventing microbial growth, ensuring product safety and longevity. Adicionalmente, active ingredients such as retinol, hyaluronic acid, or antioxidants target specific skin concerns, from aging to hydration.
The interaction of these components is critical during the mixing and homogenization process. High-shear mixers, por exemplo, enable efficient blending by creating a uniform and stable product, which enhances the performance of the ingredients. The selection of appropriate machinery—such as homogenizers—ensures that the desired texture and consistency are achieved, underscoring the importance of understanding ingredient functionality in product formulation.
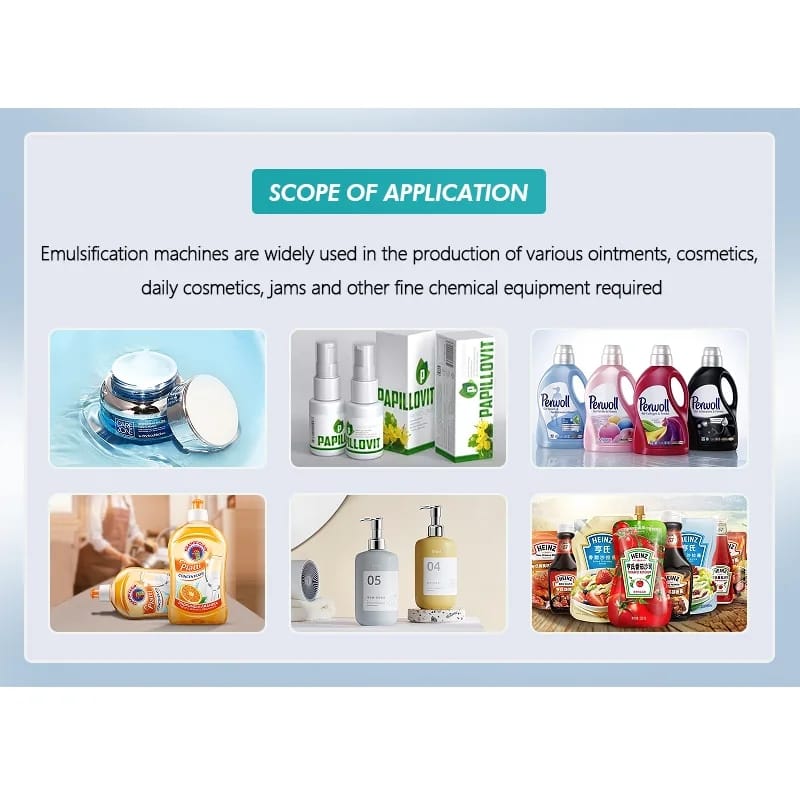
The Importance of Emulsification in Cosmetic Products
Emulsification plays a critical role in the formulation of cosmetic products, particularly in creams and lotions that typically contain both oil and water phases. The process of emulsification involves the stabilization of these phases, resulting in a homogenous mixture that ensures the proper distribution of ingredients. Without effective emulsification, formulations may separate, leading to inconsistency in texture, efficacy, and overall product quality.
Homogenizing mixers are essential tools in achieving effective emulsification. These machines utilize high shear forces to create small droplets of one phase, which are then dispersed within the other phase. This mechanical action facilitates the merging of the oil and water components, qual, when combined with the appropriate emulsifiers, results in a stable and uniform product. The efficiency of homogenizers enables cosmetic manufacturers to produce formulations that maintain their integrity throughout their shelf life, thus enhancing consumer satisfaction.
Different types of emulsifiers are employed based on the desired characteristics of the final product. For instance, natural emulsifiers such as beeswax or lecithin might be chosen for their gentle properties, while synthetic emulsifiers, like polysorbates or glycol stearate, may be utilized for their ability to create high-performance formulations. The type of emulsifier selected significantly impacts the formulation temperature, viscosity, and feel on the skin, making it a fundamental consideration in the development of cosmetic creams.
Opting for the right homogenizing mixer and emulsifier is vital for achieving stable emulsions in cosmetic products. The synthesis of these components, guided by principles of emulsification, ultimately determines the quality and effectiveness of creams, solidifying their place as indispensable elements of cosmetic science.
Features to Look for in a Homogenizer for Cosmetic Cream Making
When selecting a homogenizer for cosmetic cream production, several key features and specifications are integral to ensuring efficient and high-quality mixing. First and foremost, the mixing capacity of the homogenizer must align with the production goals. Homogenizers are available in various sizes, and the selection should consider the volume of the batches being produced to maintain consistency and meet demand.
Power is another critical aspect; a robust motor allows for efficient processing of cosmetic ingredients, ensuring thorough mixing and emulsification of the cream. A higher power rating in a homogenizer often translates to better performance with thicker formulations, which is common in cream production. Manufacturers should also assess the speed control features of the homogenizer. Variability in speed allows for customization according to the texture and viscosity of the cosmetic cream, enabling producers to formulate products with a desired consistency.
The material quality of the homogenizer is paramount as well, particularly in the cosmetics industry where hygiene standards are stringent. Stainless steel is the preferred material due to its durability and non-reactive properties, preventing contamination of cosmetic formulations. It’s advisable to select models that are compliant with industry regulations and adhere to sanitary design principles.
Lastly, ease of cleaning should not be overlooked. The design of the homogenizer should facilitate quick and effective cleaning processes, especially when switching between different formulations. This feature reduces downtime and enhances productivity, allowing manufacturers to operate efficiently without compromising the quality of their cosmetic creams. By evaluating these features carefully, manufacturers can make a well-informed choice that meets their specific production needs.
Types of Homogenizing Mixers and Their Applications
Homogenizing mixers play a critical role in the production of various products, particularly in the toothpaste and cosmetic industries. The choice of mixer can significantly impact the quality and consistency of the final product. Among the various types available on the market, rotor-stator mixers and high-shear mixers stand out due to their effectiveness in creating homogenous mixtures. Each type of mixer comes with its unique features that cater to different application needs.
Rotor-stator mixers are commonly employed in both toothpaste and cosmetic formulations. This design consists of a rotating element that creates a strong shear force against a stationary element, effectively breaking down particles and ensuring uniform distribution of ingredients. They are particularly suitable for mixing thick pastes and creams, where consistency is essential. These mixers are frequently used in the production of toothpaste, where achieving a uniform blend of abrasives, binders, and flavors is critical.
High-shear mixers, on the other hand, utilize a different mechanism to achieve homogenization. This type of mixer functions by forcing the mixture through a narrow gap between the rotor and the stator at high speeds. This process creates intense shear and turbulence, effectively reducing particle size and enhancing the dispersion of various components. High-shear mixers are particularly advantageous in cosmetic applications, such as emulsifying oils and water phases in creams and lotions, where a stable emulsion is crucial for product performance.
In addition to rotor-stator and high-shear mixers, other designs such as static mixers and inline mixers are also used for specific purposes within these industries. Static mixers promote continuous mixing without moving parts, making them ideal for certain toothpaste formulations. Inline mixers, which can be integrated into production lines, ensure consistent quality during manufacturing processes. Each type of homogenizing mixer serves a distinct purpose, making it essential for manufacturers to choose the correct equipment based on their specific application needs.
Step-by-Step Process of Making Toothpaste and Cosmetic Creams
Creating high-quality toothpaste and cosmetic creams requires a systematic approach, particularly when utilizing a homogenizing mixer. The initial step entails the careful preparation of ingredients. It is essential to gather all necessary components, including the active ingredients, abrasives, humectants, thickeners, flavoring agents, and preservatives for toothpaste. For cosmetic creams, ingredients such as emulsifiers, Óleos, waxes, and water-soluble substances should be assembled. Ensuring that these ingredients are of pharmaceutical or cosmetic grade is crucial for effectiveness and safety.
Once the ingredients are prepared, the mixing process begins. The homogenizing mixer plays a vital role at this stage, as it efficiently combines the selected components to create a uniform blend. Typically, the liquid ingredients are added first to the mixer, followed by the powders. Depending on the specific formulation, the mixer may need to operate in a vacuum environment to prevent air incorporation, which can adversely affect the texture and stability of the final product. During this phase, controlling the mixing speed and time is essential to achieve the desired consistency.
Temperature control is another critical factor in the production workflow. Many formulations require heat to dissolve specific materials or to facilitate emulsification. Thus, monitoring the temperature within the homogenizing mixer is necessary to ensure that it stays within optimal ranges. Adjustments can be made based on the formulations used, ensuring proper melting of waxes and emulsifiers for cosmetic creams or activating certain ingredients in toothpaste.
After mixing and achieving the necessary texture, the next step involves quality testing. This includes checking viscosity, pH levels, and microbial contamination to guarantee the safety and efficacy of both the toothpaste and cosmetic creams. These tests ensure the final products meet industry standards before being packaged and distributed, thereby securing consumer trust and satisfaction.
Troubleshooting Common Issues with Homogenizing Mixers
Homogenizing mixers play a critical role in the production of toothpaste and cosmetic creams, yet users may encounter a range of problems during the mixing process. Understanding these common issues is essential for maintaining optimal performance and ensuring the desired quality of the final product. One of the most frequent problems is separation, where the ingredients do not fully blend together, leading to visible layers in the mixture. This issue can often be attributed to inadequate mixing speed or an improper choice of mixer configuration. To combat this, operators should ensure that the homogenizing mixer is set to the correct speed and time based on the specific formulation requirements.
Another prevalent concern relates to inadequate emulsification, which can result in uneven distribution of ingredients, particularly in emulsified products like creams. This can be caused by insufficient shear force or improper temperature during the mixing process. To enhance emulsification efficiency, it may be necessary to preheat certain ingredients or adjust the mixing time to allow for better incorporation of the phases. Adicionalmente, using a high-shear mixer can aid in achieving a smoother texture and preventing separation.
Inconsistent texture is also a common issue that can frustrate manufacturers. Variations in viscosity or graininess can compromise the product’s quality. Troubleshooting this problem involves inspecting the ingredient quality and ensuring that all components are within specifications. Regular maintenance of the homogenizing mixer is also crucial; worn-out seals or blades can negatively affect the mixing efficiency. Operators should establish a routine maintenance schedule to check and replace any worn parts as needed. By proactively addressing these challenges and implementing effective solutions, manufacturers can significantly enhance their mixing processes and improve overall product quality.
Sustainability and Innovation in Cosmetic Manufacturing
The cosmetic industry is undergoing a significant transformation as brands increasingly prioritize sustainability in their product development processes. This shift is not merely a response to consumer demand for eco-friendly products but also a strategic move to reduce environmental impact and promote corporate social responsibility. As part of this transformation, the implementation of homogenizing mixers has emerged as a vital innovation in producing sustainable cosmetic formulations, including toothpaste and creams.
Homogenizing mixers are indispensable in ensuring consistent texture and quality in cosmetic products. These advanced machines facilitate the integration of natural and biodegradable ingredients, minimizing reliance on synthetic additives. By adopting such mixers, manufacturers are able to create smoother, more uniform mixtures that not only enhance product performance but also align with sustainable practices. Além disso, these mixers help in optimizing the use of raw materials, thus reducing waste and electrical consumption, which further supports eco-friendly production methodologies.
Adicionalmente, the use of innovative materials in cosmetic manufacturing has gained traction. Many companies are exploring the possibilities of utilizing renewable resources and biodegradable packaging. For instance, plant-based emulsifiers and organic preservatives are becoming popular alternatives to traditional synthetic options. This trend reflects a growing awareness of the connection between product ingredients and overall environmental impact.
Furthermore, the industry is witnessing the rise of eco-conscious brands that engage in transparent sourcing and ethical manufacturing practices. By promoting ingredient traceability and honoring fair trade practices, these brands foster consumer trust and contribute positively to community welfare. The combination of sustainability-minded ingredients and advanced homogenizing mixers presents an exciting opportunity for innovation that could redefine standards in cosmetic manufacturing.
Ultimately, as the demand for sustainable personal care products continues to grow, the integration of sustainable practices and cutting-edge machinery like homogenizing mixers will be crucial in shaping the future of the cosmetic industry. This commitment to eco-friendly manufacturing processes not only supports a greener planet but also empowers consumers to make informed choices about the products they use.
Conclusion: Choosing the Right Blender for Your Needs
The selection of an appropriate homogenizing mixer is crucial in the production processes of toothpaste and cosmetic creams. Both of these products demand a precision-engineered blending system that ensures the uniformity and consistency of the final output. A well-chosen homogenizing mixer will not only enhance the quality of the products but also significantly improve operational efficiency, leading to reduced waste and optimized production timelines.
When evaluating the ideal blender for your needs, there are several factors to consider. First, the scale of production plays an essential role. For large-scale manufacturing operations, a high-capacity homogenizing mixer that can handle substantial batches efficiently is necessary. Alternatively, smaller or artisanal producers may find that a compact, versatile model meets their specific requirements without overwhelming their production capacity.
Adicionalmente, the type of formulation being processed is pivotal. Toothpaste and cosmetic creams have different viscosity profiles and require tailored mixing solutions. Understanding the specific characteristics of the materials involved—including viscosity, pH levels, and the presence of sensitive ingredients—will guide the selection of the right blender.
The technology employed in the homogenizing mixer also bears consideration. Advanced mixers equipped with cutting-edge technology provide greater control over the mixing process, allowing manufacturers to achieve specific textures and particle sizes that meet regulatory standards and consumer expectations. Além disso, the ease of maintenance and operational costs related to the machines should factor into the decision-making process to ensure economic viability.
Resumindo, the right homogenizing mixer can be a game-changer for manufacturers in the toothpaste and cosmetic cream industries. By weighing the production demands, material properties, and technological capabilities, businesses can invest in equipment that enhances product quality while maximizing process efficiency.
Your point of view caught my eye and was very interesting. Thanks. I have a question for you.
I don’t think the title of your article matches the content lol. Just kidding, mainly because I had some doubts after reading the article.
Your point of view caught my eye and was very interesting. Thanks. I have a question for you. https://accounts.binance.com/si-LK/register?ref=V2H9AFPY
Can you be more specific about the content of your article? After reading it, I still have some doubts. Hope you can help me.
Can you be more specific about the content of your article? After reading it, I still have some doubts. Hope you can help me.
I don’t think the title of your article matches the content lol. Just kidding, mainly because I had some doubts after reading the article.
Your point of view caught my eye and was very interesting. Thanks. I have a question for you.
I don’t think the title of your article matches the content lol. Just kidding, mainly because I had some doubts after reading the article.
Your article helped me a lot, is there any more related content? Thanks!
Can you be more specific about the content of your article? After reading it, I still have some doubts. Hope you can help me.
Can you be more specific about the content of your article? After reading it, I still have some doubts. Hope you can help me.
Thanks for sharing. I read many of your blog posts, cool, your blog is very good. https://accounts.binance.com/register?ref=P9L9FQKY
Can you be more specific about the content of your article? After reading it, I still have some doubts. Hope you can help me.
Thank you for your sharing. I am worried that I lack creative ideas. It is your article that makes me full of hope. Thank you. But, I have a question, can you help me?
Your point of view caught my eye and was very interesting. Thanks. I have a question for you.
Your point of view caught my eye and was very interesting. Thanks. I have a question for you.
Can you be more specific about the content of your article? After reading it, I still have some doubts. Hope you can help me.
Your article helped me a lot, is there any more related content? Thanks!
Thank you for your sharing. I am worried that I lack creative ideas. It is your article that makes me full of hope. Thank you. But, I have a question, can you help me?
Can you be more specific about the content of your article? After reading it, I still have some doubts. Hope you can help me.
Thank you for your sharing. I am worried that I lack creative ideas. It is your article that makes me full of hope. Thank you. But, I have a question, can you help me?